Глубина резания, скорость резания и подача. Режимы резания. Подачи при черновом обтачивании стали твердосплавными резцами без дополнительной режущей кромки
Продольным называют точение, при котором направление движения подачи параллельно оси заготовки. На токарных станках движение резания -- вращение -- придано заготовке, а движение подачи -- поступательное перемещение -- резцу. На круглопалочных станках вращается режущий инструмент, а движение подачи придано заготовке. Истинная траектория резания -- винтовая линия.
Различают чистовое и черновое точение.
Чистовое точение (рис.2, а) выполняют резцом с плоскими рабочими поверхностями и прямолинейными режущими кромками -- главной и вспомогательной. Положение режущих кромок относительно оси вращения заготовки характеризуется главным углом в плане и вспомогательным углом в плане. Величина вспомогательного угла в плане определяет глубину кинематических неровностей, поэтому не может быть больше. Положение граней, образующих главную режущую кромку, характеризуют задним углом, углом заточки и передним углом.
Главная режущая кромка производит поперечно-торцовое резание, характеризующееся углом наклона волокон древесины.
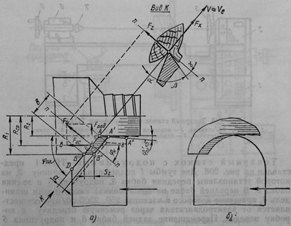
Рис. 2. Продольное точение чистовое (а) и черновое (б)
Угол наклона замеряют между направлением волокон и нормалью.
Черновое точение (рис. 2, б) производят желобчатыми резцами с полукруглой режущей кромкой. Поперечное сечение стружки серповидное, толщина стружки на периферии заготовки максимальная, а вблизи поверхности детали незначительная даже при большой подаче на резец. Это позволяет применять подачу на резец до 2 мм, тогда как при чистовом точении -- не более 0,8 мм.
> Наладка токарных станков
При наладке токарных станков необходимо: выбрать резец и закрепить его в резцедержателе (для станков с механической подачей); установить планшайбу или зажимный патрон; выбрать и закрепить подручник (для станков с ручной подачей) или копирную линейку (для станков с механической подачей); установить и закрепить обрабатываемую заготовку в станке; опробовать станок на холостом ходу; установить частоту вращения шпинделя и скорость подачи; обработать и проконтролировать пробные детали.
Требуемый резец выбирают в зависимости от характера выполняемой работы. Для первоначальной черновой обработки используют обдирочный резец, для окончательной -- чистовой резец с прямой режущей кромкой. При механической подаче резец крепят в резцедержателе винтами. Для уменьшения времени на переналадку применяют специальные поворотные головки, где одновременно укрепляют несколько резцов различного назначения.
При ручных работах необходимо проверить надежность крепления резца к деревянной рукоятке. Воспрещается использовать неисправный режущий инструмент.
Средства крепления заготовки подбирают в зависимости от её формы и размеров. Для крепления длинных заготовок (рис. 3, а) используют передний и задний центры. Передний центр 2 выполнен в виде трехзубого поводка с коническим хвостовиком, которым он вставляется в конусное отверстие шпинделя 1. Задний центр 4 имеет конусную и заостренную части и закрепляется в пиноли 5 задней бабки 6. Для уменьшения трения и повышения надежности крепления заготовки задний центр устанавливают на подшипник, что обеспечивает его вращение с заготовкой 3.
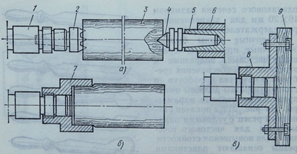
Рис. 3. Крепление заготовки в токарных станках: а - в центрах, б - в патроне, в - на планшайбе; 1 - шпиндель, 2 - передний центр, 3 - заготовка, 4 - задний центр, 5 - пиноль, 6 - задняя бабка, 7 - патрон, 8 - план
В зависимости от длины обрабатываемой заготовки заднюю бабку перемещают по направляющим станины и фиксируют в заданном положении. Закрепляют заготовку, выдвигая пиноль из бабки до тех пор, пока центры внедрятся в торцы заготовки и будут надежно удерживать ее при вращении. Для точения конусных деталей корпус задней бабки следует переместить в поперечном направлении регулировочным винтом и зафиксировать стопорным устройством. Патроны предназначены для крепления коротких заготовок (рис. 3, б). Патрон 7 имеет резьбу, посредством которой он навинчивается на шпиндель. Заготовку укрепляют в патроне путем плотной посадки ее конца в отверстие патрона. Используют также цанговые патроны и патроны с раздвижными кулачками.
