Расчет сварных соединений внахлестку. Расчет сварных соединений
СТЫКОВОЕ СОЕДИНЕНИЕ С ПРЯМЫМ ШВОМ
(рис. 1, а).
Р 1 = [σ" p ]·L·S
,
то же при сжатии
Р 2 = [σ" сж ]·L·S
,
где,
При расчете прочности все виды подготовки кромок в стыковых соединениях принимают равноценными.
СТЫКОВОЕ СОЕДИНЕНИЕ С КОСЫМ ШВОМ
(рис. 1, б).
Допускаемая сила для соединения при растяжении
То же при сжатии
При β = 45° - соединение равнопрочно целому сечению.
НАХЛЕСТОЧНОЕ СОЕДИНЕНИЕ
(рис. 2).
Соединения выполняют угловым швом. В зависимости от напряжения шва относительно направления шва относительно направления действующих сил угловые швы называют лобовыми (см. рис. 2, а), фланговыми (см. рис. 2. б), косыми (см. рис. 2. в) и комбинированными (см. рис. 2, г).
Максимальную длину лобового и косого швов не ограничивают. Длину фланговых швов следует принимать не более 60К, где К - длина катета шва. Минимальная длина углового шва 30 мм; при меньшей длине дефекты в начале и в конце шва значительно снижают его прочность.
Минимальный катет углового шва К min принимают равным 3 мм, если толщина металла S >= 3 мм.
Допускаемая сила для соединения
где, [τ ср ] - допускаемое напряжение для сварного шва на срез;
К - катет шва;
L - весь периметр угловых швов;
- для лобовых швов L = l
; для фланговых L = 2l
1 ;
- для косых L = l
/sinβ;
- для комбинированных L = 2l
1 + l
.
СОЕДИНЕНИЕ НЕСИММЕТРИЧНЫХ ЭЛЕМЕНТОВ
(рис. 3).
Силы, передаваемые на швы 1 и 2, находят из уравнений статики
Необходимая длина швов
где,
К - катет шва.
Примечание: Допускается увеличение l 2 до размера l 1 .
ТАВРОВОЕ СОЕДИНЕНИЕ
Наиболее простое в технологическом отношении.
Р = 0,7 [τ" ср ] KL
,
где,
[τ" ср ] - допускаемое напряжение для сварного шва на срез;
К - катет шва, который не должен превышать 1,2S (S - наименьшая толщина свариваемых элементов).
Наиболее обеспечивающее лучшую передачу сил.
Допускаемая сила для растяжения
Р 1 = [σ" p ]·L·S
,
то же при сжатии
Р 2 = [σ" сж ]·L·S
,
где,
[σ" p ] и [σ" сж ] - допускаемые напряжения для сварного шва соответственно при растяжении и сжатии.
СОЕДИНЕНИЕ С НАКЛАДКАМИ
Сечение накладок, обеспечивающее равнопрочность целого сечения (см. рис. 6)
где,
F - сечение основного металла; [σ p ] - допускаемое напряжение при растяжении основного металла; [σ" p ] - допускаемое напряжение для сварного шва при растяжении.
Сечение накладки, обеспечивающее равнопрочность целого сечения (см. рис. 7):
где,
[τ" cp ] - допускаемое напряжение для сварного шва на срез.
СОЕДИНЕНИЕ С ПРОРЕЗЯМИ
Применяют лишь в случаях, когда угловые швы недостаточны для скрепления.
Рекомендуется a = 2S , l
= (10 ÷ 25)S.
Допускаемая сила, действующая на прорезь
Р = [τ" сp ]·L·S
,
где,
[τ" сp ] - допускаемое напряжение для сварного шва на срез.
СОЕДИНЕНИЕ ПРОБОЧНОЕ
Применяют в изделиях, не несущих силовых нагрузок. Пробочную сварку можно применять для соединения листов толщиной от 15 мм.
Если пробочные соединения подвергаются действию срезывающих сил, то напряжение
где,
d - диаметр пробки;
i - число пробок в соединении.
СОЕДИНЕНИЕ СТЫКОВОЕ
ПОД ДЕЙСТВИЕМ ИЗГИБАЮЩЕГО МОМЕНТА
При расчете прочности соединения (см. рис. 9), осуществленного стыковым швом, находящимся под действием изгибающего момента М и и продольной силы Р, условие прочности
где,
W = Sh²/6;
F = hS.
При расчете прочности соединения (см. рис. 10, а), осуществленного угловым швом, находящимся под действием изгибающего момента М и и продольной силы Р, расчетные касательные напряжения в шве
где,
W c = 0,7Kh²/6;
F c = 0,7Kh.
При расчете прочности соединений (см. рис. 10, б), состоящих из нескольких швов и работающих на изгиб, принимают (для приведенного графически случая), что изгибающий момент М и уравновешивается парой сил в горизонтальных швах и моментом защемления вертикального шва
Если момент М и и допускаемое напряжение τ заданы, то из полученного уравнения следует определить l
и K, задавшись остальными геометрическими параметрами.
