Как вырастить кристалл из медного купороса в домашних условиях. Выращивание и изучение условия образования кристаллов медного купороса
В позапрошлом номере мы уже рассказывали, как быстро вырастить кристаллы медного купороса . Для этого нужно растворить медный купорос в горячей воде, охладить раствор, опустить в него нитку с затравкой (или просто нитку) и подождать несколько часов. На нитке вырастут кристаллы медного купороса размером до сантиметра, которые будут образовывать большие сростки, словно мидии.
Если вы хотите вырастить большой кристалл, придется поступить совсем по-другому. Сначала нужно приготовить насыщенный раствор соли, в нашем случае - медного купороса. Насыщенным называется раствор, который находится в равновесии с нерастворенным веществом (твердым, жидким или газообразным). Следовательно, насыщенный раствор содержит максимальное количество вещества, которое может раствориться при данной температуре. Чтобы приготовить насыщенный раствор медного купороса, сначала рассчитаем, сколько нужно взять соли.
Растворимость медного купороса при 20°С составляет 35.6 г в 100 г воды. Например, если вы взяли 200 мл воды, значит необходимо 35.6·200/100= 71.2 г CuSO 4 · 5H 2 O. А как быть при других температурах? С ростом температуры растворимость сульфата меди сначала увеличивается, потом почти перестает зависеть от температуры . Поэтому, чтобы исключить влияние колебаний температуры в лаборатории, точности взвешивания и других факторов возьмите количество медного купороса, раза в полтора большее расчетного. Например, в нашем случае это 71.2·1.5 ≈ 107 г. Залейте соль водой и оставьте примерно на сутки, время от времени перемешивая. Когда растворение медного купороса прекратится, и наступит равновесие, профильтруйте раствор через неплотную фильтровальную бумагу или вату. Избыток соли останется на фильтре - его можно снова высушить и использовать повторно. Налейте полученный раствор в стакан или банку. Теперь выберите крупный и хорошо сформированный кристаллик и привяжите его к нитке. Кристаллик послужит затравкой. Привяжите второй конец нитки к карандашу или стеклянной палочке и опустите затравку в раствор. Накройте стакан марлей - для защиты от пыли. Все, что остается - ждать. Через несколько дней рост кристалла будет виден визуально, за неделю может вырасти кристалл длинной в 1 см, за три-пять недель - 5 см. Если в стакане образуется осадок мелких кристалликов - перелейте раствор в чистый стакан и перенесите в него кристалл. В ходе нашего эксперимента такую процедуру пришлось проделать несколько раз. Со временем на нитке тоже образуются мелкие кристаллики, которые начинают расти. Избежать этого сложно, можно разве что поднять кристалл повыше, чтобы меньший отрезок нитки контактировал с раствором. Во время эксперимента возникла идея использовать вместо хлопчатобумажной нитки тонкую медную проволочку или капроновую нить, однако на них затравка росла значительно хуже. Эксперимент длится от нескольких недель до одного-двух месяцев.
К сожалению, на воздухе кристаллы медного купороса теряют часть своей воды, при этом происходит их выветривание (разрушение). Чтобы кристаллы медного купороса сохранились дольше, поместите их в плотно закрытую банку и храните в прохладном помещении.
Если в начальной стадии эксперимента у вас растворилась затравка, значит, раствор не был насыщенным. Причин может быть несколько. Во-первых, исходный раствор мог недостаточно долго контактировать с кристаллами и не успел стать насыщенным. Во-вторых, растворимость медного купороса растет с температурой. Если вы приготовите насыщенный раствор и опустите в него кристаллик, а потом в комнате потеплеет, растворимость возрастет, и затравка может раствориться. В любом случае, добавьте в раствор еще несколько ложек купороса, перемешайте его, и дайте постоять (а потом снова профильтруйте).
Выращивание кристаллов требует труда и много терпения, но результат может очень приятно вас удивить.
__________________________________________________
Медная, латунная и бронзовая стружка может быть переработана пирометаллургически и гидрометаллургически. В первом случае это переплавка, во втором - химическая переработка.
Сложность первого метода состоит в том, что при переплавке часть меди и еще большая часть цинка выжигаются, что приводит как к экономическим безвозвратным потерям, так и к экологическому ущербу и ухудшению условий труда. В таблице 1 приведены наиболее высокие закупочные цены на стружку, которая перерабатывается именно по первой технологии (открытые материалы из интернета).
Наименование | Цена до 100 кг | Цена 100-500 кг | Цена 500-1000 кг | Цена свыше 1000 кг |
Латунная стружка |
Представляет интерес второй способ, который не требует столь больших капитальных вложений. Однако главная сложность метода заключается в том, что необходимо разделять двух-трех компонентные сплавы, обладающие сами по себе низкой реакционной способностью. Разделение можно провести двумя путями - химическим и электрохимическим. В первом случае мы используем только химические реакции и можем воздействовать на систему (ускорять реакцию):
Изменением температуры
Введением окислителя
Введением катализаторов
Во втором случае мы можем использовать анодную поляризацию сплава для ускорения растворения, в совокупности с поисанными выше способами.
В обеих методиках приходится столкнуться с тем, что физико-химические закономерности процессов не до конца исследованы, а описанные в литературе механизмы реакций оказываются гораздо сложнее.
Выбор растворителя (выщелачевателя) является первоочередной задачей. Для этого необходимо знать химические свойства компонентов, содержащихся в перерабатываемых сплавах.
1.1 Общая информация по меди, ее сплавам и соединениям
Плотность меди - 8,93*103кг/м 3 , удельная теплоемкость при 20 o C - 0,094 кал/град, температура плавления - 1083 o C, удельная теплота плавления - 42 кал/г, температура кипения - 2600 o C, коэффициент линейного расширения (при температуре около 20 o C) - 16,7 *106(1/град), коэффициент теплопроводности меди - 335ккал/м*час*град, удельное сопротивление при 20 o C - 0,0167 Ом*мм 2 /м.
Качество катодной меди регламентируется ГОСТ 546 «Катоды медные». По химическому составу катодная медь классифицируется по ГОСТ 859. Содержание меди после электролитического рафинирования из сульфатного электролита должно составляет 99,99%.
Сплавы, повышающие прочность и другие свойства меди, получают введением в нее добавок, таких, как цинк, олово, кремний, свинец, алюминий, марганец, никель. На сплавы идет более 30% меди. Латуни - сплавы меди с цинком (меди от 60 до 90% и цинка от 40 до 10%) - прочнее меди и менее подвержены окислению. При присадке к латуни кремния и свинца повышаются ее антифрикционные качества, при присадке олова, алюминия, марганца и никеля возрастает антикоррозийная стойкость.
Раньше бронзами называли сплавы меди (80-94%) и олова (20-6%). В настоящее время производят безоловянные бронзы, именуемые по главному вслед за медью компоненту.
Медный купорос или серно-медная соль CuSO 4 .5H 2 O - встречается в природе как вторичное образование, в виде кристаллов и натечных масс, или в виде раствора, в так называемых цементных водах.
Состав медного купороса регламентируется двумя документами - ГОСТ 19347-99 и ТУ 2141-368-100-97. Состав по ГОСТ приведен в таблице 1. Текст ГОСТа вынесен в приложение 1.
Таблица 1 - Химический состав товарного медного купороса согласно ГОСТ 19347-99 (в %)
Норма для марки |
|||||
Высший сорт | Первый сорт | Высший сорт | Первый сорт | Второй сорт |
|
CuSO 4 * 5H 2 O, не менее, в пересчете на Cu | 99,1 25,22 | 24,94 | 98,1 24,97 | 24,43 | 93,1 23,96 |
Железо (Fe) не более | 0,02 | 0,04 | 0,04 | 0,05 | 0,10 |
Свободная серная кислота, не более | 0,20 | 0,25 | 0,20 | 0,25 | 0,25 |
Нерастворимый в воде осадок | 0,03 | 0,05 | 0,05 | 0,05 | 0,10 |
Мышьяк, не более | 0,002 | 0,012 | 0,012 | 0,012 | 0,028 |
Примечания 1. Для сельского хозяйства и в розничную торговлю поставляется медный купорос марок А и Б высшего и первого сорта 2. В медном купоросе марки А высшего сорта, предназначенном для экспорта, массовая доля кальция должна быть не более 0,006%, массовая доля магния - не более 0,005%. |
Медный купорос применяется в сельском хозяйстве в качестве фунгицида, в промышленности в производстве искусственных волокон, красителей, минеральных красок, мышьяковистых химикатов, для обогащения руды при флотации.
Химические свойства меди детально рассмотрены в главе 2. Свойства легирующих элементов кратко приведены ниже.
1.2 Краткие химические свойства цинка
Нормальный окислительно-восстановительный потенциал цинка равен -0,76 В. На воздухе при температуре до 100°С цинк быстро тускнеет, покрываясь поверхностной пленкой основных карбонатов. Во влажном воздухе, особенно в присутствии СО 2 , происходит разрушение металла даже при обычных температурах. Сульфид цинк выпадает в осадок при действии сероводорода на слабокислые или аммиачные водные растворы солей Zn. Сильные минеральные кислоты энергично растворяют цинк, особенно при нагревании, с образованием соответствующих солей. При взаимодействии с разбавленной НCl и H 2 SO 4 выделяется Н 2 , а с НNО 3 - кроме того, NO, NO 2 , NH 3 . С концентрированной НCl, H 2 SO 4 и HNO 3 цинк реагирует, выделяя соответственно Н 2 , SO 2 , NO и NO 2 . Растворы щелочей окисляют цинк с выделением Н 2 и образованием растворимых в воде цинкатов. Интенсивность действия кислот и щелочей на цинк зависит от наличия в нем примесей. Чистый цинк менее реакционноспособен по отношению к этим реагентам из-за высокого перенапряжения на нем водорода. В воде соли цинка при нагревании гидролизуются, выделяя белый осадок гидрооксида Zn(OH) 2 . Известны комплексные соединения, содержащие Цинк, например SО 4 и другие.
1.3 Краткие химические свойства свинца
Нормальные электродные потенциалы свинца соответственно равны -0,126 В для Рb/Рb 2+ и +0,65 В для Pb/Pb 4+ . Однако свинец не вытесняет водород из разбавленной соляной и серной кислот, вследствие перенапряжения Н 2 на Pb, а также образования на поверхности металла защитных пленок трудно-растворимых хлорида РbCl 2 и сульфата PbSO 4 . Концентрированные H 2 SO 4 и НCl при нагревании действуют на Pb, причем получаются растворимые комплексные соединения состава Pb(HSO 4) 2 и Н 2 [РbCl 4 ]. Азотная, уксусная, а также некоторые органических кислоты (например, лимонная) растворяют свинец с образованием солей Рb (II). По растворимости в воде соли делятся на растворимые (ацетат, нитрат и хлорат свинца), малорастворимые (хлорид и фторид) и нерастворимые (сульфат, карбонат, хромат, фосфат, молибдат и сульфид). Соли Pb (IV) могут быть получены электролизом сильно подкисленных H 2 SO 4 растворов солей Рb (II); важнейшие из солей Pb (IV) - сульфат Pb(SO 4) 2 и ацетат Рb(С 2 Н 3 О 2) 4 . Соли Pb (IV) склонны присоединять избыточные отрицательные ионы с образованием комплексных анионов, например, плюмбатов (РbО 3) 2- и (РbО 4) 4- , хлороплюмбатов (РbCl 6) 2- , гидроксоплюмбатов [Рb(ОН) 6 ] 2- и других. Концентрированные растворы едких щелочей при нагревании реагируют с Pb с выделением водорода и гидроксоплюмбитов типа Х 2 [Рb(ОН) 4 ].
1.4 Краткие химические свойства никеля
Нормальный водородный потенциал никеля равен -0,24 В. По отношению к воде никель устойчив. Органические кислоты действуют на никель лишь после длительного соприкосновения с ним. Серная и соляная кислоты медленно растворяют никель, разбавленная азотная - очень легко, концентрированная HNO 3 пассивирует никель, однако в меньшей степени, чем железо. При взаимодействии с кислотами образуются соли Ni (II). Почти все соли Ni (II) и сильных кислот хорошо растворимы в воде, растворы их вследствие гидролиза имеют кислую реакцию. Труднорастворимы соли таких сравнительно слабых кислот, как угольная и фосфорная. Большинство солей никеля разлагается при прокаливании (600- 800 °C). Одна из наиболее употребительных солей - сульфат NiSO 4 кристаллизуется из растворов в виде изумрудно-зеленых кристаллов NiSO 4 ·7H 2 O - никелевого купороса. Сильные щелочи на никель не действуют, но он растворяется в аммиачных растворах в присутствии (NH 4) 2 CO 3 с образованием растворимых аммиакатов, окрашенных в интенсивно-синий цвет; для большинства из них характерно наличие комплексов 2+ и . На избирательном образовании аммиакатов основываются гидрометаллургические методы извлечения никеля из руд.
ГЛАВА 2 - Физико-химические основы растворения меди и кристаллизации медного купороса
В настоящее время не существует единой теории химического и электрохимического растворения металлов, в том числе и меди, не разработана общая концепция, связывающая процессы, протекающие в жидкой фазе и на поверхности раздела «металл - раствор». Является актуальным дальнейшее развитие теории пассивации, так как при химическом и электрохимическом растворении меди создаются условия для формирования на поверхности твердой фазы из малорастворимых соединений Cu(I) и Cu (II), препятствующих дальнейшему растворению металла.