Для закрепления заготовок малой длины и большого диаметра служат планшайбы 8 (рис. 3, в), навинчиваемые на шпиндель. Заготовку крепят к планшайбе винтами или болтами 9.
Подручник устанавливают на станине так, чтобы его рабочая кромка была на уровне центров и находилась вблизи образующей обрабатываемой заготовки, но не касалась ее. По мере уменьшения диаметра и при обработке длинных заготовок подручник последовательно переставляют в новое положение по направляющим станины. При обработке фасонных изделий на задней стороне станины на кронштейнах укрепляют копирную линейку, форма которой подобна форме готовой детали. При включении подачи суппорт перемещается по криволинейной траектории и резец воспроизводит заданную форму детали.
Частоту вращения шпинделя выбирают в зависимости от диаметра заготовки и ее прочности. При больших диаметрах следует устанавливать минимальную частоту вращения шпинделя. При установке планшайбы диаметром 400 мм частота вращения шпинделя не должна превышать 800 об/мин. Частоту вращения уменьшают рукояткой переключения пары зубчатых колес или изменением частоты вращения многоскоростного электродвигателя. Скорость резания для древесины мягких пород должна составлять 10...12 м/с, твердых -- 0,5...3 м/с.
Продольная подача на один оборот шпинделя должна составлять: для черновой обработки 1,6...2 мм, для чистовой -- не более 0,8 мм. Чем выше требования к шероховатости поверхности, тем меньше должна быть продольная подача. Поперечная подача на один оборот шпинделя не должна превышать 1,2 мм. Перед пуском станка необходимо убедиться в надежном креплении заготовки и установить ограждение.
После черновой обработки детали резец заменяют и выполняют чистовое точение с малой подачей. Стружка в этом случае должна быть по возможности непрерывной ленточной и равномерной толщины.
В процессе обработки периодически контролируют форму детали шаблоном или калибром. При использовании калибра или измерительного инструмента со шкалой станок выключают и только после полной остановки детали ее измеряют.
Закончив наладку, производят пробную обработку детали и контролируют ее размеры калибром или мерительным инструментом со шкалой.
В понятие «режимы резания» входят глубина резания t, подача S и скорость резания V.
Токарная обработка должна вестись на таких режимах, при которых наиболее полно используются мощность станка и стойкость инструмента, обеспечивается высокое качество обработки при минимальной ее себестоимости и создаются безопасные условия работы.
При назначении режимов резания сначала устанавливают глубину резания, затем выбирают подачу и в зависимости от них определяют скорость резания.
Глубина резания определяется величиной припуска на обработку. Глубина резания оказывает большое влияние на силы резания, поэтому иногда возникает необходимость разделить припуск на несколько проходов.
Суммарный припуск разделяется следующим образом: 60%—на черновую обработку, 20—30 % — на получистовую и 10—20 % —на чистовую. При чистовой обработке глубина резания назначается в зависимости от необходимой степени точности и качества поверхности.
Величина подачи ограничивается силами, действующими в процессе резания: эти силы могут привести к поломке режущего инструмента, деформации и искажению формы заготовки, поломке станка. Подача выбирается максимально возможной, так как она непосредственно влияет на производительность обработки.
Обычно подача назначается из таблиц справочников по режимам резания, составленным на основе специальных исследований и изучения опыта работы машиностроительных заводов. Выбранная подача согласуется с кинематикой станка. При этом выбирается ближайшая меньшая из имеющихся на станке. Выбрать величину подачи можно из табл. 16—19.
Скорость резания зависит от материала режущей части резца, обрабатываемого материала, глубины резания, подачи и других факторов. Чем большую скорость резания позволяет достичь инструмент при одной и той же стойкости, тем выше его режущие свойства, тем более он производителен.
Стойкость резцов из быстрорежущих сталей уменьшается с увеличением скорости резания. Рациональная скорость резания для этих резцов — от 20 до 50 м/мин.
Стойкость резцов, оснащенных пластинками твердых сплавов, находится в более сложной зависимости от скорости резания. Рациональная скорость резания для этих резцов находится в пределах V=80—140 м/мин при стойкости T=30—60 мин. Скорость резания уменьшается с увеличением сопротивления резанию, которое приводит к возникновению больших сил, высокой температуры, интенсивному износу режущего инструмента.