ДОПУСКАЕМЫЕ НАПРЯЖЕНИЯ ДЛЯ СВАРНЫХ ШВОВ
Допускаемые напряжения (табл. 1 и 2) для сварных швов принимают в зависимости:
а) от допускаемых напряжений, принятых для основного металла;
б) от характера действующих нагрузок.
В конструкциях из стали Ст5, подвергающихся воздействию переменных или знакопеременных нагрузок, допускаемые напряжения для основного металла понижают, умножая на коэффициент
где,
σ min и σ max - соответственно минимальное и максимальное напряжения, взятые каждое со своим знаком.
1. Допускаемые напряжения для сварных швов
в машиностроительных конструкциях при постоянной нагрузке
2. Допускаемые напряжения в МПа
для металлоконструкций промышленных сооружений
(подкрановые балки, стропильные фермы и т. п.)
Марка стали | Учитываемые нагрузки | |||||
основные | основные и дополнительные | |||||
вызывающие напряжения | ||||||
растяжения, сжатия, изгиба | среза | смятия (торцового) | растяжения, сжатия, изгиба | среза | смятия (торцового) | |
Подкрановые балки, стропильные фермы и т.п. | ||||||
Ст2 Ст3 | 140 160 | 90 100 | 210 240 | 160 180 | 100 110 | 240 270 |
Металлоконструкции типа крановых ферм | ||||||
Ст0 и Ст2 Ст3 и Ст4 Ст5 Низколеги- рованная | 120 140 175 210 | 95 110 140 170 | 180 210 260 315 | 145 170 210 250 | 115 135 170 200 | 220 255 315 376 |
Для конструкций из низкоуглеродистых сталей при действии переменных нагрузок рекомендуется принимать коэффициент понижения допускаемых напряжений в основном металле
где,
ν - характеристика цикла, ν = Р min / P max ; Р min и P max соответственно наименьшая и наибольшая по абсолютной величине силы в рассматриваемом соединении, взятые каждая со своим знаком;
K s - эффективный коэффициент концентрации напряжений (табл. 3).
3. Эффективный коэффициент концентрации напряжения K s
Расчетное сечение основного металла | К s |
Вдали от сварных швов | 1,00 |
(металл обработан наждачным кругом) | 1,00 |
В месте перехода к стыковому или лобовому шву (металл обработан строганием) | 1,10 |
В месте перехода к стыковому шву без механической обработки последнего | 1,40 |
В месте перехода к лобовому шву без обработки последнего, но с плавным переходом при ручной сварке | 2,00 |
В месте перехода к лобовому шву при наличии выпуклого валика и небольшого подреза | 3,00 |
В месте перехода к продольным (фланговым) швам у концов последних | 3,00 |
ПРИМЕРЫ РАСЧЕТА ПРОЧНОСТИ СВАРНЫХ СОЕДИНЕНИЙ
Пример 1. Определить длину швов, прикрепляющих уголок 100x100x10 мм к косынке (рис. 11. а). Соединение конструируется равнопрочным целому элементу. Материал сталь Ст2. Электроды Э42.
В табл. 2 для стали Ст2 находим допускаемое напряжение [σ p ] = 140 МПа. Площадь профиля уголка 1920 мм² ("Уголки стальные горячекатаные равнополочные" ГОСТ 8509-93).
Расчетная сила в уголке
Р = 140x1920 = 268 800 Н
В данном случае допускаемое напряжение при срезе, согласно табл. 1, в сварном шве
[τ cp ] = 140x0,6 = 84 МПа .
Требуемая длина швов (при К =10 мм) в нахлесточном соединении согласно расчету к рис. 11а.
Длина лобового шва l = 100 мм: требуемая длина обоих фланговых швов l фл = 458-100 = 358 мм. Так как для данного уголка е 1 = 0,7l то длина шва 2 будет l 2 - 0,7x358 = 250 мм, длина шва 1 будет l 1 = 0,3x358 = 108 мм. Принимаем l 2 = 270 мм, l 1 = 130 мм.
Пример 2. Определить длину l швов, прикрепляющих швеллер №20а. нагруженный на конце моментом М = 2,4x10 7 Н·мм (рис. 11. б). Материал сталь Ст2. Электроды Э42.
В табл. 2 для стали Ст2 находим допускаемое напряжение [σ p ] = 140 МПа. Допускаемое напряжение при срезе, согласно табл. 1, в сварном шве
[τ" cp ] = 140x0,6 = 84 МПа .
Момент сопротивления сечения швеллера W = 1,67 x 10 5 мм³ (из ГОСТа)
Напряжение
σ = 2,4x10 7 / 1,67x10 5 = 144 МПа
Катет горизонтальных швов К 1 = 10 мм, вертикального К 2 = 7,5 мм. Из формулы 1 (см. выше) находим
Принимаем l = 200 мм. При этой длине шва напряжение при изгибе
Полученная величина меньше допускаемой [τ" cp ] = 84 МПа.