До настоящего времени являются актуальными вопросы влияния физико-химических факторов на скорость химического растворения металлов и сплавов, не решены вопросы взаимосвязи состава комплексов меди и их реакционной способности (либо каталитической активности) по отношению к процессу растворения меди.
2.1 Физико-химические основы растворения меди и ее сплавов в сернокислом растворе
Растворению меди в серной кислоте посвящено не так много работ.
Медь в концентрированной серной кислоте растворяется только при нагревании по уравнению:
Cu + 2H 2 SO 4 = CuSO 4 + 2H 2 O + SO 2 (1)
Кроме указанной главной, здесь происходят еще побочные реакции: в начале действия кислоты появляется светло-бурый осадок Cu 2 S, который сразу переходит в черный 2Cu 2 S.CuO, затем 2CuS.CuO и, наконец, CuS.CuO .
При взаимодействии меди с разбавленным раствором серной кислоты, содержащим также сульфат меди, в присутствии воздуха, кислород воздуха растворяется в кислоте, диффундирует к поверхности меди и окисляет ее до закиси меди:
4 Cu + O 2 = 2 Cu 2 O (2)
Закись меди растворяется в серной кислоте:
Cu 2 O + H 2 SO 4 = Cu 2 SO 4 + H 2 O (3)
Образующийся сульфат закиси меди легко окисляется в сульфат окиси меди:
2 Cu 2 SO 4 + 2 H 2 SO 4 + O 2 = 4 CuSO 4 + 2H 2 O (4)
Общая скорость процесса лимитируется наиболее медленной его стадией - окислением меди до закиси меди. Это объясняется малой растворимостью кислорода и медленной его диффузией к поверхности гранул меди. Процесс значительно ускоряется, когда в растворе уже присутствует медный купорос.
Повышение температуры, как и в других случаях, ускоряет химические реакции, но вызывает уменьшение растворимости кислорода, что замедляет окисление.
Растворимость кислорода уменьшается с ростом концентрации CuSO 4 в растворе. Поэтому при повышении концентрации CuSO 4 скорость растворения меди сначала увеличивается за счет каталитического действия CuSO 4 , а затем уменьшается вследствие недостатка кислорода. Максимум скорости растворения наблюдается при концентрации 120 г./л CuSO 4 (для раствора, содержащего ~ 110 г./л H 2 SO 4). Но даже при содержании в растворе 300 г./л CuSO 4 скорость растворения меди в 1,6 раза больше, чем в отсутствие медного купороса. С увеличением концентрации серной кислоты растворимость кислорода в ней уменьшается, но усиливаются ее окислительные свойства. Поэтому повышение кислотности раствора вызывает не очень большое уменьшение скорости растворения меди - всего на 10 % при повышении концентрации H 2 SO 4 с 2,5 до 20 %. Растворение меди значительно ускоряется в присутствии в растворе ионов железа вследствие деполяризации:
4 Fe 2+ + O 2 + 4 H + = 4 Fe 3+ + 2 H 2 O (5)
2 Cu + 4Fe 3+ = 2 Cu 2+ + 4 Fe 2+ (6)
Ионы Fe 2+ вновь окисляются в Fe 3+ и служат, таким образом, катализатором процесса. Доля растворяющейся меди под действием ионов Fe 3+ в растворе, содержащем ~110 г./л H 2 SO 4 , 60 г./л CuSO 4 и 20 - 22 г./л FeSO 4 , составляет около 60 % от всего количества меди, перешедшей в раствор.
Рисунок 1 - Зависимость между содержанием FeSO 4 в растворе медного купороса и содержанием железа в кристаллах CuSO 4 *5H 2 O. Содержание CuSO 4 * 5H 2 O в растворе (г/л): 1 - 400; 2-500; 3-550; 4-600.
Концентрация сульфата железа не должна превосходить в среднем 40 г./л, чтобы не получился продукт не соответствующий ГОСТу по железу (см. рисунок 1).
Существенным является обеспечение равномерного орошения (смачивания) гранул меди раствором. В местах, плохо орошаемых кислотой, образовавшаяся окисная пленка растворяется не полностью, вследствие малой своей растворимости кристаллизуется из раствора и цементирует при этом гранулы и шлам .
2.2 Коррозионные и анодные процессы на сплавах меди.
При растворении сплавов каждый компонент проявляет собственные электрохимические свойства. Из медных сплавов наиболее изучены латуни. В работе показано, что возможно как селективное растворение (СР) Zn с обогащением поверхностного слоя медью, так и равномерное растворение обоих компонентов с последующим восстановлением меди на поверхности латуни. Анодное растворение латуней обычно отличается от коррозионного отсутствием псевдоселективного растворения. Повышенные значения коэффициента селективности Zn (Z Zn) и более ранний переход от СР к равномерному наблюдаются с ростом j. Z Zn снижается во времени и при перемешивании раствора. В результате СР на поверхности латуни образуется тонкий обедненный цинком слой.
Равномерному растворению латуней способствуют сдвиг потенциала в анодную область и наличие в коррозионной среде окислителя. Соотношение Сu + /Сu 2+ зависит от рН раствора: при малых рН доля ионов Сu + мала, в щелочных растворах эта величина возрастает. В работе показано, что в аммиачных растворах на.-латуни возможно образование поверхностного слоя Сu 2 О, а СuСl на Сu38Zn - латуни в боратном электролите.
Проведены исследования по ионизации сплава Л-62 в концентрированных растворах FeCl 3 , CuCl 2 и в водно-ацетонитрильных растворах. При растворении Л-62 в растворах хлоридов происходит селективное растворение цинка, процесс контролируется растворением меди. Растворение латуни лимитируется диффузией продуктов в объем раствора. Обогащение поверхности медью более интенсивно в меднохлоридных растворах, что объясняется протеканием реакции контактного обмена. Поверхностными фазами являются слой, обогащенный медью, и CuCl. Замена части FeCl 3 на CuCl 2 интенсифицирует растворение латуни.
При анодном растворении латуни в водно- ацетонитрильных растворах до определенной концентрации ацетонитрила (70% мас.) увеличивается скорость ионизации сплава. Контролирующей стадией процесса является катодная. Обесцинкование, характерное для смесей с малой концентрацией ацетонитрила, быстро уменьшается во времени, сменяясь равномерным растворением латуни. В результате прямой ионизации Zn и Cu до ионов Zn (II) и Cu (II) (для медной составляющей двухэлектронная ионизация характерна для концентрированных растворов ацетонитрила), а также в результате реакций репропорционирования между ионами Cu (II) и участками, обогащенными медью, контактного обмена:
Zn + 2Cu 2+ → Zn 2+ + 2Cu + (54)
и образуется совокупность ионов цинка и меди как растворимых продуктов электрохимической коррозии, а также нерастворимые продукты - ZnO, CuCl и в меньшем количестве CuOH, Cu(OH) 2 , Zn(OH) 2 . Увеличение концентрации ацетонитрила вызывает исчезновение ионов Cu (I), образующихся в смесях, богатых ацетонитрилом, по реакциям репропорционирования и контактного обмена. Для медно - никелевых сплавов в начальный период растворения характерно СР никеля с последующим переходом к равномерному растворению при более длительной поляризации. Содержание Ni в поверхностной зоне (3-4 атомных слоя) понижается на ~ 30 %. Интегральный коэффициент селективности составляет 47, причем при анодном растворении из общего количества электричества на растворение Ni расходуется 70-80 %, а на Сu - только 10 %.
В работе исследована коррозионная стойкость сплавав Сu - Ni с различным содержанием никеля. Граница стойкости наблюдается при 50 ат. % Ni, а граница скорости коррозии - при 31-37 ат. % Ni. Показано превышение нестационарного анодного тока у сплава Сu30Ni по сравнению с Сu10Ni.
Зависимость скорости электрорастворения сплава от С Сl - варьирует с его составом. Определена критическая С Сl -, ниже которой сопротивление коррозии возрастает с уменьшением содержания Ni в сплаве, а выше - с его увеличением. В отсутствие сильных окислителей (Fе 3+) анодный процесс контролируется диффузией, а катодный - переносом заряда. Введение в электролит ионов Fе 3+ изменяет контроль стадий: анодная лимитируется переносом заряда, а катодная - диффузией. В хлорид - содержащих растворах Сu - Ni сплавы могут пассивироваться соединениями СuСl, Сu 2 О и Сu 2 (ОН) 3 Сl.
В работах на примере сплавов МН19, МНЖ Мц 30-0.8-1, МН Мц 40-1.5, МН Мц 43-0.5 было изучено коррозионное и анодное поведение Сu - Ni систем в кислых хлоридных и аммиачных растворах. Селективность растворения сплавов определятся как природой раствора, так и содержанием Ni в сплаве. В хлоридной среде сплавы с содержанием Ni до 29 % мас. активно растворяются с образованием ионов Ni(II) и Cu(I). Поверхность сплава обогащается CuCl и медью. При более высоком содержании Ni анодное растворение сплавов лимитируется растворением никеля. Такие сплавы обладают высокой поляризуемостью, характерной для пассивного состояния. При высокой анодной поляризации резкое увеличение тока сопровождается разрыхлением поверхности (кривые 1, 2; рисунок 8). Предварительная выдержка сплавов с высоким содержанием Ni в растворах NaCl активирует поверхность, вероятно, за счет специфической адсорбции Cl - ионов в широком диапазоне потенциалов (кривая 5, рисунок 8).
Аналогичный эффект оказывает повышение температуры. Растворенный кислород переводит сплавы в пассивное состояние. Коррозионное поведение в аммиачных растворах, подобно анодному, определяется содержанием Ni в сплаве: более высокое его содержание способствует быстрому обогащению поверхности сплава Ni-защищающим
компонентом. С увеличением времени травления повышается вероятность перехода в разряд стойких сплавов с меньшим содержанием Ni. Анодное растворение вызывает появление пассивирующего соединения NiO только у сплавов с содержанием Ni 43.5 %, причем тем быстрее, чем выше концентрация NH 3 . С целью выяснения возможности электролитического получения гидроксидов меди и железа как основы для производства ферритов в работах изучено влияние компонентов сплавов на электрохимическое поведение системы Fe-Cu в щелочных растворах и природа пассивирующих соединений. В области высоких поляризаций основными пассивирующими соединениями сплавов являются Cu(OH) 2 , Fe(OH) 2 и Fe(OH) 3 . Область пассивации (рисунок 9) глубокая с малыми значениями тока. Присутствие хлорид -ионов снижает концентрационный барьер Fe в сплаве, при котором регистрируется пассивация, что можно объяснить активирующим действием Cl - ионов. Для сплава с 38 % мас. Fe подобран режим электролиза с получением гидроксидного сырья для синтеза моноферрита меди. Последующая его термическая обработка дает совокупность продуктов в интервале температур:
20-200 о С CuFe 2 O 4 , FeFe 2 O 4 , Cu 2 O
300-400 о С CuFe 2 O 4 , Cu 2 O
500-600 о С CuFe 2 O 4 , CuO.
Таким образом, уже в электролитической ванне начинается образование феррита CuFe 2 O 4 . Полученные теоретические результаты позволили сформулировать принципы интенсификации процессов химического травления меди, заключающиеся в создании условий, благоприятствующих для формирования в жидкой фазе каталитически - активных комплексов меди (II) и для растворения поверхностных соединений меди (I). На этой основе разработаны новые составы медно - аммиачных травильных растворов с частичной заменой ионов хлора на ионы брома и йода, а также с введением в их состав аминов. Оптимизированы составы солянокислых растворов CuСl 2 с добавками ацетона или ацетонитрила. Интенсификация и совершенствование процессов травления были осуществлены и для персульфатных травильных растворов, использующихся для изготовления печатных плат с металлическими резистами. Новые технологические процессы травления позволяют значительно повысить емкость растворов по вытравленной меди, скорость травления с сохранением ее равномерности во времени при одновременном обеспечении высокого качества обрабатываемой поверхности.
2.3 Теоретические основы электролиза меди
В данном разделе рассматриваются общие электрохимические принципы анодного и катодного поведения меди при электролизе на примере сернокислого электролита. Эти закономерности являются базовыми при проектировании электрохимических методов переработки медных, латунных и бронзовых отходов.
Электролитическое рафинирование цветных металлов - разновидность процесса электролиза в водных растворах с выделением металла. Цель - рафинирование, т.е. очитка меди от примесей путем электролитического растворения загрязненной примесями анодной меди (анодный процесс) с последующим электроосаждением меди на катоде (катодный процесс). Получается чистая электролитическая медь в форме катодных отложений, а примеси концентрируются в донном шламе (драгоценные металлы, селен, теллур и т.д.) или в электролите в растворенной форме.
Электролитическое рафинирование меди происходит в электрохимической системе: электроды (медный катод - отрицательно заряженный, медный анод - положительно заряженный) и раствор электролита.
(-) Cu/CuSO 4 -- H 2 SO 4 /Cu (+)
При наличии внешнего источника постоянного тока на катоде идет процесс выделения меди:
Cu 2+ + 2e à Cu
на аноде, кроме растворения меди:
Cu - 2e à Cu 2+
образуются примеси, переходящие в электролит или в анодный шлам.
Протекание тока через электрохимическую систему вызывают качественные изменения, которые претерпевают ионы, атомы и молекулы на границе раздела фаз электрод - электролит в системе возникает перераспределение электрического заряда, образуется двойной электрический слой и возникает скачок потенциала - электродный потенциал. Нормальный (стандартный) электродный потенциал - потенциал электрода - металла, опущенного в раствор, содержащий его ионы при условии, если активность или отношение активностей ионов относительно которых электрод является обратимым, равно единице.