С большей скоростью резания обрабатываются автоматные стали, цветные и легкие сплавы. Алюминий обрабатывается со скоростью в 5—6 раз большей, чем скорость обработки углеродистой конструкционной стали.
Подача и глубина резания определяют нагрузку на резец и температуру резания. С увеличением подачи и глубины резания интенсивнее износ резца, что ограничивает скорость резания. Для достижения большей производительности выгоднее работать с большими сечениями среза за счет уменьшения скорости резания. Например, при увеличении подачи в 2 раза (с 0,3 до 0,6 мм/об) скорость резания необходимо уменьшить на 20—25 %. При удвоении глубины резания скорость резания должна быть уменьшена на 10—15 %. На практике скорость резания увеличивают после того, как достигнуты предельные величины по глубине резания и подаче.
Таблица 16 Подачи при черновом обтачивании стали твердосплавными резцами без дополнительной режущей кромки
Примечания:
1. Меньшие значения подач соответствуют меньшим размерам державки резца и более прочным обрабатываемым материалам.
2. При обработке прерывистых поверхностей, т. е. при работе с ударными нагрузками, табличные значения подач следует умножать на коэффициент 0,75—0,85.
3. При обработке жаропрочных сталей и сплавов подачи свыше 1 мм/об не применять.
4. При обработке с глубиной резания до 8 мм быстрорежущими резцами табличные значения подач можно увеличить в 1,1—1,3 раза.
При черновом точении сталей быстрорежущими резцами обильное охлаждение смазочно-охлаждающими жидкостями (8— 12 л/мин) повышает скорость резания на 20—30 %. При чистовом точении интенсивность охлаждения 4—6 л/мин обеспечивает повышение скорости резания на 8-10%.
Для твердосплавного инструмента особенно необходимо постоянное охлаждение, так как в случае прерывистого охлаждения могут образоваться трещины на пластинке и резец выйдет из строя.
Таблица 17 Подачи при чистовом обтачивании твердосплавными и быстрорежущими резцами
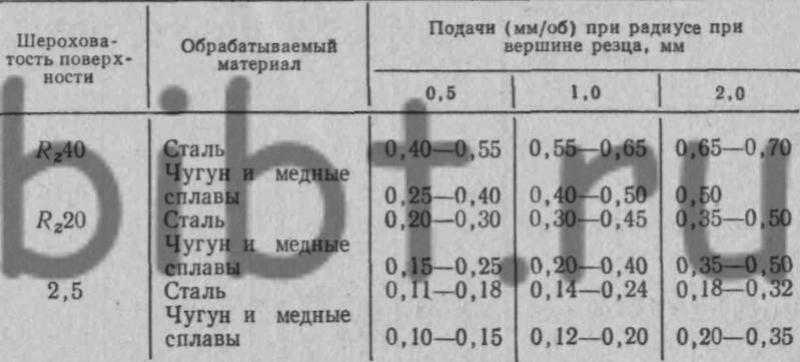
Примечания:
1. Значения подач даны для резцов со вспомогательным углом в плане =10—15°, при уменьшении последнего до 5° значения подач могут быть повышены на 20 %.
2. При чистовой обработке стали в зависимости от скорости резания величина подачи вычисляется умножением на поправочный коэффициент: при скорости резания до 50 м/мин принимать коэффициент =0,85, при скорости резания от 50 до 100 м/мин — 1,0, при скорости выше 100 м/мин — 1,2.
В зависимости от прочности стали величину подачи находят умножением на поправочный коэффициент:
при σ b до 50 кгс/мм 2 (0,49*10 5 Па) коэффициент 0,7;
при σ b от 50 до 70 кгс/мм 2 (0,49*10 5 Па -0,68*10 5 Па.)-0,75;
при σ b от 70 до 90 кгс/мм 2 (0,68*10 5 Па - 0,88*10 5 Па) -1,0;
при σ b от 90 до 110 кгс/мм 2 (0,88*10 5 Па - 1,07* 10 5 Па.) - 1,25.
Допустимая величина износа резцов определяет выбор скорости резания.
При выборе скорости резания пользуются нормативными данными, приведенными в табл. 20—24. При этом необходимо учитывать конкретные условия работы.
Таблица 18 Подачи при черновом обтачивании стали и чугуна минералокерамичёскими резцами
Примечание: * 75 кгс/мм 2 = 0,73*10 5 Па.