ЭЛЕКТРОДЫ
Размеры и общие технические требования на покрытые металлические электроды для ручной дуговой сварки сталей и наплавки поверхностных слоев из сталей и сплавов приведены в ГОСТ 9466-75 или кратко .
Электроды покрытые металлические для ручной дуговой сварки конструкционных и теплоустойчивых сталей (по ГОСТ 9467-75):
Электроды изготовляют следующих типов:
Э38, Э42, Э46 и Э50 - для сварки низкоуглеродистых и низколегированных конструкционных сталей с временным сопротивлением разрыву до 500 МПа:
Э42А, Э46А и Э50А - для сварки углеродистых и низколегированных конструкционных сталей с временным сопротивлением разрыву до 500 МПа, когда к металлу сварных швов предъявляют повышенные требования по пластичности и ударной вязкости;
Э55 и Э60 - для сварки углеродистых и низколегированных конструкционных сталей с временным сопротивлением разрыву св. 500 до 600 МПа;
Э70, Э85, Э100, Э125, Э150 - для сварки легированных конструкционных сталей повышенной и высокой прочности с временным сопротивлением разрыву свыше 600 МПа;
Э-09М, Э-09МХ, Э-09Х1М, Э-05Х2М, Э-09Х2МГ, Э-09Х1МФ, Э-10Х1М1НФБ, Э-10ХЗМ1БФ, Э-10Х5МФ - для сварки легированных теплоустойчивых сталей.
Механические свойства металла шва,
наплавленного металла и сварного соединения при нормальной температуре (по ГОСТ 9467-75)
Типы электродов | Металл шва или наплавленный металл | Сварное соединение, выполненное электродами диаметром менее 3 мм | |||
Относительное удлинение δ 5 , % | Ударная вязкость KCU, Дж/см² (кгс·м/см²) | Временное сопротивление разрыву σ в, МПа (кгс/мм²) | Угол загиба, градусы | ||
не менее | |||||
Э38 | 380 (38) | 14 | 28 (3) | 380 (38) | 60 |
Э42 | 420 (42) | 18 | 78 (8) | 420 (42) | 150 |
Э46 | 460 (46) | 18 | 78 (8) | 460(46) | 150 |
Э50 | 500 (50) | 16 | 69 (7) | 500 (50) | 120 |
Э42А | 420 (42) | 22 | 148 (15) | 420 (42) | 180 |
Э46А | 460 (46) | 22 | 138 (14) | 460 (46) | 180 |
Э50А | 500 (50) | 20 | 129 (13) | 500 (50) | 150 |
Э55 | 550 (55) | 20 | 118 (12) | 550 (55) | 150 |
Э60 | 600 (60) | 18 | 98 (10) | 600 (60) | 120 |
Э70 | 700 (70) | 14 | 59 (6) | - | - |
Э85 | 850 (85) | 12 | 49 (5) | - | - |
Э100 | 1000 (100) | 10 | 49 (5) | - | - |
Э125 | 1250 (125) | 8 | 38 (4) | - | - |
Э150 | 1500 (150) | 6 | 38 (4) | - | - |
ГОСТ 9467-75 предусматривает также типы электродов и механические свойства наплавленного металла или металла шва для легированных теплоустойчивых сталей.
Электроды покрытые металлические для ручной дуговой наплавки
поверхностных слоев с особыми свойствами (по ГОСТ 10051-75)
Тип | Марка | Твердость без термообработки после наплавки HRC |
Область применения |
Э-10Г2 Э-11Г3 Э-12Г4 Э-15Г5 Э-30Г2ХМ | ОЗН-250У O3H-300У ОЗН-350У ОЗН-400У НР-70 | 22,0-30,0 29,5-37,0 36,5-42,0 41,5-45,5 32,5-42,5 | Наплавка деталей, работающих в условиях интенсивных ударных нагрузок (осей, валов автосцепок, железнодорожных крестовин, рельсов и др.) |
Э-65Х11Н3 Э-65Х25Г13Н3 | ОМГ-Н ЦНИИН-4 | 27,0-35,0 25,0-37,0 | Наплавка изношенных деталей из высокомарганцовистых сталей типов Г13 Г13Л |
Э-95Х7Г5С Э-30Х5В2Г2СМ | 12АН/ЛИВТ ТКЗ-Н | 27,0-34,0 51,0-61,0 | Наплавка деталей, работающих в условиях интенсивных ударных нагрузок с абразивным изнашиванием |
Э-80Х4С Э-320Х23С2ГТР Э-320Х25С2ГР Э-350Х26Г2Р2СТ | 13КН/ЛИВТ Т-620 Т-590 Х-5 | 57,0-63,0 56,0-63,0 58,0-64,0 59,0-64,0 | Наплавка деталей, работающих в условиях преимущественно абразивного изнашивания |
Э-300Х28Н4С4 Э-225Х10Г10С Э-110Х14В13Ф2 Э-175Б8Х6СТ | ЦС-1 ЦН-11 ВСН-6 ЦН-16 | 49,0-55,5 41,5-51,5 51,0-56,5 53,0-58,5 | Наплавка деталей, работающих в условиях интенсивного абразивного изнашивания ударными нагрузками |
ГОСТ предусматривает также и другие химический состав, типы и марки электродов.