E 0 , B
Cu 2+ + 2e = Cu +0.34
Cu + + e = Cu +0.52
Электродные процессы при катодном осаждении и ионизации меди из растворов сопровождаются главным образом концентрационной поляризацией.
Поляризация - это отклонение потенциала электрода его равновесного значения при прохождении тока через электрод. Концентрационная поляризация - смещение потенциала под влиянием изменения концентрации электролита при электролизе, вызванное замедленностью доставки ионов или их отвода от поверхности электрода. Убыль концентрации ионов разряжающего металл пропорциональна всему току, проходящему через систему, а доставка их к катоду соответствует лишь доле тока, определяемой числом переноса данного иона.
При концентрационных изменениях в приэлектродном слое возникает диффузия, которая способствует выравниванию концентрации веществ. Диффузионные ограничения являются причиной торможения электродных реакций.
Равновесный потенциал электрода (Е) - скачок электрического потенциала между электродом и раствором, устанавливающийся при равенстве скоростей реакции окисления и восстановления.
Масса выделившегося на катоде металла зависит от его электрохимического эквивалента (количество вещества при прохождении через раствор электричества = 1Ач), а также от пропущенного через систему количества электричества.
Электрохимический эквивалент равен:
q = m/n*26,8
где m - молекулярная масса,
N - число электронов, участвующих в элементарном акте реакции.
Теоретическое количество металла выделившегося на электроде при прохождении тока через электрохимическую систему определяют по формуле:
Q=I*τ*q
Практическое количество выделившегося металла отлично от расчетного по причинам:
1. совместный разряд нескольких ионов с различной валентностью,
2. перезарядка ионов,
3. взаимодействие продуктов электродных реакций между собой или с электролитом.
Количество выделившегося металла регламентируется величиной выхода по току. Анодный выход по току больше катодного по ряду причин:
Растворение оксида меди, присутствующего в анодах огневого рафинирования:
Cu 2 O + 2H 2 SO 4 + 0,5 O 2 = 2CuSO 4 + 2H 2 O
Химическое растворение меди:
Cu + H 2 SO 4 + 0,5 O 2 = CuSO 4 + H 2 O
Окисление одновалентных ионов меди:
Cu 2 SO 4- + H 2 SO 4 + 0,5O 2 = 2CuSO 4 + H 2 O
Превышение анодного выхода по току приводит к накоплению меди в электролите, снижению кислотности, что требует корректировки состава электролита по основным компонентам - Cu, H 2 SO 4 , осуществляемой либо подключением в товарных сериях ванн регенерации, либо выводом части электролита в отделение обезмеживания, для очистки меди.
Основная задача рафинирования меди - полное удаление из анодной меди примесей, условно разбиваемых по знаку электрохимического потенциала и его величине на группы:
Ni, Fe, Zn и др., потенциалы которых электроотрицательнее меди.
Мышьяк, сурьма, висмут - потенциалы которых близки к потенциалу меди.
Драгметаллы (Ag, Au), потенциалы которых электроположительнее меди.
Ряд примесей (Se, Te, S, O 2) образуют с медью нерастворимые соединения и переходят в шлам. Свинец, образующий в электролите сернокислые соли и олово, дающее в растворах основные соли, также осаждаются со шламом. Металлы (примеси) - Ni, Fe, Zn при химическом растворении переходят в раствор, накапливаются в нем и негативно влияют на процесс электрокристаллизации меди, ухудшают качество меди.
Примеси мышьяка, сурьма, висмут наиболее опасны из-за близости потенциала их выделения к потенциалу разряда ионов меди и способностью образовать перенасыщенные растворы, содержащие примеси в значительных количествах.
Из группы Ag, Au в электролит в незначительных количествах переходит Ag в виде сульфата, концентрация которого резко уменьшается за счет введения ионов хлора в виде NaCl или HCl. Общее содержание примеси может быть определена из соотношения:
A=(100*C n /I)*(1/K p + 1/K д )
где С n - концентрация примесей в растворе.
Константа скорости разряда примеси
Константа скорости конвективной диффузии.
С увеличением скорости циркуляции возрастает переход примеси в осадок. Содержание примеси уменьшается с уменьшением ее концентрации в электролите.
Накопление Ni в электролите осложняет процесс электролиза ввиду появления состояния пассивации анода, ухудшает физико-химические свойства электролита. Технические приемы снятия анодной пассивации:
Спец. обработка поверхности анода,
Подбор определенного состава электролита,
Повышение температуры электролита,
Использование нестационарных токов (реверс и импульс).
Основной технологической операцией по выводу никеля из электролита и поддержанию его стабильного состава является передача части раствора в купоросный цех с получением никельсодержащего продукта.
2.4 Теоретические основы цементации металлов
Цементация, или контактное вытеснение - одно из весьма распространенных в технической электрохимии явлений, при котором более электроположительный металл вытесняется из раствора своей соли металлом с более электроотрицательным потенциалом. Например:
Cu 2+ + Fe = Cu + Fe 2+
Из раствора простой соли (например, медного купороса) медь вытесняется металлическим железом. Цементация широко используется в гидрометаллургии для очистки электролитов от примесей, имеющих более положительные О/В-потенциалы по сравнению с осаждаемым целевым металлом. Метод надежен и не требует сложного аппаратурного оформления. В гальванотехнике явление цементации иногда может быть использовано для получения гальванических покрытий. Однако, как правило, оно нежелательно, так как цементационный слой осаждаемого металла имеет структуру рыхлого осадка, плохо связан с основой и ухудшает адгезию металла покрытия к основе.
Условием равновесия осаждаемого (М2) и цементирующего (М1) металлов является равенство их электрохимических потенциалов.
Учитывая, что потенциал цементирующего металла значительно сильнее сдвинут в сторону отрицательных значений по сравнению с потенциалом осаждаемого, приходим к выводу о возможности достижения весьма глубокой очистки раствора от ионов M z 2+ с помощью такого простого метода. Однако термодинамические возможности цементации не всегда могут быть полностью реализованы в связи с существованием кинетических затруднений реакций растворения цементирующего металла и выделения осаждаемого из раствора.
В основе цементации лежит коррозионный процесс, иллюстрируемый обычно с помощью поляризационной диаграммы (рис. 2).
Рисунок 2 - Поляризационная диаграмма контактного обмена
Потенциал растворения цементирующего металла и осаждаемого из раствора устанавливается при плотности тока цементации ic . Из рис. 2 следует, что скорость процесса, выраженная в единицах плотности тока, определяется не только движущей силой процесса - разностью стационарных потенциалов в исходном растворе, но и характером кинетических затруднений как катодного, так и анодного процессов.
В связи с этим различают два вида контроля скорости цементации: активационный и смешанный. В зависимости от характера торможений электродных процессов по-разному изменяется и поверхность электрода: при подавляющем контроле стадии перехода в катодном процессе поверхность электрода можно рассматривать практически не зависящей от времени; преобладание диффузионного контроля приводит к образованию рыхлого цементационного осадка.
2.5 Теоретические основы кристаллизации металлов из водных растворов.
Во многих технологических процессах, связан-ных с обработкой твердых материалов в жидкой среде, приходится путем кристаллизации выделять в виде кристаллов растворенные в жидкости твердые вещества.
Кристаллизация представляет собой процесс выделения твердой фазы при затвердевании веществ, находящихся в жидком со-стоянии (из расплава), или процесс выделения твердого растворенного вещества из раствора.
Кристаллы представляют собой твердые химически однородные тела правильной формы. Строение кристаллов характеризуется сим-метричным расположением атомов, ионов и молекул в узлах простран-ственной решетки, которая образуется тремя взаимно пересекающимися системами плоскостей. В зависимости от условий образования кристаллов ско-рость роста их по отдельным граням может быть различной, вследствие чего кристаллы, сохраняя ту же самую кристаллическую решетку, прини-мают вытянутую или плоскую форму в зависимости от температуры и вязкости среды. Каждая из форм кристаллов остается устойчивой лишь в опреде-ленном интервале значений температуры и давления. При достижении предельных условий происходит переход одной кристаллической формы в другую, сопровождающийся тепловым эффектом; границы этого пере-хода определяются так же, как и при изменении агрегатного состояния вещества. Кроме того, каждая из кристаллических форм обладает отлич-ной, свойственной только ей упругостью паров и растворимостью. В технологии многообразие форм кристаллов используют для полу-чения одного и того же вещества в виде кристаллов определенной формы, обладающих различными свойствами, для чего создают соответствую-щие условия кристаллизации. Так, в зависимости от температуры кристаллизации некоторые ве-щества могут быть получены различного цвета. Например, йодная ртуть в зависимости от температуры может быть выделена в виде осадка, окра-шенного в желтый или в красный цвет. Изменяют также свой цвет при различной температуре кристаллизации хромовые соли свинца. Форма и величина кристаллов оказывают существенное влияние на их дальнейшую обработку путем фильтрования, при котором оба эти фактора значительно влияют на скорость процесса. Известно, что чем крупнее кристаллы и отчетливее выражена их кристаллическая форма, тем эффективнее протекает процесс фильтрования.
Существенное влияние на кристаллизацию оказывает процесс гидратации, при котором выделяющиеся из раствора одна или не-сколько молекул растворенного вещества соединяются с одной или не-сколькими молекулами растворителя. При этом число присоединяющихся молекул растворителя может быть различным в зависимости от темпера-туры и концентрации, при которых проводится кристаллизация.
Вследствие гидратации вещество из раствора выделяется в виде кристаллогидратов определенной формы, содержащих вполне определенное количество молекул растворителя (воды), причем содер-жание кристаллизационной воды в кристаллах сказывается не только на их форме, но и на свойствах.
Кристаллогидраты обладают определенной упругостью пара. Если упругость их пара больше упругости паров воды в окружающем воздухе при данной температуре, то кристаллы при хранении на воздухе теряют кристаллизационную воду - выветриваются. Наоборот, если упругость пара над кристаллогидратом меньше упругости паров воды в окружающем воздухе, кристалл «притягивает» из окружающего воздуха воду и постепенно «плавится». Для этих кристал-лов при хранении на воздухе содержание кристаллизационной воды должно быть таким, чтобы не нарушалась форма кристаллов.
Все вещества, в том числе и твер-дые, обладают способностью в той или иной степени растворяться в раз-личных жидких растворителях. Степень растворимости и концентрацию растворов чаще всего выражают в весовых процентах растворенного вещества по отношению к общему весу раствора или в граммах растворен-ного вещества на 100 г растворителя. Растворимость веществ зависит от их химической природы, свойств растворителя и температуры. Данные о растворимости различных ве-ществ находят опытным путем и обычно изображают в виде кривых за-висимости растворения от температуры. Растворимость многих веществ изображается плавной кривой, без излома, причем, как правило, с повышением температуры растворимость возрастает.
Для многих веществ, образующих кристаллогидраты, кривые рас-творимости имеют изломы; растворимость таких веществ может с повы-шением температуры уменьшаться.
Определение растворимости веществ при заданных температурах имеет большое практическое значение, но надежных расчетных формул нет, и в каждом конкретном случае приходится пользоваться опытными данными.
Раствор, который содержит максимально возможное для данной температуры количество растворенного вещества, называют насыщенным. Понижение температуры насыщенного раствора ведет к выделе-нию из него части растворенного вещества; при этом количество раство-ренного вещества, остающегося в растворе, будет соответствовать состоя-нию его насыщения при температуре, до которой охлажден раствор. Наоборот, повышение температуры раствора в большинстве случаев дает возможность увеличивать концентрацию до тех пор, пока раствор снова не станет насыщенным. Зная зависимость растворимости вещества от температуры, можно проводить его кристаллизацию. Понижая температуру раствора путем охлаждения или удаляя из раствора часть растворителя путем испарения или выпаривания, нарушают фазовое равновесие, вследствие чего раствор пересыщается и часть растворенного вещества переходит в твердую фазу, образуя кристаллы определенной структуры.
На рисунке 3 приведена кривая растворимости в воде медного купороса в системе с серной кислотой.
Как уже отмечалось, для по-лучения кристаллов должно быть сдвинуто фазовое равновесие, т. е. раствор должен быть пересыщен. При этом необходимо образование мельчайших кристаллических ядер-центров, из которых затем вырастают кристаллы определенной вели-чины. Таким образом, весь процесс кристаллизации можно разделить на две стадии: образование ядер вследствие нарушения фазового равновесия раствора и рост образовавшихся ядер в растворе.
Механизм образования ядер-центров кристаллизации до сих пор теоретически недостаточно выяснен. Из-вестно лишь, что если раствор твердого вещества, имеющего нормальную растворимость (возрастающую с повышением температуры), охлаждать до температуры ниже предела его насыщения, то начинается образование микроскопических ядер-центров, которое зависит от интенсивности охлаждения, скорости и способа перемешивания, температуры и свойств вещества, а также содержания примесей.
Рисунок 3 - Кривые растворимости медного купороса в системе с серной кислотой при различных температурах.
Рисунок 4 - Растворимость в системе ZnSO 4 - H 2 SO 4 - H 2 O. Твердые фазы: ниже acd - ZnSO 4 *7H 2 O; в области abc - ZnSO 4 *6H 2 O; выше bcd - ZnSO 4 *H 2 O
Практически установлено, что образованию большого количества ядер благоприятствуют быстрое охлаждение, энергичное перемешивание, высокая температура и небольшой молекулярный вес растворенного ве-щества. Количество возникающих при кристаллизации ядер непосредственно сказывается на форме и величине кристаллов. Появление только небольшого числа зародышей-ядер, способствует образованию крупных кристаллов. Медленный рост крупных кристаллов позволяет получать более полногранные формы кристаллов с хорошо развитыми плоскостями.
