Обработка деталей класса «валы. Изготовление детали "вал ступенчатый"
Этот ТП включает следующие операции:
Обработка торцов, центрирование
Токарная обработка (точение) шеек валов
Предварительное шлифование
Фрезерование шпоночных пазов
Фрезерование шлицев
Обработка резьбы
Термообработка
Исправление центровых отверстий
Чистовое шлифование шеек вала
Шлифование шлицев
Калибрование резьбы и зачистка заусенцев
Промывка
Контроль
1.2.1. Обработка торцов вала и центрирование
В единичном и мелкосерийном производствах торцы обрабатывают на токарных и фрезерных станках. Центрирование выполняется на сверлильных, токарных, револьверных и горизонтально-расточных станках.Центрирование может производиться или двумя инструментами (спиральным сверлом и зенкером), или же одним комбинированным центровочным сверлом. Угол конуса сверла обычно равен 60 0 , однако, для тяжелых заготовок валов его увеличивают до 75 0 или 90 0 .
В ряде случаев у режущих инструментов выполняют дополнительную фаску с углом 120 0 , которая предохраняет центровое отверстие от забоин при случайном повреждении торцов вала.
В серийном и массовом производствах применяют фрезерно-центровальные полуавтоматы, на которых одновременно фрезеруются 2 торца (позиция 2 на рис. 1.3.), затем центруются 2 отверстия (позиция 3).
Рис. 1.3. – Схема обработки вала на фрезерно-центровальном полуавтомате.
1.2.2. Обтачивание валов
Токарная обработка валов обычно включает черновые и чистовые операции. При черновом точении снимают большую часть припуска, работая с большей глубиной резания и большой скоростью движения подачи.В единичном и мелкосерийном производствах обтачивание выполняется на токарных универсальных станках. При обработке ступенчатых валов используются различные схемы резания, например, представленная на рис. 1.4.
В схеме на рис. 1.4., в суммарная длина перемещения резца , т.е. меньше, чем в схеме на рис. 1.4., а. Однако, число рабочих и вспомогательных ходов больше.
Рис. 1.4. – Схемы обтачивания валов
При выборе схемы резания стремятся получить максимальную производительность и минимальную себестоимость операции. При этом учитывают размеры вала, способ простановки и контроля размеров, допуски и другие факторы.
Иногда при большой разнице в диаметрах ступеней стремятся как можно дольше не ослаблять вал и ступени наименьшего диаметра обтачивать в последнюю очередь.
При обтачивании длинных не жестких валов применяют неподвижные или подвижные люнеты. Неподвижный люнет устанавливается на станине станка. Подвижный люнет движется на суппорте и его кулачки следуют за резцом (рис. 1.5., а).
Если же необходимо обеспечить соосность обработанной поверхности с поверхностью 2 (рис. 1.5., б), то кулачки люнета располагают впереди резца на поверхности.
Рис. 1.5. – Схема обтачивания вала с использованием люнета
В настоящее время в мелкосерийном производстве используются станки с ЧПУ. Они позволяют автоматизировать цикл обработки, использовать повышенные режимы резания, повысить производительность, применить многостаночное обслуживание, сократить дефицит высококвалифицированной рабочей силы, уменьшить брак, сократить сроки подготовки производства.
В крупносерийном и массовом производствах для обтачивания валов применяют многорезцовые и гидрокопировальные станки и полуавтоматы. Обычно они имеют 2 суппорта – продольный и поперечный, служащие для подрезания торцов , растачивания канавок и фасонного точения.
Суппорты могут работать одновременно. На многорезцовых станках в случае необходимости применяют обтачивание с врезанием и последующей продольной подачей (рис. 1.6., б).
Рис. 1.6. – Схема обтачивания вала на многорезцовом полуавтомате
По сравнению с универсальными токарными станками, многорезцовые станки позволяют повысить производительность за счет сокращения длины рабочего хода, одновременной работой резцов, а также за счет устранения затрат времени на смену резцов, поворот резцедержателя и холостые перемещения суппорта.
На продольном суппорте гидрокопировального станка устанавливается 1 резец, который настраивается на размер только по одной шейке вала. Получение остальных размеров обеспечивается копиром и следящей системой. Одновременно сокращается число измерений, применяется более высокий режим резания, чем при работе с ручным включением подач.
Валы обтачиваются за один или несколько рабочих ходов, при этом смена копиров производится автоматически за счет поворота барабана с копиром.
В тех случаях, когда вал может быть обработан на гидрокопировальном и одношпиндельном многорезцовом полуавтомате, выбор оборудования делается на основании технико-экономического анализа.
При этом учитываются следующие соображения:
При многорезцовом обтачивании с делением длины обработки, длина рабочего хода меньше, чем при копировальной обработки.
Время наладки и подналадки гидрокопировальных станков значительно меньше, чем для многорезцовых станков.
Количество резцов и режимы резания на многорезцовых станках часто ограничиваются податливостью заготовки и недостаточной мощностью станка. На гидрокопировальном станке можно работать с большими скоростями подачи главного движения резания.
В связи с изложенным производительность гидрокопировальных станков во многих случаях выше.
На точность многорезцовой обработки влияют погрешности относительного расположения и неодинаковый износ резцов. При обработке одной поверхности несколькими резцами на границах участков образуются уступы. На гидрокопировальных станках эти погрешности отсутствуют, поэтому удается получать более высокую точность размеров и меньшую шероховатость.
1.2.3. Отделочная обработка наружных цилиндрических поверхностей
Для отделочной обработки наружных цилиндрических поверхностей применяют тонкое точение, шлифование, полирование, притирку, суперфиниш, обтачивание роликами и т.п.1.2.2.1. Тонкое точение
Тонкое точение чаще применяется для отделочной обработки заготовок из цветных металлов и сплавов , реже для заготовок из стали и чугуна. Объясняется это трудностями шлифования цветных сплавов вследствие «засаливания» шлифовального круга.Обработка производится алмазными, композитными, металлокерамическими резцами и резцами, оснащенными твердыми сплавами, при высоких скоростях главного движения резания, малых скоростях движения подач и глубинах резания.
Тонкое точение позволяет получить 6…7 квалитет точности обработки и шероховатость поверхности мкм.
Производительность обработки выше, чем при шлифовании. В крупносерийном и массовом производствах для тонкого точения применяют специальные быстроходные станки высокой точности и виброустойчивости.
1.2.2.2. Шлифование
Оно является основным методом чистовой обработки наружных цилиндрических поверхностей. Преимуществами шлифования является возможность исправления погрешностей заготовки после термообработки. При обычном тонком шлифовании осуществляется обработка по 6-7 квалитету точности, при шероховатости поверхности 1,2…0,3 мкм.Тонкое шлифование дает 5 квалитет точности и шероховатость 0,16…0,8 мкм. Оно осуществляется малозернистым кругом при большой скорости его вращения, малой скорости вращения заготовки, малой глубине резания.
Шлифование осуществляется на кругло- и бесцентрошлифовальных станках с продольной подачей круга или по способу вращения (рис. 1.7.)
А – с продольной подачей; Б, В – по способу (методу) вращения
Рис. 1.7. – Схема шлифования на кругло-шлифовальном станке:
Шлифование по способу вращения более производительно, применяется в крупносерийном и массовом производстве при обработке цилиндрических и фасонных поверхностей.