Сварочные материалы, применяемые для сварки стальных конструкций, должны обеспечивать механические свойства металла шва и сварного соединения (предел прочности, предел текучести, относительное удлинение, угол загиба, ударную вязкость) не менее нижнего предела свойств основного металла конструкции.
Свариваемые материалы и применяемые электроды:
СтЗкп, СтЗкп, СтЗпс, Сталь 08кп, Сталь 10 - Э42, Э42А, Э46;
- Сталь 20 - Э42;
- Сталь 25Л - Э46;
- Сталь 35Л, Сталь 35, Сталь 45, Ст5кп, Ст5пс - Э50А;
- Сталь 20Х, Сталь 40X - Э85;
- Сталь 18ХГТ, Сталь 30ХГСА - Э100;
- АД1, АД1М, АМг6 - Присадочные прутки.
Подробную классификацию покрытых электродов и область применения смотри .
Сварные соединения внахлестку выполняют угловым (валиковым) швом. Угловые швы соединения внахлестку могут воспринимать произвольно направленные силы и моменты.
Соединения обычно воспринимают нагрузку в плоскости стыка.
Угловые швы соединений внахлестку могут иметь сечения: нормальные (треугольные), выпуклые и вогнутые. Наиболее целесообразный с точки зрения снижения концентрации напряжений и в условиях работы при переменных во времени нагрузках шов - вогнутый, но - и наиболее сложный в изготовлении. Применяется в специальных случаях, когда дополнительные расходы, связанные с его выполнением, целесообразны. Выпуклый шов также сложен в изготовлении, имеет повышенную концентрацию напряжений и применяется в специальных случаях. Наиболее распространенное сечение шва – нормальное (треугольное). Опасное сечение шва - сечение АА по высоте прямоугольного равнобедренного треугольника h=0,7k. Редко применяется шов в виде неравнобедренного треугольника. Общие рекомендации по выбору катета (калибра) шва k в пределах 3 мм ≤k≤10 мм при выполнении шва в один проход; k≈δ min , где δ min - меньшая толщина соединяемых деталей. При конструировании соединений следует, если можно, избегать разных толщин соединяемых деталей.
Угловые швы условно делят на лобовые (расположенные перпендикулярно) и фланговые (расположенные вдоль растягивающей или сжимающей внешней силы).
При нагружении угловых швов напряжения, возникающие в опасном сечении шва по длине шва, и в основном металле в зоне термического влияния, - далеко неравномерные. Эта неравномерность учитывается в рекомендациях по геометрическим параметрам шва и в определении [τ]’. Принято ограничивать длину фланговых швов l ф <60k, соотношение длин фланговых и лобовых швов l ф ≤l л: это позволяет упрощать расчет. Длина силового шва l ш ≥30 мм.
При разработке конструкции соединения внахлестку фланговыми швами из условия равнопрочности шва и основного металла рекомендуется применять величину нахлестки не более L н =1,2b, а при соединении комбинированным швом - не более L н =0,7b , где b - расстояние между фланговыми швами.
Фланговые (продольные) швы делают прерывистыми.
Лобовые (поперечные) швы по длине не ограничивают.
В случае симметричного сварного стыка относительно фланговых швов длины фланговых швов делают одинаковыми.
В случае сварного соединения внахлёстку деталей, не имеющих осей симметрии, длины фланговых швов принимают обратно пропорциональными расстоянию швов до осей, проходящих через центр тяжести стыка.
В случае применения нахлестки, выполненной косым швом, угол наклона шва из условия равнопрочности шва и основного металла принимают близким к 30˚.
При использовании угловых швов расчет ведут при следующих предположениях (допущениях):
1.Свариваемые детали - абсолютно жесткие: деформируются под нагрузкой только швы.
2. Под действием крутящих моментов происходит поворот соединенных деталей относительно центра тяжести сварного стыка в пределах упругих деформаций шва.
3. В опасном сечении шва возникает сложное напряженное состояние. Однако расчет угловых швов при любом способе напряжений ведут по касательным напряжениям. Нормальные напряжения не учитывают.
4. Считают касательные напряжения равномерно распределенными по высоте опасного сечения h оп = 0,7k.
5. Опасное сечение углового шва расположено под углом 45˚.
6. Вид сварки выбран правильно, а качество детали и шва удовлетворяет нормам расчета соединений с угловым швом.
При нагружении соединения внахлестку сдвигающим силами и крутящим моментом применяют метод суперпозиции.
Если действует F x , то
Если действует сила F y , то
Если действует крутящий момент Т, то
где - площадь шва,
J ρ Ш - полярный момент инерции площади шва шириной 0,7k относительно центра тяжести сварного стыка О,
ρ max - расстояние от центра тяжести стыка до наиболее удаленной точки сварного шва.