В случае, когда образуется значительное количество ядер-центров в единице объема раствора, получают мелкокристаллические осадки из микроскопических кристаллов со слабо развитыми гранями. В этом слу-чае образуются преимущественно кристаллы пластинчатой или игольча-той формы. Кроме того, если большое число ядер возникает в сильно разведен-ных растворах, то твердая фаза получается столь тонко раздробленной, что ее трудно отличить от коллоидных осадков.
Многие растворы, как, например, растворы глауберовой соли, мо-гут быть сильно пересыщены без выделения кристаллов. Выяснено, что для возбуждения процесса кристаллизации таких пересыщенных рас-творов необходимо ввести в раствор извне хотя бы один мелкий кристалл этой соли или какого-либо другого вещества с той же кристаллической структурой. Процесс кристаллизации протекает значительно легче вокруг имею-щихся в растворе кристаллов или даже мельчайших кристаллических обломков того же вещества. Поэтому весьма часто при проведении про-цесса кристаллизации предварительно вводят в раствор некоторое коли-чество кристаллов выделяемого вещества.
Развитие микроскопических ядер в видимые кристаллы начинается с того момента, когда возникли кристаллические центры-ядра, причем требуется постоянный приток твердого вещества к поверхности граней кристалла. В растворе, находящемся в состоянии покоя, по мере роста кри-сталлов жидкость, находящаяся в непосредственном соседстве с гранями кристалла, перестает быть пересыщенной, и если в эту зону не будет по-ступать материал из других соседних областей, то рост кристаллов пре-кратится. Перенос вещества, потребного для роста кристалла в неподвижной среде, происходит вследствие возникновения в растворе одновременно с ростом кристалла диффузионных и конвекционных токов.
Диффузионные токи возникают вследствие диффузии, т. е. процесса выравнивания концентраций раствора по всей его массе, проте-кающего во времени.
В основном все методы кристаллизации можно раз-бить на две группы:
1) кристаллизация с удалением части растворителя;
2)кристаллизация без удаления растворителя. Кристаллизация может проводиться периодически или непрерывно.
В некоторых случаях для осуществления кристаллизации требуется понизить растворимость кристаллизуемого продукта, что достигается введением в раствор какой-либо растворимой соли в сухом виде или в виде насыщенного раствора.
Если раствори-мость кристаллизуемого продукта с понижением температуры изменяется мало, то кристаллизацию чаще всего проводят путем удаления из рас-твора, некоторой части растворителя.
Удаление растворителя может быть осуществлено двояко: путем кипячения (выпаривания) или путем испарения при температурах, зна-чительно более низких, чем температура кипения раствора.
Соответственно различают следующие виды кристаллизации с уда-лением части растворителя: 1) выпаривание с кристаллизацией, 2) кри-сталлизация с воздушным охлаждением, 3) вакуум-кристаллизация.
При выпаривании водных растворов в закры-тых выпарных вакуум-аппаратах можно поддерживать низкие темпера-туры и интенсивно удалять растворитель
Для получения крупных кристаллов нельзя превысить предел кон-центрации, достигаемый при выпаривании. Не всегда следует выпари-вать растворы до насыщения, так как при сливании таких растворов в кристаллизатор процесс кристаллизации протекает слишком быстро, что ведет к образованию очень мелких кристаллов, а иногда весь раствор затвердевает. Поэтому в каждом конкретном случае необходимо знать предельную концентрацию, до которой можно выпаривать раствор, что устанавливают только опытным путем.
Удаление растворителя путем его испарения при атмосферном давлении протекает весьма медленно и кристаллизация длится значи-тельное время, что создает условия для медленного роста кристаллов. Таким методом пользуются, в частности, при кристаллизации соли из морской воды или на соляных промыслах, где кристаллизацию проводят в больших бассейнах.
Но, как отмечалось выше, рост кристаллов зависит от того, как быстро происходит перемещение кристаллизуемого продукта из раствора непосредственно к граням кристаллических центров. Поэтому для уско-рения кристаллизации необходимо либо искусственно уменьшить длину пути к центрам кристаллизации, либо создать путем перемешивания ин-тенсивные токи жидкости.
В производственных условиях кристаллизацию с удалением части растворителя путем испарения его в окружающий воздух проводят в от-крытых прямоугольных ящиках-кристаллизаторах, в которых подве-шиваются ленты или нити из химически стойкого материала.
Вследствие большой поверхности нитей (лент) на них осаждается основная масса чистых кристаллов; примеси осаждаются на дно и уда-ляются с маточным раствором.
Очистку нитей (лент) производят на специальных наклонных сто-лах, где с кристаллов стекает маточный раствор. Для более полного удаления маточного раствора кристаллы центрифугируют, а затем сушат.
При расчете кристаллизаторов такого типа необходимо учитывать охлаждение раствора вследствие его испарения и отдачи тепла в окру-жающую среду через стенки аппарата. Количество жидкости, испаряю-щейся в единицу времени со свободной поверхности зеркала испарения, можно подсчитать по формуле самоиспарения.
Кристаллизация путем испарения растворителя без нагревания и перемешивания в большинстве случаев проводится исключительно для получения более крупных, отчетливо образованных кристаллов.
Крупные кристаллы не всегда являются более чистыми по сравне-нию с мелкими; часто крупные кристаллы срастаются в целые агрегаты, внутри которых содержится значительное количество маточного рас-твора и примесей.
Удаление растворителя путем испарения его при атмосферном да-влении протекает медленно и требует громоздкой аппаратуры. Ускорение процесса кристаллизации достигается при перемешивании раствора в шнековых кристаллизаторах, которые могут работать периодически и непрерывно.
Охлаждение раствора в кристаллизаторе такой конструкции проис-ходит только естественным путем вследствие испарения растворителя с открытой поверхности; несмотря на это, благодаря перемешиванию процесс кристаллизации в шнековых аппаратах протекает примерно в 6-7 раз быстрее, чем в кристаллизаторах ящичного типа.
К числу кристаллизаторов, непрерывно работающих с удалением части растворителя, относятся качающиеся и барабанные вращающиеся кристаллизаторы.
Более производительными, чем кристаллизаторы с естественным охлаждением и самоиспарением раствора, являются аппараты для кри-сталлизации, работающие под вакуумом.
Принцип вакуум-охлаждения заключается в том, что если раствор поместить в замкнутый аппарат и создать в последнем вакуум, то вслед-ствие самоиспарения раствор охлаждается до температуры, соответст-вующей упругости пара над раствором.
Конденсацию выделяющегося пара производят, используя раствори-тель, в конденсаторах смешения или в поверхностных конденсаторах. Тепло конденсации передается растворителю, вследствие чего довольно значительно сокращается расход тепла.
В периодически действующих аппаратах вся жидкость удаляется при постоянном (мак-симальном) вакууме. В многоступенчатых ва-куум-кристаллизационных установках часть жидкости (в первых ступенях) испаряется при меньшем вакууме, а максимальный вакуум достигается в последней ступени. Эти уста-новки работают непрерывно и обладают зна-чительной производительностью.
Кристаллизация без удаления растворителя. Хотя при кристаллиза-ции с удалением растворителя кристаллы получаются крупными, зато, как было отмечено, создаются благоприят-ные условия для образования больших сра-стающихся агрегатов. В результате такого сращивания в кристаллизуемый продукт попадают примеси в виде маточного рас-твора. Кроме того, удаление растворителя методом испарения протекает весьма мед-ленно, а выпаривание обходится сравни-тельно дорого. Поэтому очень часто кри-сталлизацию проводят, охлаждая раствор водой или холодильным рассолом в аппа-ратах, в которых осуществляется непрерыв-ный ток раствора, или в аппаратах, снабжен-ных механическими мешалками.
Кристаллизатор с перемеши-ванием и охлаждением представляет собой герметически закрытый цилиндрический котел с плоской крыш-кой и коническим дном; котел снабжен мешалкой. Охлаждение производится водой или холодильным рассолом, которые пропускаются через змеевик. Аппарат разгружают через штуцер, имеющийся в днище. Такие аппараты изготовляют также с рубашками, при этом, чтобы устранить вы-падание кристаллов на стенках аппарата (что повело бы к значительному ухудшению теплопередачи), лопасти мешалки снабжают скребками или металлическими щетками.
Кристаллизаторы этого типа работают периодически или непрерывно. При непрерывной работе соединяют несколько аппаратов последовательно и раствор перетекает из одного кристаллизатора в другой.
ГЛАВА 3 - Существующие технологии переработки медьсодержащих твердых материалов
Согласно существующей литературе можно сделать следующую классификацию технологий производства купороса (детальное описание технологий приводится ниже)
Таблица - Возможные технологии переработки медьсодержащих отходов, латунной и бронзовой стружки
Сырье | Механизм получения | Рабочий раствор или процесс | Методика |
|
Медь чистая | Химический | Серная кислота разбавленная | Прямое растворение |
|
Серная кислота концентрированная | Прямое растворение |
|||
Соляная кислота концентрированная | Прямое растворение |
|||
Хлорид меди (II) или раствор поваренной соли | Прямое растворение |
|||
Метод натравочной башни | Прямое растворение |
|||
Электрохимический | Сульфатный электролит | Побочный продукт |
||
Растворимый анод, электролит - любая соль щелочного металла | Получение гидроксида с растворением в серной кислоте |
|||
Растворимый анод, диафрагма, электролит - любая соль щелочного металла | Прямое получение купороса и щелочи без затраты кислоты |
|||
Серная кислота | Вертикальный электролизер с потоком кислоты от катода к аноду |
|||
3.1 Метод сернокислого выщелачивания. Технологии 1,2 [ 1 ]
Для получения чистого медного купороса растворяют медь в крепкой или разбавленной наполовину водой серной кислоте. Раствор разбавляют водой, нагревают, отфильтровывают осадки, фильтрат выпаривают, кристаллизуют и полученные кристаллы очищают повторной кристаллизацией. В настоящее время в большинстве случаев предпочитают растворять медь в слабой серной кислоте при доступе воздуха. Для этого куски металла (обрезки, опилки и т. п.) закладываются в деревянные чаны, опаянные внутри свинцом и расположенные друг над другом, причем на дно чана кладутся более крупные куски. В верхний чан сверху пускают камерную серную кислоту, разбавленную маточным раствором и промывными водами от предшествовавших кристаллизаций до 10° - 30°В. и нагретую паром до 40° - 80°С. Раствор пропускают для насыщения последовательно через нижележащие чаны и затем или прямо выпускают в опаянные свинцом деревянные ящики, где при охлаждении кристаллизуется медный купорос, или предварительно выпаривают его до 40° - 42°В. Кристаллы М. купороса после первой кристаллизации выгребают, дают стечь маточному раствору, обмывают холодной водой, растворяют в возможно малом количестве горячей воды, вновь кристаллизуют, обмывают холодной водой и просушивают, медный купорос получается при этом очень чистый, почти без примеси железа и цинка. Вместо серной кислоты пользуются иногда для растворения меди выделяющеюся при обжигании серного колчедана сернистой кислотой, которую вместе с воздухом прогоняют через башню, наполненную медным ломом и нагретую паром до 100°С. Образующийся медный купорос растворяется притекающим сверху маточным раствором из кристаллизаторов, стекающий раствор прогоняется еще раз через башню для более полного насыщения, кристаллизуется, промывается и перекристаллизовывается, после чего кристаллы содержат от 98 до 99% чистого медного купороса.
Для получения больших и красивых кристаллов медного купороса, какие требуются в торговле, необходимо иметь при кристаллизации по возможности нейтральные и не слишком крепкие растворы и медленное охлаждение в закрытых (особенно зимой) больших кристаллизаторах. Лучшие кристаллы садятся на свинцовых лентах, подвешиваемых в растворе медного купороса. Сушка кристаллов медного купороса должна происходить при невысокой темп. (37° - 40°С) и в затененном помещении. При нечистоте исходных материалов медный купорос может содержать железо и цинк, что при некоторых производствах, напр. при приготовлении красок, нежелательно (железа допускается не более 1 / 2 %, а цинк, хоть и менее вреден, но все же краски выходят светлее, и невыгодно оплачивать его, как медь). Для удаления железа при приготовлении медного купороса предложено много способов, обыкновенно же выделяют его сильным прокаливанием медного купороса в пламенной печи, причем железо переходит в нерастворимую окись, или же осаждают железо углекислой медью или окисью меди. Под именем двойного, или смешанного, купороса (адмонтский, байрейтский или зальцбургский купорос) идет в торговлю для красилен и для смачивания хлебных зерен голубовато-зеленая изоморфная смесь медного купороса с железным, а иногда еще и с цинковым. Состав такого купороса непостоянен.