Для одновременного шлифования нескольких шеек используются специальные станки, работающие несколькими кругами с целью сокращения вспомогательного времени при шлифовании, применяются устройства активного контроля, позволяющие измерять заготовки в процессе шлифования, а также устройства автоматической остановки станка при достижении заданного размера.
При бесцентровом шлифовании (рис. 1.8.) заготовка помещается между двумя шлифующими кругами, из которых один (большего диаметра) является шлифующим, а с другой – ведущим.
Рис. 1.8. – Схема бесцентрового шлифования
Шлифующий круг 1 вращается со скоростью 20-35 м/с, ведущий круг 2 – со скоростью 20-30 м/мин. Заготовка 3 ничем не закрепляется, но поддерживается опорой 4 со скосом, направленным в сторону ведущего круга.
Сила сцепления заготовки с ведущим кругом больше, чем со шлифующим. Это объясняется следующими причинами:
Увеличение силы резания при уменьшении скорости вращения круга
Изготовление ведущих кругов на связи, увеличивающей коэффициент трения между кругом и заготовкой.
При бесцентровом шлифовании с продольным движением подачи заготовки ось ведущего круга не параллельна оси шлифующего круга. Благодаря этому без специального механизма подачи обеспечивается перемещение заготовки со скоростью где
- скорость вращения ведущего круга.
С увеличением угла скрещивания осей кругов производительность обработки возрастает, но качество поверхности ухудшается, поэтому обычно
.
Для повышения точности обработки иногда выполняют сквозное шлифование за несколько рабочих ходов. В крупносерийном и массовом производствах обработка может выполняться последовательно на нескольких станках, соединенных в автолинию.
При бесцентровом шлифовании по способу врезания оси кругов чаще всего параллельны. Сначала ведущий круг отводится от шлифующего, и заготовка устанавливается на опору, затем ведущий круг подводится к заготовке и осуществляется поперечная подача до получения заданного размера.
По сравнению со шлифованием в центрах бесцентровое шлифование имеет следующие преимущества:
Отпадает необходимость центрирования заготовки, что особенно важно для деталей, обрабатываемых на револьверных станках и автоматах;
Значительно уменьшаются припуски на обработку, т.к., благодаря использованию в качестве технологической базы обрабатываемой поверхности, устраняется влияние на припуск погрешности зацентровки;
Отпадает необходимость использования люнетов при шлифовании длинных и тонких валов;
Бесцентрошлифовальные станки сравнительно легко автоматизируются и встраиваются в автолинию;
Обеспечивается более высокая производительность, чем при шлифовании в центрах;
Благодаря простоте управления станком, высокая точность достигается при средней квалификации шлифовщика ;
Погрешность обработки, вызываемая износом круга, в 2 раза меньше, чем при шлифовании в центрах, т.к. износ круга непосредственно отражается на величине диаметра заготовки, а не на величине радиуса.
1. Затраты времени на наладку и регулировку таких станков достаточно велики и окупаются при больших партиях заготовок. Поэтому бесцентровое шлифование чаще всего применяют в автотракторной и подшипниковой промышленности.
2. шпоночные пазы, канавки, отверстия, разрывы обрабатываемой поверхности препятствуют нормальной работе и даже делают её невозможной.
3. При бесцентровом шлифовании трудно обеспечить круглость обрабатываемой поверхности.
4. Затрудняется достижение соосности шлифуемой поверхности с другими ранее обработанными поверхностями.
1.2.3.3. Полирование и суперфиниш
Полирование мягкими кругами из войлока, фетра или лентой ведется при высоких скоростях инструмента, на поверхность которого наносится смесь мелкозернистого абразивного порошка и смазки. Полирование обеспечивает малую шероховатость поверхности (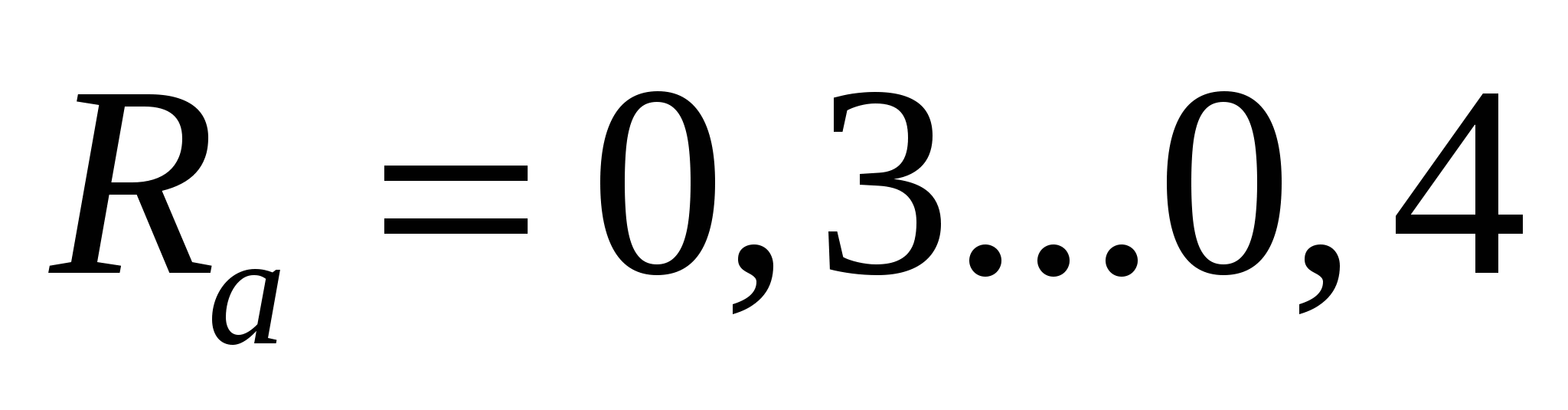
Суперфиниш (отделка колеблющимися брусками) реализует принцип неповторяющегося следа, который заключается в том, что ни одно зерно абразива не проходит дважды по одному и тому же пути. Для этого, кроме вращающейся заготовки, с небольшой скоростью (1-2,5 м/мин) и продольного перемещения брусков (рис. 1.9.) им сообщают от 200 до 1000 колебаний в минуту с малой амплитудой.
За счет колебательных движений, малой зернистости брусков и малого давления обеспечивается малая шероховатость заготовки ( мкм).
Рис. 1.9. – Схема обработки вала абразивными брусками.
Процесс ведется с применением смазочно-охлаждающей жидкости и протекает следующим образом: в начальный момент площадь контакта брусков с обрабатываемой поверхностью мала и давление бруска оказывается значительным, что вызывает интенсивный съём металла. В дальнейшем бруски прирабатываются, давление уменьшается, и процесс резания теряет свою интенсивность.
Суперфиниш не улучшает макрогеометрию заготовки, поэтому предварительная обработка должна обеспечить правильную геометрическую форму детали. Припуск под суперфиниш обычно не оставляют.
1.2.4. Обработка резьбы
1.2.4.1. Нарезание резьбы резцами и гребенками
При нарезании резьбы на токарных станках заготовке сообщают вращение , а резцу – перемещение вдоль оси заготовки с подачей на оборот, равной шагу резьбы. Точность шага определяется точностью кинематической цепи станка, а точность профиля резьбы – точностью заточки и установки резца. Поэтому в процессе обработки токарь обычно контролирует ?????????????????????.При нарезании резьбы за несколько рабочих ходов движение поперечной подачи резца может осуществляться, например, по схемам, показанным на рис. 1.10. (а,б). При использовании схемы (а) обеспечивается лучшее качество обработанной поверхности, а при работе по схеме (б) упрощается форма срезаемого слоя, облегчается процесс резания и удаления стружки. Поэтому иногда черновую обработку выполняют по схеме (б), а последний слой срезают по схеме (а).