Принятые режимы резания проверяются по мощности электродвигателя станка. При этом определяется мощность, необходимая для работы с выбранными режимами, и сравнивается с фактической мощностью электродвигателя. Если мощность электродвигателя оказывается недостаточной, необходимо понизить скорость резания.
Пример определения режимов резания с помощью справочных таблиц
Исходные данные:
обрабатываемая заготовка — валик D = 80 мм,
материал — сталь 45, σ b = 85 кгс/мм 2 (σ b =0,8*10 5 Па.) ,
резец —прямой проходной, оснащенный пластинкой из твердого сплава Т5К10, параметры φ=60°, φ 1 =30°, r= 1,0 мм, сечение 16X25, заданная стойкость 60 мин,
припуск на обработку 3 мм, шероховатость поверхности Rz = 20.
Станок 16К20 (N = 10 кВт, n=0,8).
Таблица 19 Подачи при чистовом обтачивании стали и чугуна минералокерамическими резцами
Примечание. В зависимости от прочности обрабатываемого материала величину подачи находят умножением на поправочный коэффициент:
при σ b до 50 кгс/мм 2 (0,49*10 5 Па) коэффициент 0,70;
при σ b от 50 до 70 кгс/мм 2 (0,49*10 5 Па-0,68*10 5 Па) - коэффициент 0,75;
при σ b от 70 до 90 кгс/мм 2 (0,68*10 5 Па-0,88*10 5 Па) - коэффициент 1,00;
при σ b от 90 до 110 кгс/мм 2 (0,88*10 5 Па-1,07*10 5 Па)- коэффициент 1,25.
Последовательность определения режимов резания:
1. Назначаем глубину резания. Учитывая, что требования к шероховатости поверхности невысокие, снимаем припуск за один проход: t = 3 мм.
2. Из справочной табл. 17 выписываем значение подачи, обеспечивающей заданную величину шероховатости поверхности: S = 0,3— —0,45 мм/об. Принимаем имеющееся в паспорте станка значение 5 = 0,4 мм/об.
3. По табл. 20 находим значение скорости резания. При глубине резания t = 3 мм и подаче 0,3 мм/об V табл. = 198 м/мин, а при подаче 0,5 мм/об V табл.= 166 м/мин. Принимаем среднее значение для подачи 0,4 мм/об V табл.=182 М/МИН.
По табл. 22 находим поправочный коэффициент для σ b = 85 кгс/мм 2: K2 = 0,88.
Оптимальная скорость резания определяется из произведения V = V табл.* К2= 182*0,88= 160 м/мин
4. Определяем
частоту вращения шпинделя:
Уточняем по паспортным данным станка n = 630 об/мин.
Таблица 20 Скорость резания при черновом обтачивании углеродистой, кремнистой, хромоникелевой сталей и стального литья резцами с пластинками из твердого сплава
Примечание. Значения скоростей резания V даны для следующих условий обработки:
стойкость резца T—60 мин;
резец без дополнительной режущей кромки φ 1 >0;
обрабатываемый материал — сталь с пределом прочности 70—80 кгс/мм 2 (0,68*10 5 Па - 0,78*10 5 Па.)
материал резца — твердый сплав Т15К6;
главный угол в плане φ —45°.
Для измененных условий работы см. поправочные коэффициенты в табл. 22.
Таблица 21 Скорость резания при чистовом обтачивании углеродистой, хромистой, хромоникелевой сталей и стального литья твердосплавными резцами без дополнительной режущей кромки
Таблица 22 Поправочные коэффициенты скорости резания твердосплавными резцами с
углом φ>0
Таблица 23 Скорость резания при черновом обтачивании серого чугуна твердосплавными резцами без дополнительной режущей кромки
Примечание. Поправочные коэффициенты см. в табл. 22.
Таблица 24 Скорость резания при чистовом обтачивании серого чугуна твердосплавными резцами без дополнительной режущей кромки
Примечание. Поправочные коэффициенты см. в табл. 22.
К основным режущим инструментам, используемым при , относится резец, геометрические параметры которого определяют его технические возможности, точность и эффективность обработки. Разбираться в таких параметрах должен любой специалист, решивший посвятить себя токарному делу, поскольку правильный выбор углов резца увеличивает как продолжительность эксплуатации инструмента, так и производительность обработки.