3.2 Получение медного купороса при окислении меди хлорной медью. Технология 4
Этот метод основан на образовании хлористой меди из хлорной и металлической меди:
Cu + CuCl 2 = 2CuCl
(хлористую медь получают также хлорированием цементной меди в растворе поваренной соли). Хлористую медь окисляют воздухом с образованием оксихлорида меди:
6CuCl + 1,5O 2 +3H2O = 3
Оксихлорид растворяют в серной кислоте, в результате чего образуется раствор сульфата меди и регенерируется хлорная медь
3 + 3H 2 SO 4 = 3CuSO 4 + 3CuCl 2 + 6 H 2 O
Получение оксихлорида меди осуществляют в бетонном баке, куда загружают медь и заливают раствор хлорной меди. После этого продувают массу воздухом, пока вся металлическая медь не перейдет в нерастворимый оксихлорид. После отстаивания и декантации пульпу растворяют при нагревании в серной кислоте. При охлаждении раствора из него кристаллизуется CuSO 4 * 5H 2 O. Маточный раствор возвращают в процесс. Этим способом можно получать также хлорокись меди.
3.3 Производство медного купороса из медного лома методом натравочной башни. Технология 5
Гранулированную медь загружают в натравочную башню, высотой около 6 м, диаметром 2,5 м. Башня изготовлена из листовой стали, внутри футерована кислотоупорным кирпичом и диабазовыми плитками. На высоте 0,5 - 0,9 м от дна в башне имеется ложное днище, лежащее на колосниковой решетке из стальных балок, опаянных свинцом. На ложном днище находится слой меди, высоту которого поддерживают периодическими загрузками на уровне 0,25 м от крышки башни. Под крышкой помещена турбинка, с помощью которой медь непрерывно орошается смесью серной кислоты с маточным раствором. Количество находящейся в башне меди составляет 22 - 28 т.
В башне происходит одновременно окисление и растворение меди. Эти процессы идут с выделением тепла, достаточным для повышения температуры до необходимого уровня, то есть до 70 - 85 0 С. Для окисления меди в башню под колосниковую решетку вдувают воздух в смеси с паром. Пар подают для нагревания воздуха. Вдувание холодного воздуха вызвало бы охлаждение щелока и выделение из него кристаллов медного купороса, что привело бы к закристаллизовыванию нижнего слоя гранулированной меди. Подачей пара регулируют и температуру в башне. Уходящая из нее паро-воздушная смесь выбрасывается в атмосферу. С 1 м 3 натравочной башни можно получить в сутки более 1,3 т. медного купороса.
Орошающий щелок имеет температуру 55 - 60 0 С и содержит 20 - 30 % CuSO 4 ∙ 5 H 2 O, и 12 - 19 % свободной H 2 SO 4 . Оптимальная плотность орошения натравочной башни, равная 1,5 - 2,1 м 3 /(м 2 ∙ ч), обеспечивает образование на поверхности медных гранул очень тонкой жидкостной пленки, через которую кислород диффундирует к меди с достаточной скоростью. При большей плотности орошения происходит снижение производительности башни, которое происходит после кратковременного ее возрастания, башня как бы «вымывается».
Вытекающий из натравочной башни горячий щелок (74 - 76 0 С) представляет собой почти насыщенный раствор медного купороса - он содержит 42-49 % CuSO 4 ∙ 5 H 2 O и 4 - 6 % свободной H 2 SO 4 . Этот щелок подают центробежным насосом из хромоникелевой стали во вращающийся кристаллизатор непрерывного действия с воздушным охлаждением раствора. Смесь кристаллов медного купороса с маточным раствором через сборник с мешалкой поступает в центрифугу из нержавеющей стали, где кристаллы, отжатые от маточного раствора, промываются водой. На центрифугирование поступает пульпа с соотношением Т: Ж от 1: 2 до 1: 1,5. Отфугованный продукт, содержащий 4 - 6 % влаги и 0,15 - 0,2 % кислоты, высушивают в барабанной сушилке воздухом при 90-100 0 С. Маточный раствор и промывную воду после смешения с серной кислотой возвращают в производственный цикл.
В маточном растворе происходит постепенное накопление примесей, все больше загрязняющих продукт. Содержащийся в медном купоросе сульфат никеля можно удалить с достаточной полнотой при однократной перекристаллизации. Для удаления FeSO 4 необходима многократная перекристаллизация. Получение медного купороса с содержанием 99,9 % CuSO 4 ∙ 5 H 2 O однократной перекристаллизацией из раствора, насыщенного при 70 0 С, возможно при содержании в нем не более 0,3 % NiSO 4 и не более 0,15 % FeSO 4 .
Если в растворе больше 40 г./л FeSO 4 , то количество железа в продукте больше 0,4 %, то есть выше нормы, допускаемой ГОСТом для продукта III сорта. Из растворов, содержащих больше 100 - 120 г./л FeSO 4 , выделяются смешанные кристаллы железного и медного купоросов с характерной сине-зеленой окраской.
Содержание железа в кристаллах медного купороса можно уменьшить предварительным окислением Fe 2+ в Fe 3+ . Окислителем может служить воздух (длительный барботаж), азотная кислота, перекись водорода и др. Степень очистки повышается в 2 - 4 раза при добавке к раствору незначительного количества HF (плавиковой кислоты), что приводит к образованию фторидных комплексов Fe 3+ . Установлено также, что при усилении перемешивания в процессе кристаллизации получаются кристаллы с меньшим содержанием железа, но и размеры их уменьшаются. Присутствие ионов никеля также уменьшает размеры кристаллов, а мышьяка - увеличивает.
На производство 1 т. кристаллического медного купороса расходуют: 0,27 - 0,29 т. металлической меди и 0,39 - 0,40 т. серной кислоты (100 %).
На заводе имени Войкова общие затраты тепла на производство медного купороса составляли 0,76 мгкал на 1 т. продукта. Расход тепла распределяется следующим образом. В натравочную башню через инжекторы вводится 47 % тепла, на подогрев воздуха в калориферах сушильного агрегата затрачивается 26 % тепла и 27 % тепла расходуется на подогрев раствора в сборниках, на разогрев мазута в цистернах и т. д. Количество тепла, выводимого с паро-воздушной смесью, больше тепла, вводимого с паром вследствие дополнительного парообразования, обусловленного выделением тепла реакцией. Поэтому вместо паро-воздушной смеси можно вдувать в башню теплый воздух из кристаллизатора с добавкой 20 - 25 % пара от обычного количества, при температуре смеси, исключающей закристаллизовывание нижнего слоя гранул в башне.
Ввод пара в натравочную башню может быть и вовсе исключен при осуществлении процесса с рециркуляцией паро-воздушной смеси. Отходящую из башни паро-воздушную смесь с температурой ~ 80 0 С направляют при помощи вентилятора из нержавеющей стали под ложное дно башни. При осуществлении процесса по такой схеме возможно введение в цикл газообразного кислорода, что значительно интенсифицирует растворение меди.
Отходом производства медного купороса являются илы, скапливающиеся в резервуарах с производственными растворами. Количество илов составляет 1 - 2 % от перерабатываемой меди. Состав их различен; они могут содержать до 8,5 % Ag 2 O, до 5 % Bi 2 O 3 , 0,05 - 0,1 % Au, Pt, Pd. Такие илы могут быть переработаны гидрометаллургическими методами для извлечения из них ценных металлов.
Предложено получать медный купорос из натравочного щелока добавкой к нему серной кислоты (башенной, купоросного масла, олеума или SO 3) до содержания свободной H 2 SO 4 60 % и более. При этом быстро осаждается мелкокристаллический белый безводный сульфат меди, примеси же остаются в растворе. CuSO 4 отфуговывают и растворяют в чистом маточном растворе медного купороса, из которого кристаллизуется CuSO 4 ∙ 5 H 2 O. Кислый щелок после осаждения безводного CuSO 4 возвращается на растворение меди. После накопления в нем значительного количества ценных примесей (никель, цинк, серебро и др.) их можно извлечь. Преимущество этого способа - в простой и быстрой кристаллизации медного купороса без затраты тепла и холода и высокой чистоте продукта.
Можно вообще отказаться от выпуска пятиводного сульфата меди и выпускать безводный продукт, концентрация меди в котором больше (39,8 % вместо 25,5 % в CuSO 4 ∙ 5 H 2 O). Производство и транспорт его будут дешевле, хотя он и потребует более тщательной упаковки из-за гигроскопичности. Впрочем, даже при небрежной упаковке на поверхности белого порошка появится лишь синеватая окраска вследствие гидратации влагой воздуха, но это не ухудшит качества продукта, который предназначен для растворения в воде. Однако, во избежание слеживания, упаковка должна быть герметичной.
Очистка сточных вод, сбрасываемых в водоемы из производств медного купороса и других медных солей, от ионов меди может быть осуществлена на 70 - 90 % с помощью сульфата алюминия. Выделяющаяся при гидролизе сульфата алюминия гидроокись алюминия адсорбирует ионы меди.
3.4 Получение медного купороса электролизом. Технология 7-9
Суть метода - электрохимическое окисление меди с растворением ее в серной кислоте. При проведении электролиза с растворимым медным анодом в растворе любой соли щелочного металла получающаяся на аноде медная соль, реагируя с образующейся на катоде щелочью, дает гидроксид меди с одновременной регенерацией электролита.
Можно получить электролизом инепосредственно раствор медного купороса, осуществляя процесс в ванне, в которой анод, находящийся на дне ванны, состоит из спрессованных или сплавленных обрезков меди. Через полый катод, помещенный сверху, подается серная кислота. Движение раствора от катода к аноду не допускается нежелательное в данном случае осаждение меди на катоде.
При проведении электролиза с растворимым медным анодом в растворе сульфатат натрия в ванне с диафрагмой можно одновременно получить медный купорос и гидроксид натрия. Купорос при этом легко может быть отделен от сульфатат натрия.
Медь может быть извлечена из разбавленных растворов цементацией и слабой аммиачной водой. При этом образуется осадок Cu(OH) 2 * CuSO 4 который после отделения от раствора можно растворить в серной кислоте с получением купороса.
3.5 Технология получения медного купороса из электролита цехов электрорафинирования меди (6)
В производстве медного купороса в качестве основного сырья используется раствор цеха электрорафинирования меди и медные гранулы.
Производство медного купороса включает в себе следующие последовательные стадии:
1. Получение насыщенных растворов и нейтрализация серной кислоты;
2. Выпарная вакуум-кристаллизация;
3. Разделение суспензии медного купороса и обработка кристаллов;
4. Затаривание и упаковка.
Первая стадия - получение насыщенных растворов сернокислой меди. Процесс производят путём связывания свободной серной кислоты, присутствующей в передаточном растворе цеха электрорафинирования меди и оборотных растворах купоросной производства, с медью в виде мелких гранул.
Основная реакция:
Cu + H 2 SO 4 + O 2 = CuSO 4 + H 2 O
На скорость процесса и качество получаемого купороса влияют:
Поверхность меди
Скорость окисления поверхности меди
Температура процесса растворения (растворение проводится при температуре 75-95 0 С)
Кислотность раствора.
Растворение меди осуществляется путём загрузки гранул в аппараты нейтрализации колонного типа, подогреваемые паром. Циркуляция осуществляется за счёт подачи в раствор сжатого воздуха. Образующаяся воздушно-жидкостная эмульсия вытесняется вверх по центральной трубе аппарата раствором, подводящимся по боковой трубе.
Скорость циркуляции (объемный расход) поддерживается на уровне от 15 до 30 м 3 /ч путем регулировки подачи воздуха.
Вторая стадия - выпарная вакуум-кристаллизация. Процесс организован в 3 стадии. Первые две производят медный купорос продукционный, а на третьей получают медный купорос некондиционный, который отправляется в начало процесса.
Исходный раствор из напорного бака самотёком подают в нижнюю часть вакуум-кристаллизатора. Под давлением напора перегретый маточный раствор, вытекая из сопла струйного насоса, подсасывает суспензию, циркулирующую в аппарате. Поступающий исходный раствор и образовавшаяся смесь поднимаются по центральной циркуляционной трубе вверх и на выходе из неё вскипают. Образовавшиеся кристаллы частично отводятся из вакуум-кристаллизатора. На процесс оказывают влияние температура и растворенные примеси.
В выпарном вакуум-кристаллизаторе поддерживается разряжение не менее 092-098 кПа. Суспензию из аппарата, при достижении концентрации 15-25%, сливают в бак-мешалку и закачивают в механические кристаллизаторы для сбора суспензии.
Третья стадия - разделение суспензии медного купороса и обработка кристаллов. Отделение кристаллов медного купороса от маточного раствора и промывку кристаллов производят на центрифугах, в основе работы которых лежит принцип фильтрации под действием центробежных сил. Для отделения маточного раствора II стадии кристаллизации от нерастворимых примесей дополнительно проводят фильтрацию раствора на рамном фильтр-прессе. Отфильтрованный маточный раствор направляют в бак маточного раствора, а кек после выгрузки фильтр-пресса - на площадку хранения медьсодержащих отходов.
Кристаллы с I и II стадий кристаллизации отправляют на сушку, а с III стадии - растворяют конденсатом в агитаторе при постоянном перемешивании и нагреве паром через рубашку агитатора.
Сушку кристаллов проводят горячим воздухом в барабанной сушилке, откуда купорос поступает на автоматическую линию упаковки и пакетирования или на узел затаривания готового продукта.
Для получения мелкодисперсного купороса от общей массы на двуситовой сортировке отделяют мелкую фракцию кристаллов.
Упаковку производят на автоматизированной линии в полиэтиленовые или бумажные мешки.
Список вариантов технологий, которые предлагаем мы и которые могут быть использованы, но нами не придуманы.