Рис. 1.10. – Схемы резания при обработке резьбы.
При нарезании резьбы одним резцом за несколько рабочих ходов его режущая кромка быстро притупляется и её форма искажается, поэтому рекомендуется для нарезания резьб с крупным шагом использовать 2 резца – черновой и чистовой, или же применять резьбонарезные гребенки. Благодаря уменьшению числа рабочих ходов, гребенки обеспечивают повышение производительности обработки. Недостатком стандартных гребенок является то, что их нельзя использовать для работы «в упор», т.е. для нарезания резьб, расположенных рядом с шейками большего диаметра.
Обработка резьбы на токарных станках производится обычно в следующих случаях:
При нарезании резьбы на заготовках, предварительно обточенных на том же станке, т.к. при этом сокращается вспомогательное время и повышается точность относительного расположения поверхностей.
При изготовлении точных длинных винтов.
При нарезании резьб большого диаметра или нестандартного шага и профиля, если приобретение специального высокопроизводительного инструмента не оправдывается из-за малого объема выпуска.
При нарезании прямоугольных резьб.
Увеличение производительности резьбонарезания за счет увеличения скорости главного движения резания во многих случаях оказывается затруднительным из-за сложности быстрого отвода резца, обрабатывающего резьбу, примыкающую к уступу.
В крупносерийном и массовом производствах резьбу часто нарезают на специальных полуавтоматах, обеспечивающих автоматизацию цикла многоходовой обработки. В мелкосерийном производстве целесообразно использовать станки с ЧПУ.
1.2.4.2. Фрезерование резьбы охватывающей резцовой головкой
Нарезание резьбы охватывающей головкой производится на токарно-винторезных и резьбофрезерных станках. Твердосплавные резцы 1 (рис. 1.11.) закрепляются в резцовой головке и вращаются со скоростью 150-450 м/мин. Головка устанавливается под углом к оси заготовки в соответствии с углом подъема резьбы и за каждый оборот медленно вращающейся заготовки перемещается вдоль её оси на величину шага. Наибольший эффект достигается при обработке крупных резьб.Рис. 1.11. – Схема нарезания резьбы охватывающей головкой.
1.2.4.3. Нарезание резьбы плашками и самораскрывающимися головками
При нарезании резьбы на токарно-револьверных и агрегатных станках в качестве инструмента могут использоваться плашки. Держатели плашек позволяют инструменту свободно перемещаться на небольшую величину или, как говорят, самоустанавливаться в продольном направлении. Это исключает срыв резьбы при несовпадении скорости движения плашкодержателя вдоль оси заготовки и скорости навинчивания плашки на заготовку.Основной недостаток плашек – необходимость свинчивания их после окончания нарезания резьбы, что снижает производительность и качество обработки.
При обработке резцовыми самораскрывающимися головками свинчивания не требуется и производительность значительно повышается.
1.2.4.4. Фрезерование резьбы дисковыми и гребенчатыми (групповыми) фрезами
Фрезерование дисковыми фрезами (рис. 1.12.) применяется для обработки крупных резьб при достаточно больших объемах выпуска. При этом обработка выполняется за 1-3 рабочих хода. Заготовка медленно поворачивается, а вращающаяся со скоростью главного движения фреза перемещается вдоль её оси с подачей на оборот, равной шагу резьбы.Рис. 1.12. – Схема фрезерования резьбы.
По сравнению с точением преимуществом фрезерования является более высокая производительность, возможность многостаночного обслуживания и использования рабочего невысокой квалификации.
Фрезерование гребенчатыми (групповыми) фрезами применяется для получения коротких наружных и внутренних резьб с мелким шагом.
В отличие от обработки резьб дисковой фрезой оси гребенчатой фрезы и заготовки параллельны (рис. 1.13.). Длина фрезы обычно на 2-3 шага превышает длину резьбового участка заготовки.
Рис. 1.13. – Схема фрезерования резьбы гребенчатой фрезой.
В начале обработки вращающаяся фреза перемещается в радиальном направлении и врезается в заготовку на глубину профиля резьбы. При этом за 1 оборот заготовки фреза перемещается вдоль оси на шаг резьбы (движение подачи
). Фрезерование происходит за 1,2 оборота заготовки. Причем вначале обработки 0,2 оборота необходимы для врезания фрезы, а в конце – для зачистки следов врезания.
1.2.4.5. Накатывание резьбы
Накатывание резьбы применяется в крупносерийном и массовом производствах. Помимо высокой производительности метод позволяет получить благоприятную упрочненную поверхностную структуру металла, т.к. волокна материала пластически деформируются, а не перерезаются.Резьба накатывается плоскими плашками или накатными роликами.
На плоских плашках (рис. 1.14.) имеется прямолинейная резьба (развертка резьбы) с такими же профилем и углом подъема как и у накатываемой резьбы. Резьба накатывается за один двойной ход ползуна. Число двойных ходов в минуту достигает 280.
Рис. 1.14. – Схема накатывания резьбы плашками.
Накатывание резьбы одним роликом применяется на токарных и револьверных станках и автоматах из-за односторонней радиальной силы. В этом случае возможен изгиб заготовки.
Поэтому большее распространение получило накатывание резьбы двумя роликами с радиальным движением подачи (рис. 1.15.).
Накатывание резьбы может также производиться двумя-четырьмя роликами с продольной подачей при постоянном межосевом расстоянии. По производительности накатывание роликами обычно уступает накатыванию плашками.
Рис. 1.15. – Схема накатывания резьбы роликами.
- Анализ технологических требований изготовления детали………….2
- Выбор вида финишной обработки конструктивных элементов
детали………………………………………………………………….…5
- Выбор способа установки заготовки для её обработки………………6
- Выбор вида, определение размеров заготовки, типа и
типоразмера центровых отверстий………………………………...…..6
- Составление укрупнённого маршрута изготовления детали……..….7
- Разработка операций по формированию контура детали………….....8
- Составление плана токарной и шлифовальной обработок
детали……………………………………………………………….......15
- Выбор и расчёт режимов резания…………………………………….19
- Определение затрат времени на токарную и шлифовальную
обрабоку…………………………………………………………..……30
- Заключение……………………………………………………..36
Список используемой литературы…………………………...………37
1. Анализ технологических требований изготовления детали.
Деталь изготавливается в условиях единичного производства из стали 45 ГОСТ 1050-88 твердостью НВ 280, термообработка - нормализация. Она представляет собой 5-ти ступенчатый вал длиной 360 мм. Относится к группе цилиндрических изделий. Внутри - сплошной. Основное предназначение вала передавать крутящий момент в редукторе тихоходной ступени.
Рисунок 1. Компоновочная схема
1 ступень вала под МУВП; 2 ступень вала под подшипник и уплотнение; 3 ступень вала под зубчатое колесо; 4 - заплечник вала; 5 ступень вала под подшипник;
6 канавка; 7 рабочий торец.8, 9, 10 нерабочие торцы;
Первая ступень диаметром 67 мм и длиной 110 мм имеет шпоночный паз и служит для посадки МУВП, обрабатывается с допуском n 6, шероховатостью R а = 0,8 мкм.