[τ]’ - допускаемое напряжение на срез для шва.
В случае действия одновременно трёх силовых факторов расчет ведут по суммарному τ max
При действии осевой растягивающей (или сжимающей) силы считают, что срез угловых швов происходит по сечению I-I (рис. 19), проходящему через биссектрису прямого угла.
Рис. 19. К расчету соединения внахлестку. Лобовой шов
Проверочный расчет. Условие прочности одностороннего лобового шва на срез:
где - расчетное и допускаемое напряжения среза для шва (см. табл.5); l ш - длина шва;
Проектировочный расчет. Длину одностороннего лобового углового шва (см. рис. 19) при осевом нагружении определяют по формуле
длина двустороннего лобового углового шва
Рассмотрим случай, когда лобовой шов нагружен моментом (рис. 19.1).
Рис.19.1
Касательные напряжения в сечении m-m определяются как τ=M/W,
где - момент сопротивления сечения изгибу.
Тогда
Фланговые угловые швы (см. рис.9, б) рассчитывают по уравнению (6), т.е. аналогично рассмотренному случаю расчета двустороннего лобового шва. Во фланговых швах нагрузка по длине шва распределяется неравномерно (по концам шва увеличивается), поэтому длину фланговых швов стараются ограничить l ш < (50÷60)К.
Если в нахлесточном соединении угловые швы не обеспечивают требуемой прочности, то дополнительно к угловым применяют пробочные (рис. 19.2, а), прорезные (рис. 19.2, б), и проплавленные швы (рис.19.2, в).
Пробочный шов получается путем заполнения расплавленным металлом отверстий круглой формы в одной или обеих соединяемых деталях. Прорези прорезных швов могут быть закрытыми или открытыми. Из-за высокой трудоёмкости изготовления, низкой прочности и негерметичности – это один из худших видов соединений. Проплавленные швы – более производительны.
а) б) в)
Рис.19.2
Рассмотрим соединение деталей фланговыми швами различной длины.
В случае несимметричных угловых фланговых швов, посредством которых приваривают деталь несимметричного профиля, например уголок, каждый из этих швов рассчитывают по своей нагрузке (рис.19.3).
Рис.19.3
Сила F проходит через центр тяжести сечения уголка. Силы F 1 и F 2 , действующие на швы, определяют так:
Очевидно, что длины швов в этом соединении при одинаковых сечениях должны быть пропорциональны нагрузкам
Стыковые соединения. Для удобства передачи силовых пото-ков наиболее совершенными являются соединения встык, так как в них практически нет отклонений этих потоков, а следовательно, по-чти отсутствуют концентрации напряжений.
Поэтому из всех сварных соединений под динамической нагруз-кой лучше работают соединения встык. Кроме того, эти соедине-ния экономичны по затрате материалов. Основной недостаток сты-ковых соединений — необходимость весьма точно резать соединя-емые элементы, а часто и разделывать кромки.
Ручную сварку встык можно вести без специальной обработки кромок при толщине t соединяемых элементов до 8 мм, а при автома-тической — до t= 20 мм (рисунок ниже). При большей толщине элементов кромки для удобства сварки и для обеспечения полного провара разде-лывают (скашивают под углом). Скосы можно делать только с одной стороны (V- и U- образные швы, рисунки ниже) или с двух сторон (X- и К-образные швы, рисунки ниже). Односторонняя сварка проще в отношении производства работ, допускает контроль за проваром кор-ня шва (где больше всего дефектов) и последующее усиление со сто-роны корня (обратная подварка). Однако при односторонней сварке из-за усадки швов происходит коробление свариваемых элементов.
Разделка кромок стыковых сварных соединений
При двусторонней сварке (X- и К- образные швы) меньше объем шва, а следовательно, и ниже расход наплавленного металла. Этот фактор, а также симметричность расположения шва благоприятно отражаются на усадочных деформациях. Недостаток двусторонней сварки — трудность контроля за качеством провара средней части (корня шва) повышенная сложность изготовления, так как необхо-димо вести сварку с двух сторон, для чего изделие приходится кан-товать. В начале и конце шва наплавленный металл получается низкого качества. Для устранения этого недостатка следует начинать и заканчивать сварку на специальных подкладках — выводных планках, временно удлиняющих швы (рисунок ниже). По окончании сварки эти планки вместе с начальными и конечными участками шва сре-зают, а торцы швов и прилегающие участки зачищают.
В случае соединения стыковым швом листов разной толщины переходцть от большей толщины к меньшей можно за счет соответствующего оформления наружной поверхности шва (рисунок ниже) только при условии, если разница в толщинах не более 4 мм, а величина уступа в месте стыка не превышает 1/8 толщины более тонкого листа.
Устройство стыкового шва в листах разной толщины
При большей разнице в толщинах и при динамических нагруз-ках следует предусматривать скосы у более толстого листа с укло-ном до 1:5 (рисунок ниже). За расчетную толщину стыкового шва при-нимаю толщину соединяемых элементов, а если толщина их раз-лична, то толщину более тонкого элемента (без учета наплавленного валика сверху). Расчётной длиной шва l w , считают фактическую его длину за вычетом 2t, учитывающих непровар в начале и конце шва. Если сварка была начата и закончена на выводных планках, то умень-шение длины шва не производят.