Выводы
На основании имеющихся данных можно сказать:
1. Температура является лимитирующим фактором при растворении меди. В холодных травителях, независимо от их природы, растворение идет с ничтожной скоростью
2. В травителе должно присутствовать 100-120 г/л медного купороса (безводный) для того, чтобы облегчить последующую кристаллизацию
3. Кристаллизация начинается в концентрированном растворе при присутствии там порошковой меди. Присутствие кристаллов купороса, введенных извне кристаллизацию не инициирует
4. Периодический барботаж необходим, т.к. с повышением концентрации купороса растворимость кислорода в нем падает и дополнительно тормозит реакцию. Кроме этого, барботаж делает осадок мелкодисперсным и не дает спекаться
5. Процесс тормозится после первого часа. Это связано с:
а. Остывание раствора, если не использовался нагрев
б. Расход растворенного воздуха и установление диффузионных ограничений по купоросу
в. Повышение концентрации купороса и уменьшение растворимости кислорода вследствие этого
6. Рафинированный и вторичный рафинированный порошок имеют высокую скорость растворения независимо от исходных параметров в рамках первого часа т.к:
а. Поверхность меди сильноокисленна. Ионы меди и железа катализируют только ОВ реакцию ионизации меди, а не обменные, которые преобладают в первом часе
б. Вторичная меди имеет более высокую скорость, чем первичная. т.к. в процессе ее оксидицзации принимали участие остатки травящего элеткролита. Т.е создавались условия с избытком окислителя - кислорода и легкостью его доступа вследствие того, что слой электролита имел пленочный характер, а не объемный. Кроме этого, сказывалось каталитическое действие ионов меди и железа.
В итоге выделим основные принципы процесса:
Максимальный нагрев, барботаж, введение оксидизатора, использование травителя с высоким исходным содержанием купороса и введением ионов железа.
Техинструкция
Первая партия шлама загружается в реактор на одни сутки. В течение смены используется нагрев и барботаж. Реактор должен быть снабжен полной и толстой термоизоляцией и крышкой с клапаном для стравливания лишнего воздуха.
После того, как первая партия прошла суточную реакцию она выгружается, раствору дается стечь и весь порошок отправляется в оксидизатор на воздух, представляющий собой емкость в теплом и влажном месте, где происходит усиленное окисление меди
В это время загружается вторая партия в этот же раствор. Раствор должен быть прогрет до наиболее высокой температуры, доступной технологически. Далее операции повторяются до насыщения раствора.
Насыщенный горячий раствор должен быть слит в кристаллизатор до конца смены, чтобы по остывании его не началось выпадение кристаллов. Не допускается оставлять порошок в насыщенном растворе по этой же причине
Кристаллизатор - это емкость, в которую подведены змеевики с холодной водой и внутрь которого загружены соты - т.е параллельно расположенные сетки Рабица.
Маточный раствор анализируется, корректируется по купоросу и кислоте и идет обратно.
В случае необходимости вывода маточного раствора из обращения он может быть нейтрализован цинковыми анодами или цинковой пылью, либо железными опилками. При этом следует учитывать наличие в нем железа.
Тихонова Дарья
Кристаллы окружают нас повсюду. Мы живём на поверхности твёрдого тела – земного шара, сооружениях, построенных из твёрдых тел, - домах. Наше тело, хотя и содержит приблизительно 65% воды (мозг – 80%) , тоже твёрдое. Знать свойства твёрдых тел жизненно необходимо!
Актуальность работы заключается в том, чтобы находить захватывающие рядом. То, что можно пронаблюдать, изучить и понять. Это ведь так интересно, занимательно и любопытно. Так как я буду выращивать кристалл соли, я прослежу и опишу целый процесс становления тела, определённой геометрической формы.
Цели работы:
1. Изучить строение и физические свойства кристалла медного купороса;
2. Выращивание кристаллов и наблюдение за процессом их роста;
3. Установить зависимость роста кристаллов от температуры, концентрации раствора, рода веществ;
Задачи:
1. Собрать материал о кристаллах, их свойствах и применении, используя различные источники информации, в том числе Интернет;
2. Провести опыты по выращиванию кристаллов медного купороса;
3. Выбрать способ, приемлемый для выращивания кристаллов в домашних условиях;
4. Изучить условия образования кристаллов, их формы, цвета;
5. Проанализировать полученные результаты.
Скачать:
Предварительный просмотр:
Муниципальное бюджетное общеобразовательное учреждения
«Центр детского (юношеского) технического творчества»
Городского округа г. Салават Республики Башкортостан
Выращивание и изучение условия
образования кристаллов медного купороса
Исследовательская работа по химии
Выполнила: Тихонова Дарья Александровна
Руководитель: Туманова Ольга Михайловна, педагог ДО направления «Прикладная химия»
г. Салават, 2013
Введение………………………………………………………………. | ||
Основные сведения о моно- и поликристаллах…………………….. | ||
Методика выращивания моно- и поликристаллов………………… | ||
Анализ роста монокристалла медного купороса………………….. | ||
Задача о концентрации раствора медного купороса при выращивании монокристалла……………………………………………………. | ||
Выводы………………………………………………………………… | ||
Литература…………………………………………………………….. | ||
Приложения…………………………………………………………… |
Введение
Кристаллы окружают нас повсюду. Мы живём на поверхности твёрдого тела – земного шара, сооружениях, построенных из твёрдых тел, - домах. Наше тело, хотя и содержит приблизительно 65% воды (мозг – 80%) , тоже твёрдое. Знать свойства твёрдых тел жизненно необходимо!
Актуальность работы заключается в том, чтобы находить захватывающие рядом. То, что можно пронаблюдать, изучить и понять. Это ведь так интересно, занимательно и любопытно. Так как я буду выращивать кристалл соли, я прослежу и опишу целый процесс становления тела, определённой геометрической формы.
Цели работы:
- Изучить строение и физические свойства кристалла медного купороса;
- Выращивание кристаллов и наблюдение за процессом их роста;
- Установить зависимость роста кристаллов от температуры, концентрации раствора, рода веществ;
Задачи:
- Собрать материал о кристаллах, их свойствах и применении, используя различные источники информации, в том числе Интернет;
- Провести опыты по выращиванию кристаллов медного купороса;
- Выбрать способ, приемлемый для выращивания кристаллов в домашних условиях;
- Изучить условия образования кристаллов, их формы, цвета;
- Проанализировать полученные результаты.
Основные сведения о моно- и поликристаллах
Если рассматривать при помощи лупы или микроскопа крупинки сахара, соли, медного купороса, то можно заметить, что они ограничены плоскими, как бы шлифованными гранями. Наличие таких естественных граней является признаком нахождения вещества в кристаллическом состоянии.
Кристалл (от греческого слова crystals–буквально: лёд.) – называется тело определённой геометрической формы, ограниченное естественными плоскими гранями.
Монокристаллы и поликристаллические тела
Тело, представляющее собой один кристалл, называется монокристаллом.
Монокристалл - отдельный однородный кристалл, имеющий непрерывную кристаллическую решётку и иногда имеющий анизотропию физических свойств. Внешняя форма монокристалла обусловлена его атомно-кристаллической решёткой и условиями (в основном скоростью и однородностью) кристаллизации. Медленно выращенный монокристалл почти всегда приобретает хорошо выраженную естественную огранку, в неравновесных условиях (средняя скорость роста) кристаллизации огранка проявляется слабо.
Поликристалл - агрегат мелких кристаллов какого-либо вещества, иногда называемых из-за неправильной формы кристаллитами или кристаллическими зёрнами. Многие материалы естественного и искусственного происхождения (минералы, металлы, сплавы, керамики и т. д.) являются поликристаллами.
Основные свойства кристаллов | ||
Форма и размер кристаллов | Кристаллы различных веществ имеют разнообразную форму. Размеры кристаллов различны. Одни кристаллы крупны и легко различимы невооруженным глазом, другие же настолько малы, что могут быть рассмотрены только в микроскоп. Размеры кристаллов поликристаллического типа могут с течением времени изменяться. Так, мелкие кристаллы железа и стали переходят в крупные кристаллы. Этот переход ускоряется при ударах и сотрясениях. Он постоянно происходит в железнодорожных рельсах, вагонных осях, стальных мостах, отчего прочность этих сооружений с течением времени уменьшается. |
|
Полиморфизм | Очень многие тела одинакового химического состава в кристаллическом состоянии в зависимости от условий могут существовать в двух или более разновидностях (модификациях). Это свойство называется полиморфизмом (многоформностью). У льда, например, известно до десяти различных модификаций, которые получают в лабораториях. В природе же встречается только один вид. |
|
Анизотропия кристаллов | Существенным свойством монокристалла является анизотропия (От греческих слов anisos - неравный, tropos - поворот, направление.) - неодинаковость его свойств (механических, тепловых, электрических и т. д.) по различным направлениям. Например, если кристаллы поваренной соли, имеющие кубическую форму, раскалывать, то мелкие осколки будут иметь преимущественно форму прямоугольных параллелепипедов. Это значит, что в направлениях, параллельных граням, прочность кристалла поваренной соли гораздо меньше, чем в диагональных и других направлениях. |
|
Изотропность кристаллов | Поликристаллические тела изотропны (От греческих слов isos - равный, tropos - поворот, направление.), т.е. обнаруживают одинаковые свойства по разным направлениям. Это объясняется тем, что кристаллики, из которых состоит поликристаллическое тело, ориентированы друг по отношению к другу хаотически. В результате ни одно из направлений не отличается. |
|
Дефекты в кристаллах | Описывая строение кристаллов, мы пользовались идеальными моделями. Отличие реальных кристаллов от идеальных кристаллов состоит в том, что реальные кристаллы не обладают правильной кристаллической решеткой. В них всегда встречаются нарушения строгой периодичности в расположении атомов. Эти нарушения называют дефектами в кристаллах. Дефекты образуются в процессе роста кристаллов под влиянием теплового движения молекул, механических воздействий, облучения потоками частиц, из-за наличия примесей. |
Сульфа́тме́ди(II) (медь серноки́слая) - неорганическое бинарное соединение, медная соль серной кислоты с формулой CuSO 4 . Нелетучее, не имеет запаха. Безводное вещество бесцветное, непрозрачное, очень гигроскопичное. Кристаллогидраты - прозрачные негигроскопичные кристаллы различных оттенков синего с горьковато-металлическим вкусом, на воздухе постепенно выветриваются (теряют кристаллизационную воду). Сульфат меди(II) хорошо растворим в воде. Из водных растворов кристаллизуется голубой пентагидрат CuSO4·5H2O - медный купоро́с.
Основные свойства сульфата меди(II) | ||
Термическое воздействие | При нагревании пентагидрат последовательно отщепляет две молекулы воды, переходя в тригидрат CuSO4·3H2O (этот процесс, выветривание, медленно идёт и при более низких температурах [в т.ч. при 20-25 °С]), затем в моногидрат (при 110 °С) CuSO4·H2O, и выше 258 °C образуется безводная соль. Выше 650 °C становится интенсивным пиролиз безводного сульфата по реакции: |
|
Растворимость | Растворимость сульфата меди(II) по мере роста температуры проходит через плоский максимум, в течение которого растворимость соли почти не меняется (в интервале 80-200 °C). Как и все соли, образованные ионами слабого основания и сильной кислоты, сульфат меди(II) гидролизуется, (степень гидролиза в 0,01М растворе при 15 °C составляет 0,05 %) и даёт кислую среду. Константа диссоциации составляет 5·10−3. |
|
Токсикологические данные | Сульфат меди (II) относят к классу опасности 1 (малоопасное вещество), как вещество, содержащее сульфат-ион. С другой же стороны, на стограммовой упаковке сульфата меди, поступающей в розничную продажу, указан класс опасности 2 (высокоопасное вещество). Смертельная доза медного купороса составляет от 8 до 30 грамм для взрослого человека. Летальная доза зависит от состояния здоровья человека, от его массы, от иммунитета именно к данному веществу и от других факторов. |
Методика выращивания моно- и поликристаллов
Безопасность.
При обращении с сульфатом меди (II) в бытовых условиях стоит быть очень осторожным. При приготовлении растворов желательно использовать резиновые или одноразовые полиэтиленовые перчатки, очки, резиновые сапоги и также настоятельно рекомендуется использовать респиратор. Ни в коем случае не использовать пищевую посуду. Приготовление раствора и использование медного купороса стоит производить в отсутствие детей и животных. Во время использования нельзя пить, курить, принимать пищу. После работы лицо и руки вымыть с мылом, прополоскать рот.
Хранить в сухом прохладном месте при температуре от -30 до +30, отдельно от лекарств, пищевых продуктов и кормов для животных, в недоступном для детей и животных месте. Запрещается хранение вещества в повреждённой упаковке.
Методика выращивания монокристаллов
- Приготовим насыщенный раствор соли - медного купороса. Насыщенным называется раствор, который находится в равновесии с нерастворенным веществом (твердым, жидким или газообразным). Следовательно, насыщенный раствор содержит максимальное количество вещества, которое может раствориться при данной температуре. Чтобы приготовить насыщенный раствор медного купороса, нужно рассчитать, сколько потребуется взять соли. Растворимость медного купороса при 20°С составляет 35.6 г в 100 г воды. Возьмём 200 мл воды, значит необходимо 35.6·200/100= 71.2 г CuSO 4 · 5H 2 O. С ростом температуры растворимость сульфата меди сначала увеличивается, потом почти перестает зависеть от температуры. Поэтому, чтобы исключить влияние колебаний, температуры в лаборатории, точности взвешивания и других факторов берём количество медного купороса большее расчетного - 100 г. Зальём соль водой и время от времени перемешиваем.