Параметры токарных резцов
Любой токарный резец образуют державка, необходимая для фиксации инструмента в держателе токарного станка, и рабочая головка, обеспечивающая резание металла. Для рассмотрения геометрических параметров токарного резца за образец лучше взять проходной инструмент.
На режущей части токарного резца данного типа выделяют три поверхности:
- переднюю (по ней в ходе обработки заготовки осуществляется сход металлической стружки);
- задние – главную и вспомогательную (обе повернуты своей лицевой частью к обрабатываемой детали).
Кромка инструмента, называемая режущей (и непосредственно участвующая в обработке), образована пересечением его передней и главной задней поверхностей. В геометрии токарного резца выделяют и вспомогательную режущую кромку. Она, соответственно, образована пересечением передней поверхности со вспомогательной задней.
Точку, в которой пересекаются главная и вспомогательная режущие кромки, принято называть вершиной резца. Последняя при резании металла испытывает колоссальные нагрузки, приводящие к ее поломке. Чтобы повысить стойкость вершины резца, ее в процессе заточки не заостряют, а немного скругляют. Это требует введения такого параметра, как радиус при вершине. Есть и еще один способ увеличения стойкости вершины токарного резца – формирование переходной режущей кромки, имеющей прямолинейную форму.
Важнейшими геометрическими параметрами резцов для токарной обработки являются их углы, которые определяют взаимное расположение поверхностей инструмента. Параметры углов варьируются в зависимости от разновидности токарного резца и от ряда других факторов:
- материала изготовления инструмента;
- условий его работы;
- характеристик материала, который предстоит обрабатывать.
Углы резцов для токарной обработки
Чтобы правильно определять углы токарного инструмента, их точные величины, их рассматривают в так называемых исходных плоскостях.
- Основная плоскость параллельна направлениям подач токарного резца (продольной и поперечной) и совпадает с его опорной поверхностью.
- Плоскость резания включает главную режущую кромку и проходит по касательной по отношению к поверхности обработки. Эта плоскость перпендикулярна к основной.
- Главная секущая плоскость пересекает главную режущую кромку и располагается перпендикулярно по отношению к проекции, которую данная кромка откладывает на основную плоскость. Есть еще и вспомогательная плоскость секущего типа, которая, соответственно, перпендикулярна проекции, откладываемой на основную плоскость вспомогательной режущей кромкой.
Как уже говорилось выше, измеряются именно в данных плоскостях и те из них, которые измеряют в плоскости, называемой главной секущей, обозначают как главные. Это, в частности, главный передний, главный задний углы, а также углы заострения и резания.
Одним из важнейших считается главный задний угол токарного резца, который минимизирует трение, возникающее при взаимодействии задней поверхности инструмента с деталью, которую в данный момент обрабатывают (а значит, уменьшает нагрев резца и продлевает срок его службы). Образуется этот угол поверхностью резца (главной задней) и плоскостью резания. Выбирая данный угол при заточке инструмента, учитывают тип обработки и материал заготовки. При этом следует знать, что сильное увеличение размера заднего угла приводит к быстрому выходу токарного резца из строя.
Прочность и стойкость режущего инструмента, усилия, возникающие в ходе обработки, определяются параметрами переднего угла. Он находится между передней поверхностью токарного резца и плоскостью, в которой расположена главная режущая кромка (эта плоскость перпендикулярна плоскости резания). При заточке токарного резца, учитывают ряд факторов, влияющих на величину данного угла:
- материал заготовки и самого инструмента;
- форму передней поверхности;
- условия, в которых резец будет использоваться.
Увеличение значения переднего угла, с одной стороны, позволяет улучшить чистоту обработки, а с другой – провоцирует снижение прочности и стойкости токарного резца. Такой угол, получаемый в результате заточки, может иметь положительное и отрицательное значение.
Токарные резцы с передними углами, которые имеют отрицательные значения, отличаются высокой прочностью, но выполнять обработку такими инструментами затруднительно. Обычно заточку с передним углом, который имеет положительное значение, используют, когда предстоит обработка заготовки из вязкого материала, а также когда материал изготовления инструмента отличается высокой прочностью.
Резцы с передними углами, имеющими отрицательное значение, применяют при обработке материалов с высокой твердостью и прочностью, при выполнении прерывистого резания, когда материал изготовления инструмента не обладает достаточной прочностью на изгиб и плохо воспринимает ударные нагрузки.