Напряжения в шве проверяют но формуле
где N - расчетное усилие; R wy — расчетное сопротивление сварно-го соединения встык растяжению или сжатию.
Расчетные сопротивления растяжению сварных соединений, выполненных ручной или полуавтоматической сваркой, при обычных способах контроля за качеством шва ниже, чем расчетные сопротив-ления основного стыкуемого металла, и потому прямой стык, выпол-ненный такой сваркой, не будет равнопрочен основному металлу. Для получения равнопрочного соединения применяют косой шов, кото-рый делают с наклоном 2:1 (см. рисунок ниже).
При действии изгибающего момента М на соединение нормаль-ные напряжения в шве
где Ww = tl 2 w / 6 — момент сопротивления шва.
В сварных соединениях встык, работающих одновременно на изгиб и срез, проверяют приведенные напряжения по формуле
где σ w — нормальные напряжения от изгиба; тw = Q/(tl w) — среднее касательное напряжение от срезающей силы, определенное из ус-ловия равномерного распределения по стыковому шву.
Соединение внахлестку. Такое соединение выполняют с наклад-ками или без них с помощью угловых швов. В зависимости от распо-ложения швов по отношению, к направлению передаваемого усилия различают фланговые швы (рисунок ниже), расположенные параллельно усилию, и лобовые швы, расположенные перпендикулярно усилию.
Соединение с фланговыми швами (а), направление потока силовых линий и распределение напряжений (б)
Простота соединения внахлестку, для которого не требуется точ-ной подгонки и обработки кромок, а только очистка, удаление зау-сениц и правка, является причиной широкого распространения это-го вида сварного соединения. Недостаток его — сильное искаже-ние силового потока при передаче усилия с одного элемента на другой и связанная с этим концентрация напряжений, вызываемая одновременной работой шва на срез и изгиб.
При соединении фланговыми швами неравномерная передача уси-лия происходит как по длине шва, так и по поперечному сечению со-единения (рисунок выше). По длине наиболее интенсивна передача усилий на концах швов, где разность напряжений в соединяемых элементах наибольшая. Однако перед разрушением шва за счет пластической ра-боты перенапряженных участков (начального и конечного) происхо-дит выравнивание напряжений. Это позволило положить в основу рас-чета допущение о равномерном распределении напряжений среза по минимальной площади сечения шва. Разрушение шва может происхо-дить как по металлу шва (рисунок ниже), так и по основному ме-таллу на границе его сплавления с металлом шва (рисунок ниже), особенно если наплавленный металл прочнее основного.
Лобовые швы (рисунок ниже) более равномерно передают усилия по ширине, чем фланговые. Однако вследствие резкого изменения на-правления потока силовых линий (рисунок ниже) в корне шва концент-рируются большие напряжения (рисунок ниже); в результате разрушение шва происходит при малых удлинениях (ε = 3—4%), т. е. хрупко.
Соединение с лобовыми швами
Неравномерность распределения напряжений приводит к сни-жению качества соединения. Поэтому независимо от вида работы (сжатие, растяжение, срез) расчет лобовых швов условно ведут на срез по минимальной площади сечения шва. При соединении внах-лестку с лобовыми швами длину нахлестки следует назначать не менее пяти толщин более тонкого элемента (см. рисунок ниже). Это позво-ляет уменьшить влияние дополнительного изгибающего момента.
Нормальный угловой шов в разрезе имеет форму прямоуголь-ного равнобедренного треугольника с криволинейной гипотенузой (рисунок ниеже).
Обычный наплыв выпуклого шва составляет 0,1 размера его ка-тета k f . В конструкциях, непосредственно воспринимающих динамические нагрузки, с целью снижения концентрации напряжений в угловых лобовых швах применяют пологие швы с отношением ка-тетов 1:1,5 (рисунок ниже) или вогнутые швы (рисунок ниже).
Поперечные сечения угловых швов
а — нормальный выпуклый; б— пологий выпуклый; в — вогнутый
Минимальный катет-шва в конструкциях, работающих на ста-тическую нагрузку, при автоматической и полуавтоматической сварке — 3 мм, при ручной сварке — 4 мм, а при динамических нагрузках — 6 мм. Швы имеют градацию через 1 мм. Кроме того, наименьший катет однопроходных угловых швов ограничен в зави-симости от толщины более толстого из свариваемых элементов. В таблице ниже приведены минимальные значения катетов угловых швов для основных групп конструкций. Наибольшее значение катета уг-лового шва в зависимости от толщины соединяемых элементов мо-жет быть принято k f = 1,2t, где t — наименьшая из толщин сварива-емых элементов.