- Когда растворение медного купороса прекратится, и наступит равновесие, профильтруем раствор через неплотную фильтровальную бумагу или вату.
- Насыщенный раствор перельём в другую колбу.
- Выберем крупный и хорошо сформированный кристаллик, который послужит нам затравкой.
5. Привяжем его к нитке и опустим в колбу так, чтобы он не касался стенок сосуда.
6. Накроем стакан марлей - для защиты от пыли.
7. Покроем кристалл лаком.
8. Наблюдаем за ростом кристалла.
Через несколько дней рост кристалла будет виден визуально, он вырос длиной около 2 см.За неделю вырос кристалл длинной в 3,5 см, за две недели - 5 см, за три – 7см.
Когда в стакане образовывался осадок мелких кристалликов - я переливала раствор в чистую колбу и переносила в него мой кристалл. В ходе моего эксперимента такую процедуру я проделывала через день. Со временем на нитке тоже образуются мелкие кристаллики, которые начинают расти. Избежать этого сложно, можно разве что поднять кристалл повыше, чтобы меньший отрезок нитки контактировал с раствором. Во время эксперимента возникла идея использовать вместо хлопчатобумажной нитки тонкую медную проволочку. К сожалению, на воздухе кристаллы медного купороса теряют часть своей воды, при этом происходит их выветривание (разрушение). Чтобы кристаллы медного купороса сохранились дольше, покроем его лаком и поместим их в плотно закрытую банку.
Выращивание кристаллов потребовал труда и много терпения, но результат очень приятно нас удивил!
Методика выращивание поликристалла
В колбу наливаем 200мл. воды, добавляем туда 100г. медного купороса, хорошо размешиваем и переливаем раствор в стакан. Затем нагреваем раствор до 60 градусов по цельсию, наблюдаем, что медный купорос практически растворился. После этого сразу помещаем раствор в песок, для лучшей изоляции и удержания температуры, вносим в него затравку-кристаллик сульфата меди, привязанный к нитке.
Наследующий день мы видим образования поликристалла, по форме напоминавшего елочку.
Анализ роста монокристаллов за неделю
(Все три кристалла я растила по одной методике, но некоторые условия я меняла, например для первого кристалла я через день делала новый насыщенный раствор, нагревала до 60 о С и фильтровала его.)
1-кристалл.
2-кристалл (Для второго кристалла я взяла дистиллированную воду, но не нагревала, сделала насыщенный раствор, и в течение всей недели я не меняла этого раствора, а только насыщала его)
1 График зависимости изменений одной из граней кристалла от времени
Задача о концентрации раствора медного купороса при
выращивание монокристалла
Определите массовую долю медного купороса в растворе, полученном при растворении 100 г. медного купороса в 200 г. воды.
Решение:
Для начала нам надо найти массу раствора, она ровна сумме масс медного купороса и воды, то есть 300г. Затем находим массовую долю CuSO 4 в растворе, она ровна отношению массы вещества к массе раствора и чтобы найтисколько это в процентах умножаем это число на 100%. m(р-ра)=m(CuSO 4 )+m(H 2 O) m(р-ра)=100 г.+200 г.=300г. w(CuSO 4 )=(m в-ва / m р-ра )* 100% w(CuSO 4 )=(100 г./ 300 г.) * 100% = 33,(3) % Ответ: w(CuSO 4 ) = 33,(3) % |
Выводы
- Любая примесь в растворе может стать включением в кристалле или быть источником в дефекте. В итоге вместо монокристалла появятся «химеры», состоящие из наростов и искажений.
- Реальные кристаллы не обладают правильной кристаллической решёткой. В них всегда встречаются нарушения строгой периодичности в расположении атомов.
- Физические свойства кристаллов зависят от их строения – пространственной кристаллической решётки.
- Скорость роста кристаллов зависит от концентрации, насыщенности раствора и наличия инородных веществ. Чем больше концентрация, насыщенность вещества, и чем меньше наличие инородных веществ, тем быстрее происходит рост кристаллов.
- Монокристалл медного купороса можно вырастить за неделю.
- Поликристалл медного купороса можно вырастить за сутки.
- Кристаллы человек использует везде!
Медный купорос - вещество, которое благодаря красивому ярко-синему цвету идеально подходит для выращивания кристаллов. Их можно подарить своим близким или использовать в качестве элемента декора. В любом случае они никого не оставят равнодушным, а процесс изготовления может стать по-настоящему увлекательным. Итак, как же вырастить кристалл из медного купороса?
Подготовительные мероприятия
Медный купорос можно приобрести практически в любом хозяйственном магазине. Он активно применяется в сельском хозяйстве для борьбы с вредителями. Однако не следует забывать о том, что это вещество является токсичным. При работе с медным купоросом в домашних условиях обязательно используйте резиновые перчатки и не допускайте его попадания в пищевод и на слизистые оболочки. По окончании работ тщательно мойте руки в проточной воде.
Из медного купороса можно вырастить настоящее чудо, однако в процесе изготовления не забывайте о технике безопасности
Для того чтобы сделать кристалл, вам понадобятся:
- вода - если есть возможность, используйте дистиллированную или в крайнем случае кипячёную. Сырая вода из-под крана категорически не подходит из-за содержания в ней хлоридов, которые вступят в реакцию с раствором и ухудшат его качество ;
- медный купорос;
- стакан;
- проволока;
- нить из шерсти - проследите, чтобы она была тонкой. Можно использовать длинный волос. Кристаллы сульфата меди прозрачны, и нитка не должна просматриваться сквозь них.
Помещая затравку в ёмкость с раствором, следите, чтобы она не соприкасалась со стенками или дном сосуда. Это может нарушить процесс роста кристалла и его структуру.
Инструкция по выращиванию кристалла
Существует две технологии выращивания кристаллов из медного купороса.
- Если вы не хотите долго ждать, то можете воспользоваться быстрым способом. По времени это займёт около недели, а в результате вы получите множество небольших кристаллов, закреплённых один на другом, будто колония ракушек-мидий.
- Второй метод более продолжительный. Он поможет вам вырастить крупный цельный кристалл, похожий на драгоценный камень.
Но оба они основаны на работе с насыщенным раствором вещества.
Обратите внимание! Чем выше температура воды, тем быстрее в ней растворяется медный купорос. Но при достижении жидкостью +80С° последующее нагревание никак не влияет на растворимость солей.
Быстрый способ
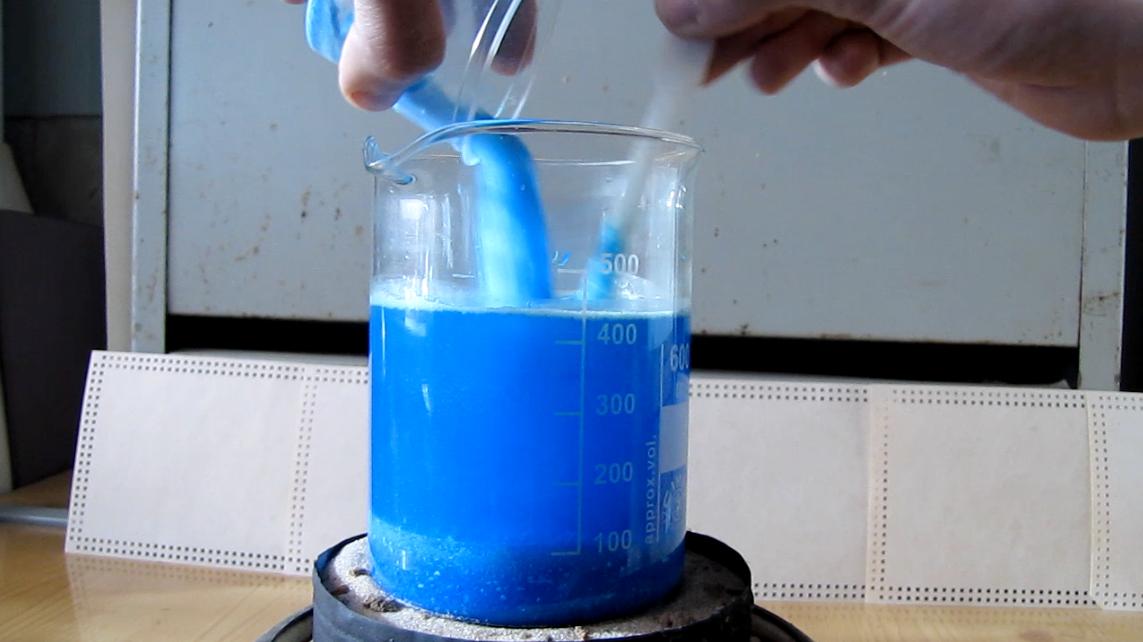
Выращивая кристаллы сульфата меди быстрым способом, вы можете не беспокоиться о затравке: можно и вовсе обойтись без неё. Осадок легко закрепится на нитке.
Второй способ
В этом случае вы сможете вырастить крупный кристалл сульфата меди, однако это займёт гораздо больше времени. Кроме того, в отличие от первого способа, выбор затравки принципиально важен. К тому же вам придётся следить, чтобы к ней не прилипали мелкие кристаллики.
Чем крупнее и ровнее будет выбранный из общей массы кристаллик медного купороса, тем красивее получится конечное изделие.
Вам понадобятся 200 г тёплой воды и около 110 г медного купороса.
Инструкция по изготовлению:
- смешайте купорос и воду в подходящей посуде (стакане или банке), оставьте на сутки. Периодически помешивайте: активное вещество должно полностью раствориться. После этого отфильтруйте раствор через вату или специальную фильтровальную бумагу. Оставшийся на поверхности фильтра осадок можно высушить и использовать снова при необходимости;
- полученный раствор залейте в чистую ёмкость;
- выберите кристаллик для затравки, привяжите его к нити (волосу). Второй конец нитки закрепите на палочке, положите её горизонтально на ёмкость. Затравка должна опуститься в раствор в строго вертикальном положении. Посуду накройте кусочком ткани, чтобы внутрь не попадала пыль;
Подходящий по размеру для затравки кристаллик медного купороса
- спустя несколько дней вы заметите, что кристалл растёт. Через неделю он достигнет 1 см, а со временем увеличится ещё больше;
Обязательно накройте ёмкость с раствором и затравкой кусочком ткани
Во время работы вы можете столкнуться с некоторыми трудностями. Их несложно преодолеть, придерживаясь простых правил.
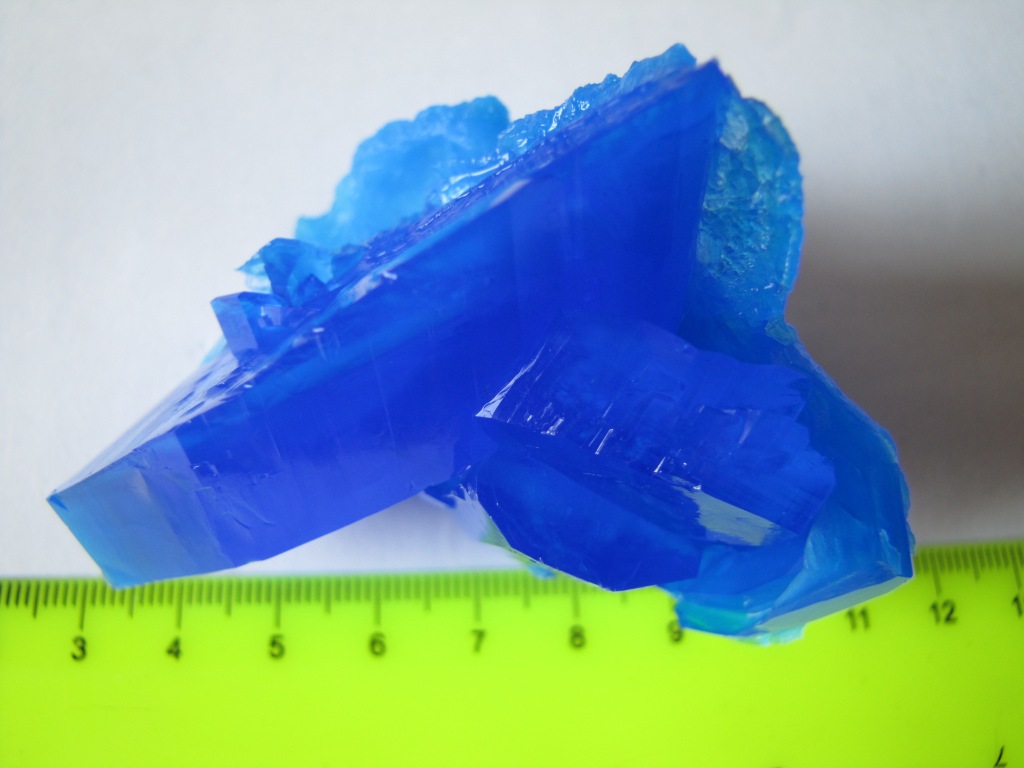
При воздействии воздуха кристалл медного купороса теряет часть влаги, выветривается и со временем разрушается. Чтобы избежать этого, храните его в плотно закрытой ёмкости в прохладном месте. Специалисты советуют покрывать его бесцветным лаком, - это создаст надёжную защитную плёнку.