Вторая ступень диаметром 72 мм и длиной 85 мм имеет два участка: первый - полированный для посадки уплотнительной манжеты на участке длиной 40 мм, обработанной с допуском h 8, шероховатостью R а = 0,32 мкм; второй - для посадки подшипника обрабатывается с допуском k 6, шероховатостью R а = 0,8 мкм.
Третья ступень диаметром 80 мм и длиной 80 мм имеет шпоночный паз для посадки зубчатого колеса 8 степени точности. Обрабатывается с допуском p 6 и шероховатостью Ra = 0,8 мкм.
Четвертая ступень диаметром 85 мм и длиной 53 мм служит упором для зубчатого колеса и подшипника, специально не обрабатывается.
Пятая ступень диаметром 72 мм и длиной 32 мм служит для посадки подшипника, обрабатывается с допуском k 6, шероховатостью R а = 0,8 мкм.
На пятой ступени под подшипник протачивается канавка при помощи канавочного резца на токарном станке, т.к. торец 7 является рабочим. Все остальные торцы являются не рабочими.
Для удобства монтажа делаем фаски на ступенях: 1, 2, 3, 5., которые подрезаются на токарном станке при помощи проходного резца. Фаски не являются рабочими, поэтому точность и шероховатость обеспечивается инструментом.
На поверхностях 1 и 3 необходимо нарезать шпоночные пазы.
При изготовлении детали необходимо выдерживать допуски формы и расположения.
Допуск цилиндричности (табл. 24.2 );
Т/ o / = 0,5 . 19 = 9,5 мкм. Принимаем Т/ o / = 0,01 мм;
Для поверхности 1 (Ø67 n 6)
Т/ o / = 0,5 . 19 = 9,5 мкм. Принимаем Т/ o / =0,01 мм;
Для поверхности 3 (Ø80 p 6)
Т/ o / = 0,5 . 22 = 11 мкм. Принимаем Т/ o / =0,01 мм;
Допуск соосности расположения
Для поверхности 1 (Ø67 n 6),
Т = 60/n
Т = 60/1000 = 0,06 мм. Принимаем Т= 0,06 мм;
Для поверхностей 2 и 5 (Ø72 k 6)
Т = 0,1 . В1 . Ттабл (табл. 22.5 );
где В1 ширина подшипника;
Т = 0,1 . 32 . 4 = 12,8 мкм. Принимаем Т=0,01 мм.
Для поверхности 3 (80 p 6)
При 8 степени кинематической точности передачи для зубчатого колеса с делительным диаметром 280мм. (по табл. 22.7 ) степень точности допуска соосности 7). Т = 40мкм (табл. 22.6 ). Принимаем Т=0,04 мм.
Допуск перпендикулярности упорного буртика под подшипник
Для шарикового подшипника степень точности допуска 8 (табл. 22.4 );
Т┴ = 0,03 мм (табл. 22.8 ); Принимаем Т┴ = 0,03мм
Допуски параллельности и симметричности шпоночного паза
Зубчатого колеса 22N 9
Хвостовика 20N 9
Т// = 0,5. t шп. (табл. 24.2 );
Т// = 0,5. 52 = 26 мкм. Принимаем Т// = 0,02мм;
Т≡ = 2. t шп (по табл. 24.2 );
Т≡ = 2. 52 = 104 мкм. Принимаем Т≡ = 0,1мм,
где t шп - допуск ширины шпоночного паза.
2. Выбор вида финишной обработки конструктивных элементов детали.
Для обрезки заготовки в размер, сверления центровых отверстий и формирования профиля вала применим токарный станок 16К20.
Для поверхности 4 (85h 14) с шероховатостью Rz 80, назначаем только черновое точение.
Для поверхностей 2 и 5 (72k 6) с шероховатостью Ra 0,8 назначаем окончательное шлифование, для участка под манжетное уплотнение с Ra 0,32 назначаем полирование.
Для поверхностей 1 (67n 6) и 3 (80p 6) с шероховатостью Ra 0,8 назначаем окончательное шлифование.
Фаски, галтели, и центровые отверстия получаем на токарном станке.
Для получения шпоночных канавок используем концевые фрезы.
3. Выбор способа установки заготовки для её обработки.
Рассчитаем средний диаметр заготовки как:
Где: n число конструктивных элементов;
диаметр и длина конструктивного элемента;
L длина детали
Определим коэффициент жесткости:
Т.к. 4<К ж <10, то применяем установку в центрах.
4. Выбор вида, определение размеров заготовки, типа и типоразмера центровых отверстий.
Для условий единичного или мелкосерийного производства и при несущественном перепаде диаметров, для детали типа вал применяется в качестве заготовки круглый горячекатаный сортовой прокат.
При максимальном диаметре детали 85 мм и при К = 4,8 рекомендуемый диаметр заготовки 95 мм.
Из номенклатуры круглого сортового проката выбираем сталь горячекатаную круглую ГОСТ 2590 88 обычной степени точности (В) 95 мм с предельными отклонениями +0,5; -1,3 допуск на заготовку составляет 1,8мм (Т = 1,8мм), что соответствует 16 квалитету.
Определим длину заготовки:
где Z то припуск на торцевую обработку. При номинальном диаметре проката свыше 80 мм до 180 мм Z то = 3мм. (по табл. П7 )
Центровые отверстия для токарной и шлифовальной обработки выбираем согласно ГОСТ 14034-74. Для детали 95 мм рекомендовано центровое отверстие В 10.
Выбираем: отверстие центровое В 10 ГОСТ 14034-74.
5. Составление укрупнённого маршрута изготовления детали.
005 Заготовительная
Отрезать заготовку от проката круглого сечения обычной степени точности 95мм длиной 366мм.
010 Термическая
Заготовку подвергнуть термообработке нормализации до НВ 280.
015 Токарная
Выполнить обработку торцов в размер 360 h 14 и сверлить два центровых отверстия В10 ГОСТ 14034-74. За несколько технологических переходов выполнить обработку по формированию контура детали. Точить фаски, канавки.
020 Кругло-шлифовальная
Выполнить предварительную и окончательную обработку шеек детали.
025 Фрезерная
Фрезеровать два шпоночных паза окончательно.
030 Термическая 2
Подвергнуть ТВЧ шейку вала Ø72 h 8 под манжету.
035 Моечная
Очистить детали от загрязнений;
040 Контрольная
Выполнить контроль детали по условиям чертежа;
6. Разработка операций по формированию контура детали.
6.1. Расчёт числа стадий обработки по каждому конструктивному элементу.
Ужесточение точности:
- Ø67 n6
- Ø72 k6
- Ø72 h8
80 р 6
85 h14
Число стадий обработки:
Принимаем:
n 1 = n 2 = n 3 = n 5 = 4
n 2” = 3
n 4 = 1
6.2. Расчёт точности промежуточных размеров заготовки по стадиям обработки.
Определим точность заготовки по каждой стадии механической обработки для каждой поверхности. При расчете шаг уменьшения квалитетов по стадиям механической обработки должен изменяться по закону убывающей арифметической прогрессии. Расчет ведём в табличной форме.
Таблица 1 . Расчет точности промежуточных размеров 2-ой; 5-ой поверхностей вала: Ø72 k 6; 3-ей - Ø80р6; 1-ой Ø67 n 6.