Из-за большой концентрации напряжений в начале и конце шва длина углового шва должна быть не менее 40 мм или 4k f (при дина-мических нагрузках 60 мм или 6k f). Наибольшая длина фланговых швов также ограничена и не должна превышать 85 β f k f (β f — коэф-фициент глубины проплавления угловых швов, принимаемый по таблице ниже), так как фактические напряжения по длине шва распреде-лены неравномерно и при длинных швах его крайние участки ис-пытывают перенапряжение, а средние — недонапряжения против расчетного значения. Это ограничение не распространяется на та-кие швы, у которых усилие возникает по всей длине, например на поясные швы балок.
Минимальные значения k f угловых сварных швов
Коэффициент глубины проплавления угловых швов β
Вид сварки при диаметре сварочной про-волоки d, мм |
Положение шва |
Коэф-фи-- |
Значение β при катетах швов, мм |
|||
Автоматическая |
В лодочку |
|||||
Автоматическая и полуавтоматиче-ская при |
В лодочку |
|||||
Нижнее, горизонтальное, вертикальное |
||||||
Ручная; полуавтоматическая проволокой сплошного сечения при d ≤ 1,4 или порошковой проволокой |
В лодочку, нижнее, гори-зонтальное, вертикальное, потолочное |
|||||
Примечание. Швы «в лодочку» применяют для поясных швов в балках и колоннах
Расчет как фланговых, так и лобовых швов производят по их наи-меньшему сечению βk f , который называют расчетным (см. рисунок ниже).
При этом у выпуклых швов выпуклость не учитывают. В угло-вых швах, выполненных автоматом или полуавтоматом, получается более глубокое проплавление, чем при обычной ручной сварке, что и следует учитывать в расчете.
Напряжения принимают равномерно распределенными по длине шва и рассматривается возможность разрушения шва от услов-ного среза по одному из двух сечений (см. рисунок ниже):
- по металлу шва (сечение I-I)
- по металлу границы сплавления (сечение II-II)
где β f и β z — коэффициенты глубины проплавления шва, принима-емые по таблице ниже в зависимости от вида сварки и положения шва для сталей с пределом текучести до 580 МПа; k f — катет шва; l w — расчетная длина шва, принимаемая меньше его фактической длины на 10 мм за счет непровара на концах шва; R wf — расчетное сопро-тивление условному срезу металла шва по таблице ниже; γ wf и γ wz — ко-эффициенты условий работы шва, равные 1 для сварных конструк-ций, работающих при температуре не ниже -40 °С; R wz = 0,45R un — расчетное сопротивление условному срезу металла границы сплавления (значения R un = σ в).
Обычно в расчетах определяют необходимую фактическую длину шва, задаваясь катетом шва k f (используя для этого приведенные ранее рекомендации):
Расчет производят по двум сечениям (по металлу шва, прини-мая β f и R Wf и по металлу границы сплавления, учитывая β z и R wz). Большее из двух значений принимают за длину шва.
Как говорилось выше, из-за неравномерного распределения на-пряжений в длинных угловых швах в расчет можно вводить только длину l w = β f k f Если расчетная длина шва, полученная по форму-ле выше, окажется больше, то определяют необходимый катет шва по формуле
При действии изгибающего момента на прямоугольный эле-мент, прикрепленный угловыми швами (рисунок ниже), напряжения в швах по двум сечениям определяют как напряжения изгиба в двух прямоугольных сечениях, принимая за ширину прямоугольника расчетное сечение шва (β f k f или β z k f), а за высоту — расчетную длину шва (l w):
При действии сдвигающей силы на элемент, прикрепленный угловыми швами (рисунок ниже), напряжения в каждом из двух швов определяют по формулам ниже, заменяя в них N на Q.
Схемы к расчету угловых швов
Если на элемент одновременно действуют момент и сдвигаю-щая сила, то результирующие (равнодействующие) напряжения в угловых швах
√σ 2 w +τ 2 w ≤ R w γ w γ c
Эти напряжения не следует путать с приведенными напряжени-ями в стыковых швах (см. формулу ниже).
В случае прикрепления фланговыми швами несимметричных элементов, например уголков, желательно, чтобы линия действия усилия проходила через центр тяжести соединения, т. е. площади швов должны быть распределены обратно пропорционально их рас-стояниям до центра тяжести элемента.
У равнополочных уголков с шириной полки b принимают рассто-яние от центра тяжести уголка до обушка z 0 = 0,3b. Тогда для прикреп-ления уголка (рисунок ниже) с усилием N требуется длина сварного шва:
со стороны обушка:
со стороны пера:
Крепление несимметричного профиля (уголка) фланговыми швами
Для неравнополочных уголков, прикрепленных меньшей пол-кой, в формулах выше коэффициенты перед N меняются соответственно на 0,75 и 0,25. Комбинированные соединения пред-ставляют собой соединения, в которых имеется несколько различ-ных видов сварных швов: фланговые, лобовые, стыковые. Простей-ший вид стыкового соединения — соединения с накладками, обва-ренными по всему контуру.