Курсовая работа
По общей химической технологии
Производство медного купороса из медного лома
Введение
Характеристика медного купороса
Способы производства медного купороса
Башенный способ получения медного купороса
1 Сырье для получения медного купороса
2 Физико-химические характеристики основных стадий процесса
2.1Теоретические основы процесса
2.2 Очистка и грануляция медного лома
2.3 Растворение меди в серной кислоте (натравка)
2.4 Кристаллизация медного купороса
3 Описание технологической схемы
4. Характеристика используемых химических реакторов
5 Характеристика отходов, проблемы их обезвреживания и полезного использования
Расчетная часть
Области применения теоретических и практических расчетных коэффициентов на основе расчета материального и теплового балансов
Заключение
Библиографический список
Введение
Среди неорганических веществ медный купорос является одним из наиболее эффективных препаратов для борьбы с болезнями плодовых деревьев, виноградников и других растений. Чаще всего его используют в смеси с известью и другими наполнителями.
Медный купорос получают разными способами, но самый основной - башенный способ (получение из медного лома), главным сырьем которого является медь и серная кислота.
Медный купорос является важнейшей солью меди и находит широкое применение в промышленности и сельском хозяйстве. Он служит исходным материалом для производства различных солей меди.
В сельском хозяйстве он применяется для предохранения растений от вредителей и некоторых заболеваний и является составной частью ядохимикатов: бордосской жидкости и препарата АБ.
Смесь водного раствора медного купороса с известью (1 кг CuSO4*5H2O и 0,75 кг свежегашеной извести на 100л воды) известна под названием бордосской жидкости, представляющей собой суспензию основного сульфата меди 3Cu(OH)2*CuSO4 и CaSO4. Основная соль полностью разрушается в щелочной среде. Для образования суспензии стойкой основной соли молярное отношение CuO: СaO должно быть равным 1:0,75, а весовое отношение 1:0,53 или весовое отношение CuO: Ca(OH)2, равным 1:0,7. В связи с частичной карбонизацией извести при хранении и перевозках, при изготовлении бордосской жидкости принимают весовое отношение медного купороса к извести 1:0,75.
При смешении раствора медного купороса с раствором соды получается бургундская жидкость - суспензия основного карбоната меди 3Cu(OH)2*2CuCO3. Преимущество ее перед бордосской жидкостью является хорошая прилипаемость и отсутствие комков, забивающих распылительные устройства. Медный купорос применяют для изготовления парижской зелени. Также его используют в гальванических элементах в качестве электролита, в гальванотехнике, для консервирования дерева, для изготовления некоторых минеральных красок, в производстве искусственного волокна и при обогащении руд.
1. Характеристика медного купороса
Пятиводный кристаллогидрат сульфата меди CuSO4·5H2O (хальконтит), называемый медным (синим) купоросом, образует асимметричные ярко- синие кристаллы триклиноэдрической системы с плотностью 2,29г/см3. Как и другие соли меди, медный купорос ядовит. При нагревании он плавится (110°) с потерей части кристаллизационной воды и переходит в трехводный (голубого цвета) и одноводный (белого цвета) сульфат меди. Выше 258° образуется безводный сульфат меди белого цвета, сильно гидроскопичный. При 819 - 860° CuSO4 разлагается по реакции:
CuSO4 = SO3+ CuO·CuSO4
а при 897 - 934° полностью диссоциирует на CuO и SO3. При обычной температуре кристаллы медного купороса на воздухе не выветриваются.
Насыщенный водный раствор медного купороса содержит при 0°- 12,9%, при 20°- 17,4 %, при 55°- 29,9 %, при 100° - 42,4 % CuSO4. Безвариантное равновесие CuSO4·5H2O + CuSO4·3H2O + раствор + пар существует при 96° и 540 мм рт. ст. Растворимость медного купороса в присутствии свободной серной кислоты понижается; в растворе образуется комплексный ион 2-. При повышенных температурах из кислых раствор кристаллизуется CuSO4·3H2O.
В системе CuSO4 - FeSO4- H2SO4- H2O в интервале 27 - 97° и диапазоне концентраций H2SO4 от 7 до 37 г/л и FeSO4 (в вес.%):0 - 2,6, 2,7 - 4,7 и 8,5 - 9,2. С повышением температуры растворимость твердого раствора уменьшается, а содержание FeSO4 в нем возрастает. В растворах с увеличенной кислотностью повышается содержание FeSO4 в кристаллах, но понижается их растворимость.
Требования к качеству медного купороса представлены в таблице 1: Таблица 1. Состав медного купороса (в %)
По ГОСТ 5.1688-72 (со знаком качества)Марка АМарка БСорт ΙСорт ΙΙСорт ΙΙΙсушеныйНе сушеныйсушеныйНе сушеныйCuSO4·5H2O не менее99,095,09894949296В пересчете на Cu,не менее25,1924,1724,923,923,923,4-Железо Fe, не более0,0350,030,060,030,10,30,02Свободная H2SO40,250,250,250,250,250,250,25Нерастворимый в воде остаток, не более0,050,040,10,050,040,10,05Мышьяк As, не более0,0050,0010,0150,0150,0150,030,015
Медный купорос Ι и ΙΙ сортов марки А предназначаются для сельского хозяйства, ΙΙΙ сорта - для обогатительных предприятий, марки Б - для предприятий искусственного волокна. Тарой для медного купороса служат деревянные бочки, фанерные барабаны или ящики с бумажными или полиэтиленовыми вкладышами, а также двойные полиэтиленовые и джутовые мешки и четырехслойные бумажные мешки.
2. Способы производства медного купороса
Различают, главным образом, по видам применяемого сырья: .Из медного лома и отходов меди (стружки, высечки, проволоки, опилок и т.д.) с окислением меди кислородом воздуха, электролизом или раствором хлорной меди;
.Из окиси меди, получаемой из белого матта;
.Из окиси меди и сернистого газа;
.Из окисленных медных руд, содержащих незначительное количество меди, переработка которых на металлическую медь плавкой в печах является не экономичной;
.Из колчеданных огарков и других отходов;
.Из отбросных электролитных растворов медеэлектролитных заводов.
Наиболее промышленное значение имеет башенный способ производства медного купороса, использующий медный лом и отходы металлообрабатывающих заводов. Основные стадии башенного способа следующие: ) гранулирование меди; ) Растворение меди в серной кислоте (натравка); ) кристаллизация медного купороса. При башенном способе производства медь в виде медного лома и других отходов переплавляют в печах для очистки от различных примесей. Расплавленную медь выливают тонкой струей в холодную воду для получения ее в виде полых шариков (гранул), обладающих большой поверхностью, вследствие чего ускоряется растворение меди в серной кислоте. Для растворения гранулы загружают в полую башню, через которую пропускают воздух и обрабатывают слабым раствором медного купороса, содержащим свободную серную кислоту. При этом получается концентрированный раствор медного купороса, из которого при охлаждении выделятся кристаллический медный купорос. За рубежом основными производителями медного купороса являются Франция и Италия, где в качестве сырья используют главным образом медный лом и окисленные руды. В отличие от этого в США используют в основном электролитные щелоки, из которых производят больше половины всех солей препаратов меди.
3. Башенный способ производства медного купороса
.1 Сырье для получения медного купороса
Основным сырьем для получения медного купороса служат серная кислота и металлическая медь. Серная кислота должна употреблять требованиям ГОСТ 2184 - 59 (таблица 2).
Таблица 2. Состав различных сортов серной кислоты (в %)
Составные частиКонтактная H2SO4Башенная H2SO4Регенерированная H2SO4техническаяТехническая улучшеннаяолеумМоногидрат серной кислоты не менее92,592,5 - 94,0_7591Свободный серный ангидрид(SO3), не менее__18,5__Окислы азота (в пересчете на N2O3), не менее_0,0001_0,030,01Прокаленный остаток, не более_0,040,15_0,2Железо, не более_0,015___Мышьяк, не более_0,0001___
Металлическую медь употребляют в виде: ) сортного лома и отходов меди; ) низкокачественный лом и отходы меди. Используемая медь должна соответствовать требованиям, предусмотренным ГОСТ 1639 - 48. В производстве медного купороса применяют: лом и кусковые отходы прокатной меди без полуды и пайки (куски меди, медные проводники, снарядные пояски, обрезки); лом прокатной меди, засоренной не более чем на 10% другими металлами и сплавами; медную стружку; лом и кусковые отходы луженой и паяной меди как не засоренной так и засоренной другими металлами.
3.2 Физико-химические характеристики основных стадий процесса
3.2.1 Теоретические основы процесса
В отсутствии окислителей, в частности кислорода воздуха, в разбавленной серной кислоте медь практически не растворяется. Она с достаточной скоростью растворяется в горячей концентрированной серной кислоте, но осуществлять этот процесс нерационально, так как при этом половина затрачиваемой кислоты восстанавливается до SO2, окисляя медь в окись меди, которая и растворяется в серной кислоте, образуя медный купорос. Схема этого процесса может быть выражена следующими уравнениями реакций:
Cu + H2SO4 = CuO + H2O + SO2+ H2SO4 = CuSO4 + H2O+ 2H2SO4 = CuSO4 + 2H2O + SO2
С целью экономии серной кислоты окисление меди производят кислородом воздуха одновременно с процессом «натравки», т.е. растворения в серной кислоте. Медный лом предварительно переплавляют для рафинирования (очистки от примесей Fe, Zn, Al, Pb и т.д.) и придания ему формы, удобной для растворения - пустотелых гранул, обладающих большой поверхностью, что ускоряет растворение в кислоте в 5-10 раз.
3.2.2 Очистка и грануляция медного лома
Для этого загрязненную медь расплавляют в пламенных печах и окисляют кислородом воздуха, содержащимся в печных газах. Большая часть примесей при этом окисляется и удаляется в виде шлака с поверхности расплавленной меди, а медь получается более чистой. Процесс очистки металла окислением входящих в него примесей кислородом воздуха при высокой температуре называется окислительной очисткой, или рафинированием. Чистая медь плавится при 1084°, а в присутствии примесей - при более низкой температуре. Примеси летучих металлов и окислов - металлический цинк, трехокиси мышьяка и сурьмы - удаляются при нагревании меди до ее расплавлении. При расплавлении медь окисляется до закиси меди, устойчивой выше 1100°. Закись меди накапливается на поверхности расплавленной меди в твердом (до 1200°) и в жидком (до 1235°) виде и частично растворяется в меди, а затем вступает во взаимодействие с примесями, например:
Cu2O + Fe = FeO + 2Cu
По мере расходования растворенной закиси меди новые ее количества переходят с поверхности в раствор, и медь подвергается дальнейшему окислению. Образующиеся окислы железа, магния, кальция и других металлов не растворимы в меди и переходят в шлак, всплывающий на поверхность металла. Вследствие взаимодействия закиси меди с некоторыми окислами (например, с окисью железа с образованием феррита меди) часть ее так же переходит в шлак и содержание в нем Cu2O достигает 30 - 40%.
После окисления, ошлакование примесей металлов и удаления шлака, температуру в печи немного снижают с целью окисления присутствующей в меди полусернистой меди:
Cu2S + 2Cu2O ↔ 6Cu + SO2
Эта реакция протекает бурно, и выделяющаяся двуокись серы увлекает брызги меди с образованием «медного дождя» («кипение» массы). В производстве медного купороса дальнейшая очистка не требуется, а присутствие в ней кислорода и двуокиси серы, необходимо для получения пористых и пузыристых гранул. Растворимость газов в расплавленной меди возрастает с повышением температуры. В твердой меди, нагретой даже до температуры плавления, растворимость газов не значительная. Процесс гранулирования с получение пузыристой и пористой меди основан на быстром выделении газов при внезапном охлаждении и затвердевании расплавленной меди. Это осуществляется выливанием ее тонкой струей в холодную воду. 3.2.3 Растворение меди в серной кислоте (натравка)
При взаимодействии гранул меди с разбавленным раствором серной кислоты, содержащий также сульфат меди, в присутствии воздуха, кислород воздуха растворяется в кислоте, диффундирует к поверхности меди и окисляет ее до закиси меди: 4Cu + O2 = 2Cu2O
Закись меди растворяется в серной кислоте:
Cu2O + H2SO4 = Cu2SO4 + H2O
Образующийся сульфат закиси меди легко окисляется в сульфат окиси меди:
2Cu2SO4 + 2H2SO4 + O2 = 4CuSO4 + 2H2O
Общая скорость процесса лимитируется наиболее медленной его стадией - окислением меди до закиси. Это объясняется малой растворимостью кислорода и медленной его диффузией к поверхности гранул меди. Процесс значительно ускоряется, когда в растворе уже присутствует медный купорос. В результате деполяризации
Cu + Cu2+ = 2Cu2+
4 восстанавливается медью до Cu2SO4, а затем Cu2SO4 вновь окисляется растворенным кислородом до CuSO4. Таким образом, медный купорос играет роль переносчика кислорода.
В присутствии металлической меди в растворе медного купороса может находиться лишь ничтожное количество одновалентной меди. Константа равновесия реакции Cu2+ + Cu ↔2Cu+ при 25° К = 2: = 0,62·10-6. В растворе, содержащим 50 г/л H2SO4 и 32 г/л Cu в виде CuSO4, имеется только ≈ 0,022 г/л одновалентной меди, т.е. меньше 0,1 % от общего ее количества.
Повышение температуры, как и в других случаях, ускоряет химические реакции, но вызывает уменьшение растворимости кислорода, что замедляет окисление. Поэтому в натравочной башне поддерживают температуру не выше 80 -85°. При этом при окислении меди используется приблизительно ¼ кислорода, поступающего в башню с воздухом, расход которого составляет 1000 нм3 на 1т медного купороса.
Растворимость кислорода уменьшается с ростом концентрации CuSO4 в растворе. Поэтому при увеличении концентрации CuSO4