№ |
Стадия обработки |
КВ |
∆КВ |
Заготовка |
16 |
10 |
|
Обтачивание черновое |
12 |
||
Обтачивание чистовое |
|||
Шлифование предварительное |
|||
Шлифование окончательное |
Таблица 2. Расчет точности промежуточных размеров 2”-ой поверхности на участке вала манжетное уплотнение: Ø 72 h 8
№ |
Стадия обработки |
КВ |
∆КВ |
Заготовка |
16 |
||
Обтачивание черновое |
12 |
||
Обтачивание чистовое |
|||
Шлифование окончательное |
Для получения размера 4-ой поверхности с Ø 85 h 14, используем только обтачивание черновое.
6.3. Определение промежуточных размеров по стадия механической обработки
Расчет ведем в табличной форме, используя следующие формулы:
где: - припуск на обработку поверхности принимается из;
d - текущий диаметр;
d () - диаметр предшествующей обработки;
Исходный размер ступени вала;
максимальный размер ступени вала;
Таблица 3. Расчет припусков на промежуточные размеры 2-ой и 5-ой поверхностей вала под подшипник Ø72 k 6
№ |
Характеристика размера |
|||||
Исходный размер |
2 Zi |
Предельные отклонения |
Величина |
Rz (Ra ) |
||
Шлифование окончательное |
72,021 |
0,06 |
72 |
0,8 |
||
Шлифование предварительное |
72,081 |
0,1 |
72,081 |
1,25 |
||
Обтачивание получистовое |
72,181 |
0,5 |
72,18 |
Rz 4 0 |
||
Обтачивание черновое |
72,681 |
2,1 |
72,68 |
Rz80 |
||
Заготовка |
74,781 |
- |
h 16 |
74,78 |
Rz12 5 |
Таблица 4. Расчет припусков на промежуточные размеры 3-ой
поверхности вала Ø80р6
№ |
Расчёт промежуточных размеров |
Характеристика размера |
||||
Исх. размер |
2 Zi* |
Предельные отклонения |
Величина |
Rz (Ra ) |
||
Шлифование окончательное |
80,059 |
0,06 |
p6 |
80 |
0, 8 |
|
Шлифование предварительное |
80,119 |
0,1 |
h7 |
80,119 |
1,25 |
|
Точение получистовое |
80,219 |
0,5 |
h9 |
80,22 |
Rz40 |
|
Точение черновое |
80,719 |
2,1 |
h 12 |
80,72 |
Rz80 |
|
Заготовка |
82,819 |
- |
h16 |
82,82 |
Rz12 5 |
Таблица 5. Расчет припусков на промежуточные размеры 2”-ой ступени вала на участке под уплотнение Ø72 h 8
№ |
Расчёт промежуточных размеров |
Характеристика размера |
||||
Исх. размер |
2 Zi* |
Предельные отклонения |
Величина |
Rz (Ra ) |
||
Шлифование окончательное |
7 2 |
0,06 |
7 2 |
0,8 |
||
Точение получистовое |
72,06 |
0,5 |
72,06 |
Rz 40 |
||
Точение черновое |
7 2,56 |
2,1 |
h1 2 |
7 2,56 |
Rz 80 |
|
Заготовка |
74,66 |
- |
h16 |
74,66 |
Rz 125 |
Таблица 6. Расчет припусков на промежуточные размеры 1-ой
поверхности вала Ø67 n 6
№ |
Расчёт промежуточных размеров |
Характеристика размера |
||||
Исх. размер |
2 Zi* |
Предельные отклонения |
Величина |
Rz (Ra ) |
||
Шлифование окончательное |
67,039 |
0,06 |
n 6 |
67 |
0, 8 |
|
Шлифование предварительное |
67,099 |
0,1 |
h 7 |
67,099 |
1,25 |
|
Точение получистовое |
67,199 |
0,5 |
h9 |
67,2 |
Rz40 |
|
Точение черновое |
67,699 |
2,1 |
h12 |
67,7 |
Rz80 |
|
Заготовка |
69,799 |
- |
h16 |
69,8 |
Rz12 5 |
Таблица 7. Расчет припусков на промежуточные размер 3-ей ступени
вала Ø85 h 14
№ |
Расчёт промежуточных размеров |
Характеристика размера |
||||
Исх. размер |
2 Zi* |
Предельные отклонения |
Величина |
Rz (Ra ) |
||
Точение черновое |
85 |
1,7 |
h1 4 |
85 |
Rz80 |
|
Заготовка |
86,7 |
- |
h16 |
86,7 |
Rz125 |
Проверка:
Окончательно выбираем из сортамента прокат 90мм
7. Составление плана токарной и шлифовальной обработок детали
Расчёт выполняем из условия применения станка 16К20, имеющего следующие характеристики:
Допустимая мощность резания N = 7,5 кВт;
Максимальный диаметр заготовки до 400 мм;
Максимальная длина заготовки 1400 мм;
Частота вращения шпинделя 12,5…1600 об/мин (регулирование ступенчатое);
Продольная подача суппорта 0,05…2,8 мм/об (регулирование ступенчатое).
7.1. Расчет предельно-допустимых глубин резания при черновом обтачивании.
Глубину резания для технологического перехода рассчитываем по формуле:
и сравниваем полученное значение с предельно допустимым для данного диаметра:
если обработка осуществляется за один переход,
если обработка осуществляется за несколько технологических переходов.
Применим формулу с коэффициентом «0,1», т.к. Кж = 4,8<9.
При этом назначаем подачу инструмента и сравниваем мощность резания с допустимой мощностью на шпинделе (7,5 кВт).
Установ В
Третья ступень: 80 р6
Выполняем анализ по мощности:
При подаче инструмента S = 0,3 мм/об и глубине резания t = 5 мм мощность N = 7,2 кВт, что меньше 7,5кВт. (по табл. П13 ).
Вторая ступень: Ø72 k 6
Следовательно, обработка по диаметрам возможна за 1 проход.
Выполняем анализ по мощности:
При подаче инструмента S = 0,4 мм/об и глубине резания t = 4 мм мощность N
Первая ступень: Ø67 n 6
Следовательно, обработка по диаметрам возможна за 1 проход.
Выполняем анализ по мощности:
При подаче инструмента S t = 3 мм мощность N = 7,1 кВт, что меньше 7,5кВт. (по табл. П13 ).
Установ Г
Четвёртая ступень: 85 h 14
Следовательно, обработка по диаметрам возможна за 1 проход.
Выполняем анализ по мощности:
При подаче инструмента S = 0,6 мм/об и глубине резания t = 3 мм мощность N = 7,1 кВт, что меньше 7,5кВт. (по табл. П13 ).
Пятая ступень: Ø72 k 6
Следовательно, обработка по диаметрам возможна за 1 проход.
Выполняем анализ по мощности:
При подаче инструмента S = 0,2 мм/об и глубине резания t = 8 мм мощность N = 7,4 кВт, что меньше 7,5кВт. (по табл. П13 ).
7.2. План токарной обработки
Операция 015. Токарная.
Установ А (торцевание, центрование заготовки)
2.Подрезать торец "как чисто".
Установ Б (торцевание, центрование заготовки)
1. Переустановить заготовку.
2.Подрезать торец справа с соблюдением размера 1.
3.Сверлить центровое отверстие по условиям эскиза.
1. Переустановить заготовку
2. Точить начерно в размер 1 на длине 6.
3. Точить начерно в размер 2 на длине 5.
4. Точить начерно в размер 3 на длине 4.
1. Переустановить заготовку.
2. Точить начерно в размер 1 на проход.
3. Точить начерно в размер 2 на длине 3.