Параметрами, характеризующими геометрию резца для токарной обработки, также являются углы резания и заострения. Угол резания, величина которого может варьироваться в пределах 60–100 0 , находится между поверхностью инструмента, называемой передней, и плоскостью резания.
Величина данного угла напрямую зависит от твердости, которой обладает обрабатываемый металл: чем она выше, тем больше его значение. Угол заострения полностью соответствует своему названию, он измеряется между главной передней и главной задней поверхностями инструмента и характеризует степень заострения его вершины.
Характеризуют токарный резец и углы в плане. Это главный, измеряемый между направлением продольной подачи и проекцией, которую откладывает главная режущая кромка на основную плоскость, и вспомогательный, образуемый проекцией вспомогательной режущей кромки на основную плоскость и направлением продольной подачи.
При заточке указанные углы выбираются не произвольно, а в зависимости от типа токарной обработки и жесткости, которой обладает система «станок – инструмент – заготовка». Так, обработку большей части металлов можно проводить инструментами с главным углом в плане, равным 45 0 , но тонкие и длинные заготовки следует обрабатывать резцами, у которых величина этого угла находится в промежутке 60–90 0 . Это необходимо для того, чтобы исключить прогиб и дрожание детали.
Вспомогательный угол в плане одновременно коррелирует с чистотой обработки и со стойкостью резца. С его уменьшением возрастает чистота обработки и увеличивается стойкость инструмента.
Помимо рассмотренных выше в геометрии токарных резцов различают углы.
Для того чтобы обрабатывать заготовку резанием и получать в результате этого обработанные поверхности той или иной детали, заготовка и применяемый режущий инструмент должны совершать определенные движения. Эти движения разделяются на основные (служащие для осуществления процесса резания) и вспомогательные (служащие для подготовки к процессу резания и для завершения операции). Основных движений два:
- движение резания (или главное движение);
- движение подачи.
При обработке на токарном станке движение резания - вращательное - совершает заготовка, тем или иным способом скрепленная со шпинделем станка, а движение подачи - поступательное - получает режущий инструмент (резец), жестко закрепленный в резцедержателе. Движение позволяет осуществлять процесс резания (образования стружки) , движение же подачи дает возможность вести этот процесс (обработку) по всей длине заготовки (рис. ч.16).
Глубина резания (t) -величина срезаемого слоя за один проход, измеренная в направлении, перпендикулярном обработанной поверхности. Глубина резания всегда перпендикулярна направлению движения подачи (см. также рис. 11 -14). При наружном продольном точении (рис. 16) она представляет собой полуразность между диаметром заготовки и диаметром обработанной поверхности, полученной после одного прохода:
Скорость резания υ - величина перемещения точки режущей кромки относительно поверхности в единицу времени в процессе осуществления движения резания*.
При токарной обработке, когда обрабатываемая заготовка вращается с частотой n об/мин, скорости резания в точках МК режущей кромки будет величиной переменной. Максимальная скорость:
где D - наибольший диаметр поверхности в мм.
* Скорость резания является функцией частоты вращения заготовки и скорости перемещения резца (подачи).
Если скорость будет известна, то легко определить частоту вращения:
При продольном точении скорость резания имеет постоянную величину на протяжении всего времени резания (если диаметр заготовки вдоль всей ее длины одинаков, а частота вращения неизменна). При подрезке торца, когда резец перемещается от периферии заготовки к центру, скорость резания при постоянной частоте вращения переменна. Она имеет наибольшее значение у периферии и равна нулю в центре (рис. 17). Переменной вдоль обработанной поверхности скорость резания будет и при отрезке (см. рис. 14). Однако в этих случаях учитывают максимальную скорость резания.
Подача s (точнее, скорость подачи) - величина перемещения режущей кромки относительно обработанной поверхности в единицу времени в направлении движения подачи. При токарной обработке может быть продольная подача , когда резец перемещается в направлении, параллельном оси заготовки (см. рис. 16); поперечная подача , когда резец перемещается в направлении, перпендикулярном оси заготовки (см. рис. 17), и наклонная подача - под углом к оси заготовки (например, при точении конической поверхности).
Различают подачу за один оборот заготовки, т. е. величину относительного перемещения резца за время одного оборота заготовки (из положения I резец переместился в положение II, рис. 16), и минутную подачу , т. е. величину относительного перемещения резца за 1 мин. Минутная подача обозначается S м (мм/мин), а подача за одни оборот - s (мм/об). Между ними существует следующая зависимость.