Получистовое обтачивание:
4. Точить получисто в размер 4 на длине 6.
5. Точить канавку по размерам 7,8,9.
6. Снять фаску 5.
Установ Д (получистовая обтачивание).
1. Переустановить заготовку.
2. Точить получисто в размер 3, на длину 8, с образованием галтели 7.
3. Точить получисто в размер 2, обеспечивая размер 9, с образованием галтели 6.
4. Точить получисто в размер 1, обеспечивая размер 10, с образованием галтели 5.
5. Снять фаску 4.
7.3. План шлифовальной обработки
Операция 020 шлифовальная
Установ А (шлифование предварительное, окончательное)
1. Установить, закрепить, снять заготовку.
2. Шлифовать предварительно в размер 1 на длине 3.
3. Шлифовать окончательно в размер 2 на длине 3.
Установ Б (шлифование предварительное, окончательное)
1. Переустановить заготовку.
2. Шлифовать предварительно в размер 6 на длине 8.
3. Шлифовать предварительно в размер 4 на длине 9.
4. Шлифовать предварительно в размер 2 на длине 10.
5. Шлифовать окончательно в размер 7 на длине 8.
6. Шлифовать окончательно в размер 5 на длине 9.
7. Шлифовать окончательно в размер 3 на длине 10.
8. Шлифовать окончательно в размер 1 на длине 11.
8. Выбор и расчёт режимов резания.
8.1. Черновое обтачивание.
При черновом обтачивании применяем проходной резец с главным углом в плане φ = 450 , стойкостью Т = 60 мин из материала Т15К6.
Для установа В:
Третья ступень 80,72 : :глубина резания t = 4,64 мм, продольная подача S = 0,3 мм/об табл.11.
Коэффициент корректировки.
КПV = 0,9 табл. 5;
КИV = 1 табл. 6;
КφV = 1 табл. 18.
Скорость резания:
Определяем частоту вращения:
Вторая ступень 72,68 : глубина резания t = 4,02мм, продольная подача S = 0,4 мм/об табл.11.
Коэффициент корректировки.
где КМV = 1,25 табл. 1; 2.
КПV = 1 табл. 5;
КИV = 1 табл. 6;
КφV = 1 табл. 18.
Скорость резания:
Определяем частоту вращения:
Первая ступень 67,7 : глубина резания t = 2,49 мм, продольная подача S = 0,6мм/об табл.11.
Коэффициент корректировки.
где КМV = 1,25 табл. 1; 2.
КПV = 1 табл. 5;
КИV = 1 табл. 6;
КφV = 1 табл. 18.
Скорость резания:
коэффициенты СV = 350, x = 0,15, y = 0,35, m = 0,2 табл.17.
Определяем частоту вращения:
Из нормального ряда частот вращения шпинделя станка принимаем ближайшее меньшее значение n = 860 об/мин.
Для установа Г :
Четвёртая ступень 85 : глубина резания t = 2,5мм, продольная подача S = 0,6 мм/об табл.11.
Коэффициент корректировки.
где КMV коэффициент учёта влияния материала заготовки на скорость резания;
КП V коэффициент учёта влияния состояния поверхности на скорость резания;
КИV коэффициент учёта влияния инструментального материала на скорость резания;
КφV коэффициент учёта влияния главного угла в плане резца на скорость резания;
где коэффициенты КГ = 1 и n V = 1 табл. 2.
δв = 600 МПа для стали 45 ГОСТ 1050-88;
КПV = 0,9 для первого прохода табл. 5;
КИV = 1 для материала Т15К6 табл. 6;
КφV = 1 для резца с главным углом в плане 450 табл. 18.
Скорость резания:
где коэффициенты СV = 350, x = 0,15, y = 0,35, m = 0,2 табл.17.
Определяем частоту вращения:
Из нормального ряда частот вращения шпинделя станка принимаем ближайшее меньшее значение n = 630 об/мин.
Пятая ступень 72,68 : глубина резания t = 6,16 мм, продольная подача S = 0,2 мм/об табл.11.
Коэффициент корректировки.
где КМV = 1,25 табл. 1; 2.
КПV = 1 табл. 5;
КИV = 1 табл. 6;
КφV = 1 табл. 18.
Скорость резания:
коэффициенты СV = 420, x = 0,15, y = 0,2, m = 0,2 табл.17.
Определяем частоту вращения:
8.2. Получистовое обтачивание.
При получистовом обтачивании применяем проходной резец с главным углом в плане φ = 900 , радиусом при вершине r = 2,4 мм табл.14, стойкостью Т = 60 мин из материала Т15К6.
Для установа Г:
Пятая ступень 72,18 глубина резания t = Zi = 0,25мм.
где К3 = 0,45 табл.14
Коэффициент корректировки.
где КМV = 1,25 табл. 1; 2.
КПV = 1 табл. 5;
КИV = 1 табл. 6;
КφV = 0,7 табл. 18.
Скорость резания:
коэффициенты СV = 350, x = 0,15, y = 0,35, m = 0,2 табл.17.
Определяем частоту вращения:
Из нормального ряда частот вращения шпинделя станка принимаем ближайшее меньшее значение n = 1000 об/мин.
Для установа Д:
Первая ступень 67,2 : глубина резания t = Zi = 0,25мм.
Продольная подача определяется по табл.14 в зависимости от шероховатости и радиусе при вершине резца. SТАБЛ = 0,87 при Rz = 40.
где К3 = 0,45 коэффициент запаса для обрабатываемого материала из стали 45 с пределом прочности σВ = 600 МПа табл.14.
Из нормального ряда продольных подач суппорта станка принимаем значение S = 0,4 мм/об.
Коэффициент корректировки.
где КМV = 1,25 табл. 1; 2.
КПV = 1 табл. 5;
КИV = 1 табл. 6;
КφV = 0,7 табл. 18.
Скорость резания:
коэффициенты СV = 350, x = 0,15, y = 0,35, m = 0,2 табл.17.
Определяем частоту вращения:
Из нормального ряда частот вращения шпинделя станка принимаем ближайшее меньшее значение n = 1000 об/мин.
Вторая ступень 72,18 глубина резания t = Zi = 0,25мм.
SТАБЛ = 0,87 при Rz = 40. табл.14
где К3 = 0,45 табл.14
Из нормального ряда продольных подач суппорта станка принимаем значение S = 0,4 мм/об.
Коэффициент корректировки.
где КМV = 1,25 табл. 1; 2.
КПV = 1 табл. 5;
КИV = 1 табл. 6;
КφV = 0,7 табл. 18.
Скорость резания:
коэффициенты СV = 350, x = 0,15, y = 0,35, m = 0,2 табл.17.
Определяем частоту вращения:
Из нормального ряда частот вращения шпинделя станка принимаем ближайшее меньшее значение n = 1000 об/мин.
Третья ступень 80,22 глубина резания t = Zi = 0,25мм.
SТАБЛ = 0,87 при Rz = 40. табл.14
где К3 = 0,45 табл.14
Из нормального ряда продольных подач суппорта станка принимаем значение S = 0,4 мм/об.
Коэффициент корректировки.
где КМV = 1,25 табл. 1; 2.
КПV = 1 табл. 5;
КИV = 1 табл. 6;
КφV = 0,7 табл. 18.
Скорость резания:
коэффициенты СV = 350, x = 0,15, y = 0,35, m = 0,2 табл.17.
Определяем частоту вращения:
Из нормального ряда частот вращения шпинделя станка принимаем ближайшее меньшее значение n = 860 об/мин.
8.3. Расчёт режимов шлифования.
Шлифование выполняем на шлифовальном станке 3Б151, который имеет следующие характеристики:
- наибольший диаметр и длина шлифуемой заготовки: 180 х 630(800) мм;
- диаметр и ширина шлифовального круга: 600 х 63 мм;
- частота вращения детали: 63…400 об/мин (бесступенчатое регулирование);
- скорость продольного перемещения рабочего стола: 0,1…0,6 м/мин (бесступенчатое регулирование);
- поперечная подача шлифовального круга (глубина шлифования): 0,0025…0,05 мм на один ход рабочего стола с шагом 0,0025 мм;
- непрерывная подача шлифовального круга при врезном шлифовании: 0,1…2 мм/мин;
- мощность электродвигателя привода шлифовального круга: 7 кВт.
8.3.1. Расчёт режимов предварительного шлифования.
Согласно с. 302 для предварительного шлифования принимаем:
- v ШЛ.КР. = 30 м/с;
- скорость вращения заготовки: v ЗАГ. = 20 м/мин;
- S = (0,3…0,7)·В ШЛ.КР. = 18,9…44,1 мм/об. Принимаем S = 30 мм/об;
- глубина шлифования t ШЛИФ = 0,01 мм;
72,081 :
Частота вращения заготовки:
80,119 :
Частота вращения заготовки:
67,099 :
Частота вращения заготовки:
8.3.2. Расчёт режимов окончательного шлифования.
Согласно с. 302 для окончательного шлифования принимаем:
- скорость вращения шлифовального круга: v ШЛ.КР. = 35 м/с;
- скорость вращения заготовки: v ЗАГ. = 35 м/мин;
- продольная подача шлифовального круга: S =(0,2…0,4)·В ШЛ.КР. =12,6…25,6 м/об. Принимаем S = 20 мм/об;
- глубина шлифования t ШЛИФ = 0,005 мм;
- количество проходов шлифовального круга:
- для 2” ступени количество проходов шлифовального круга:
Частота вращения шлифовального круга:
72,021 :
Частота вращения заготовки:
80,059
Частота вращения заготовки:
67,039
Частота вращения заготовки:
72:
Частота вращения заготовки:
9. Определение затрат времени на токарную и шлифовальную обработку
Расчёт времени выполняем для каждого технологического перехода в соответствии с картой эскизов.
9.1. Определение затрат времени на токарную обработку
(9.1)
Где Т Ш.Т. затраты времени непосредственно на обработку детали;
Т П.З. подготовительно-заключительное время, Т П.З. = 12 мин. ;
N число деталей в партии. N = 1;
(9.2)
где К Д коэффициент учёта дополнительных затрат времени, для токарной обработки К Д = 0,07 ;
t ОП. оперативное время;
(9.3)
где - затраты времени на установку, закрепление и снятие заготовки, = 0,76 мин ;
Вспомогательное время, связанное с конкретным технологическим переходом, для чернового обтачивания = 0,25 мин, для получистового обтачивания = 0,4 мин, ;
Затраты времени в данном технологическом переходе на перемещение инструмента, при котором происходит обработка поверхности;
где - длина перемещения инструмента по обрабатываемой поверхности на данном технологическом переходе;
Частота вращения детали на данном технологическом переходе;
Продольная подача резца на данном технологическом переходе;
Установ В (черновое обтачивание).
80,72
72,68 :
67,7 :
Тогда:
Установ Г (черновое обтачивание).
85 :
72,68 :
Тогда:
Установ Г (получистовое обтачивание).
72,18:
Тогда:
Установ Д (получистовое обтачивание).
67,2:
72,18 :
80,22:
Тогда:
Итого затраты времени на токарную обработку заготовки:
Штучно-калькуляционное время:
9.2. Определение затрат времени на шлифовальную обработку
Затраты времени на шлифовальную обработку рассчитываем по формулам (9.1), (9.2), (9.3) :
Для шлифовальной обработки К Д = 0,09 ;
Для предварительного шлифования = 0,25 мин., I = 5 и S = 30 мм/об, для окончательного шлифования = 0,45 мин., I = 6 (для 2” ступени I =2), и S = 20 мм/об .
Определение затрат времени на предварительное шлифование.
72,081:
72,081:
80,119 :
67,099 :
Тогда:
Определение затрат времени на окончательное шлифование.
72,021:
72,021:
80,059:
67,039 :
7 2 :
Тогда:
Итого затраты времени на шлифовальную обработку заготовки:
Штучно-калькуляционное время:
10. Заключение
В ходе курсовой работы был разработан технологический процесс на изготовление детали ступенчатый вал. Оформлена технологическая документация на операции и переходы применяемые в ходе получения детали. Установлены и применены в ходе разработки техпроцесса основные принципы и приёмы, используемые при обработке металлов резанием.
Список литературы
1. Воробьёв Л.Н.Технология машиностроения и ремонт машин-
М.: «Высшая школа», 1983
2. Справочник технолога-машиностроителя: 3-е издание в 2-х т. под ред. Косиловой А.Г., Мещерякова Р.К., -М. “Машиностроение” 1972.
3. Справочник технолога-машиностроителя: 4-е издание в 2-х т. под ред. Косиловой А.Г., Мещерякова Р.К., -М. “Машиностроение” 1985.
4. Краткий справочник металлиста, 3-е издание под ред. Орлова П.Н., Скороходова Е.А., -М.: «Машиностроение», 1987.
5. Панов А.А. Обработка металлов резанием. Справочник технолога, -М.: «Машиностроение», 1988.
6. Дальский А.М. Справочник технолога-машиностроителя: в 2-х т., -М.: «Машиностроение», 2004.
7. Технология машиностроения: в 2-х т., т. 1. Основы технологии машиностроения / Бурцев В.М., Васильев А.С., Дальский А.М. и др. М.: МГТУ им. Н.Э. Баумана 1999.
8. Конструирование узлов и деталей машин, под ред. Дунаева П.Ф., Леликова О.П., М.: Издательский центр “Академия”, 2003.
10. Проектирование технологических процессов изготовления деталей подъёмно-транспортных, строительных и дорожных машин. 2-я часть В.И. Фомин М: «МИИТ» 2008.
Cтраница 2
Ступенчатые валы являются наиболее распространенной деталью в машиностроении. Автоматизации их производства уделяется большое внимание. Токарная обработка ступенчатых валов обычно выделяется.
Ступенчатые валы диаметром 48 мм и длиной 258 мм обраба тываются с тактом в 1 9 мин (114 сек); из этого времени вспомогательное время на станках составляет около 32 сек, а продолжительность перегрузки - около 12 сек.
Ступенчатые валы можно делить на короткие - до 250 мм, средние - 250 - 350 мм и длинные - более 350 мм.
Полирование кулачков.| Контроль профиля кулачков вые профиль и углы расположения, то плечо Н при синхронном вращении обоих валов не изменяется. Если какой-либо кулачок контролируемого вала имеет погрешности формы или расположения, то плечо Н изменится и стрелка индикатора отклонится. |
Ступенчатые валы в основном изготовляют из конструкционных и легированных сталей, так как к ним предъявляются высокие требования по механической прочности, обрабатываемости, малой чувствительности к концентрации внутренних напряжений.
Ступенчатые валы имеют несколько конструктивных разновидностей. К ним относятся: 1) валы без шлицев и зубчатых колес; 2) валы со шлицами; 3) валы-шестерни без шлицев; 4) валы-шестерни цилиндрические со шлицами; 5) валы-шестерни конические со шлицами.
Ступенчатые валы с небольшим перепадом ступеней могут непосредственно обрабатываться шлифованием на бесцентрово-шлифовальных станках по ступени наибольшего диаметра, а остальные ступени - с напуском, удаляемым при последующих переходах.
Ступенчатые валы обрабатываются обычно из штампованных, а в некоторых случаях из литых заготовок.
Ступенчатые валы являются наиболее распространенными. Для уменьшения массы или для размещения внутри других деталей валы иногда делают с каналом по оси; в отличие от сплошных такие валы называют полыми.
Ступенчатый вал с диаметром D 75 мм и d QO мм (см. рисунок), изготовленный из углеродистой стали, для которой ав 75 KZJMMS, о.
Ступенчатый вал с постепенным утолщением от опор к его центру имеет заметно повышенные критические числа оборотов по сравнению с аналогичным валом усредненной толщины.
Ступенчатый вал обрабатывается с помощью эталонного вала, установленного на центрах параллельно обрабатываемому валу. Особенность этой схемы заключается в том, что копир представляет собой простой оригинал обрабатываемого вала, который можно быстро менять; станок не нуждается в настройке.
Если ступенчатый вал изготовляют из проката, то при точении ступеней с меньшим диаметром возможны недопустимо большие глубины резания. В этом случае применяют метод деления припуска. При этом варианте продольный суппорт перемещается на всю длину / обтачиваемых ступеней.
Вычертить ступенчатый вал, выдерживая только масштаб диаметров, а также привести все данные к заданию.
Обработка ступенчатых валов
К атегория:
Токарное дело
Обработка ступенчатых валов
Валы, имеющие несколько участков различного диаметра и длины, называются ступенчатыми. Для обработки ступенчатых валов резец настраивают с помощью пробных проходов, отдельно для каждой ступени. Деления лимба, соответствующие диаметрам каждой ступени, запоминают или записывают. По этим данным ведут обработку всей, партии заготовок без пробных проходов.
Длины ступеней контролируют штангенциркулем с выдвижным глубиномером (типа ШЦТ ), штангенглубиномером, линейкой или шаблоном. Токарные станки 16К20, 1К62, 1К625, 1И611 и другие имеют лимб продольной подачи. Повороту лимба на одно деление соответствует перемещение суппорта на один миллиметр. По лимбу продольной подачи можно контролировать продольное перемещение резца и отводить резец в тот момент, когда получена нужная длина ступени. Высокая производительность при обработке ступенчатых валов достигается за счет правильного выбора схемы обработки. Наиболее производительной является такая схема обтачивания, при которой весь припуск снимают за один проход резца. Общий путь перемещения резца при этом равен сумме длин ступеней, т. е. общей длине заготовки.
Работа по второй схеме менее производительна, чем по первой.
Большую партию ступенчатых заготовок целесообразно обрабатывать, пользуясь продольным упором, закрепляемым на направляющей станины и ограничивающим перемещение суппорта. Проточив первую пробную заготовку на нужную длину, выключают станок и, не отводя суппорта, закрепляют упор так, чтобы он прикоснулся к левой боковой грани каретки суппорта. Теперь все последующие заготовки, обрабатываемые при перемещении суппорта до упора, будут иметь одинаковый размер. Механическую подачу выключают при подходе суппорта к упору на расстоянии 1 - 2 мм и доводят его до упора ручной подачей.
1. КОНТРОЛЬ ДЛИН СТУПЕНЕЙ СТУПЕН -ЧАТОГО ВАЛИКА : а - штангенциркулем ШЦ-I. б - штангенглубиномером, в - линейкой, г - шаблоном
2. СХЕМЫ ОБТАЧИВАНИЯ СТУПЕНЧАТОГО ВАЛИКА :
Заготовки с несколькими ступенями обрабатывают по упору с мерными длиноограничите-лями, в качестве которых можно использовать наборы мерных плиток (обычно потерявших исходную точность) или специальные шаблоны.
Центровые отверстия в заготовках не могут иметь абсолютно одинаковую глубину, поэтому при установке в центрах заготовки смещаются, заготовки с более глубоким центровым отверстием устанавливаются ближе к передней бабке, а с более мелким - дальше. При обработке по упору вследствие различной глубины отверстий получаются различные длины ступеней на различных деталях партии. Чтобы обеспечить одинаковые длины ступеней для всех деталей партии ступенчатых валов, закрепляемых в центрах, применяют передний плавающий центр. Он состоит из конического корпуса, который устанавливается в конической расточке шпинделя; собственно центра, свободно перемещающегося в осевом отверстии корпуса; пружины и упорного винта. Винт играет роль шпонки, а винт - роль стопора.
Когда обрабатывается партия коротких заготовок в патроне по продольным упорам, то для предотвращения ее продольного смещения заготовка должна упираться в уступы кулачков патронов или в торец внутреннего (шпиндельного) упора. Рабочий торец винта внутреннего упора подрезают непосредственно на станке при затянутой контргайке: это обеспечивает его перпендикулярность к оси шпинделя.
3. НЕПОДВИЖНЫЙ ПРОДОЛЬНЫЙ УПОР К ТОКАРНОМУ СТАНКУ 16К20: 1 - корпус упора, 2 - прижимная планка, 3 - зажимной винт, 4 - регулировочный винт
4. ОБТАЧИВАНИЕ СТУПЕНЧАТОГО ВАЛА ПО УПОРУ С ДЛИНООГРАНИЧИТЕЛЯМИ (а), СХЕМА ОБОЗНАЧЕНИЯ (б): 1 -упор, 2 -регулировочный винт, 3 - мерные плитки - длиноограничители
5. ВНУТРЕННИЙ УПОР : 1 - шпиндель, 2 - конусная втулка, 3 - винт упора, 4 - контргайка, 5 - патрон
Постоянство диаметров ступенчатых валов партии достигается при помощи поперечных упоров: неподвижный поперечный упор закрепляют на каретке суппорта, а подвижный - на поперечных салазках.
Если брак исправим, т. е. на поверхности заготовки осталась часть металла припуска, то после соответствующей регулировки повторяют чистовой проход. При обработке партии заготовок после обработки пробной детали ее контролируют, устанавливают и устраняют причины брака, затем приступают к обработке всей партии.
6. ПЛАВАЮЩИЙ ЦЕНТР : а -устройство, б - применение (базирование на левый торец заготовки при помощи плавающего центра), в - схема обозначения; 1-упорный винт, 2 -пружина, 3 - корпус, 4 - винт-стопор, 5 - центр, 6 - винт-шпонка
7. ИСПОЛЬЗОВАНИЕ КУЛАЧКОВ В КА-1 ЧЕСТВЕ УПОРОВ : а -упор в кулачок, б - упор в уступ кулачка, в -упор в выточку (для «сырых» кулачков). г - схема обозначения
8. ПОПЕРЕЧНЫЕ УПОРЫ СТАНКА 16К20: 1 - неподвижный на каретке, 2 - на поперечных салазках суппорта
9. ОБРАБОТКА СТУПЕНЧАТОГО ВАЛИКА ПО ПОПЕРЕЧНОМУ УПОРУ С МЕРНЫМИ ОГРАНИЧИТЕЛЯМИ ДИАМЕТРА