Соединение впритык применяют в случае соединения листов под прямым углом. Вследствие своей простоты оно имеет широкое применение. Для расчетных соединений используют соединение в тавр, для нерасчетных связующих — угловое соеди-нение.
Лекция № 25. Расчет сварных соединений.
При изготовлении металлических конструкций часто применяется сварка с помощью электрической дуги.
Впервые электрическая дуга была открыта русским ученым проф. В. В. Петровым в 1802 г. Обнаружив плавление металла в пламени полученной им электрической дуги, проф. Петров указал на возможность использования этого явления в технике. Однако электрическая дуговая сварка была изобретена лишь в конце XIX века русскими инженерами Н. Н. Бенардосом (1882 г.) нашим земляком и Н. Г. Славяновым (1888 г.) и получила впоследствии широкое распространение во всем мире.
Сущность электросварки по методу Славянова заключается в том, что, расплавляя электрической дугой материал электрода (сталь), заполняют им стык соединяемых элементов, также прогреваемых дугой до температуры плавления. В результате, после остывания расплавленного металла, образуется шов, прочно соединяющий стыкуемые элементы. Схема сварки показана на Рис.1. Электрическая дуга горит между металлическим электродом и свариваемым металлом, расплавляя электрод и кромки соединяемых элементов металла, между которыми образуется так называемая сварочная ванна.
Рис.1. Технологическая схема сварки.
Для защиты плавящегося металла от попадания вредных включений из окружающего воздуха на поверхность электрода наносится толстая защитная обмазка, выделяющая при плавлении электрода большое количество шлака и газов, благодаря чему плавящийся металл изолируется от окружающего воздуха.
Этим обеспечивается высокое качество металла сварного шва, механические свойства которого могут резко ухудшиться под влиянием кислорода и азота воздуха (при отсутствии обмазки или при тонкой обмазке). С той же целью автоматическая сварка производится под слоем флюса, защищающим плавящийся металл от попадания кислорода и азота воздуха.
При правильном выборе конструкции соединений, материалов и технологии сварки сварные соединения по надежности не уступают заклепочным при действии как статических, так и динамических нагрузок (в том числе ударных и знакопеременных). В то же время электросварка имеет ряд преимуществ перед клепкой, из которых важнейшими являются меньшая трудоемкость сварочных работ и отсутствие ослабления сечений соединяемых элементов отверстиями. Это дает значительную экономию средств и металла, помимо экономии, получаемой за счет большей компактности соединений. Большие экономические выгоды, приносимые электросваркой, и даваемое ею упрощение конструкций привели в последнее время к постепенному вытеснению заклепочных соединений сварными.
Значительное развитие электросварка получила в СССР благодаря трудам советских ученых Патона, Вологдина, Никитина, Хренова и др., разработавших новые методы сварки, обеспечивающие высокую прочность соединений.
Методы расчета сварных соединений тесно связаны с технологией сварки, причем для многих видов соединений расчет носит весьма условный характер. Вообще методику расчета сварных соединений нельзя еще считать установившейся.
Что касается норм допускаемых напряжений для материала швов, то они принимаются различными в зависимости от способа сварки (ручная и автоматическая), а также от состава и толщины защитной обмазки электродов.
В таблице приведены допускаемые напряжения для сварных швов в конструкциях из стали марки ст. 3 по существующим нормам.
Таблица.
Допускаемые напряжения при сварке.
При проверке прочности сварных швов учитывается возможный непровар в начале шва и образование кратера в конце. Поэтому расчетная длина шва принимается меньшей, чем действительная или проектная на 10 мм .
Необходимо отметить, что наиболее простым и надежным видом соединения является соединение встык, образуемое путем заполнения зазора между торцами соединяемых элементов наплавленным металлом. Соединение встык осуществляется, в зависимости от толщины соединяемых элементов, по одному из типов, показанных на Рис.2. Проверка прочности производится на растяжение или сжатие по формуле:

Рис.2. Расчетная схема сварного соединения.
Здесь условная рабочая площадь сечения шва, где расчетная длина шва , а высота шва h принимается равной толщине свариваемых элементов t .
Поскольку допускаемое напряжение для сварного шва ниже, чем для основного металла, стремятся к увеличению длины стыкового шва. С этой целью применяют соединение встык с косым швом (Рис.3). Исследования таких соединений, произведенные Институтом электросварки Академии наук УССР, показали, что равнопрочность их с основным металлом всегда обеспечивается.
Проверка прочности косых швов производится и по нормальным и по касательным напряжениям, возникающим по сечению шва mn :
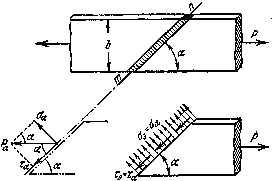
Рис.3. Расчетная схема косого сварного соединения.
Имея в виду, что получим:
Здесь расчетная длина шва по техническим условиям принимается равной .
Как установлено опытом, наиболее рациональным углом наклона шва к линии действия сил является . Недостатком соединения косым швом является неудобство центрировки стыкуемых элементов при сварке, поэтому его применяют редко.
Иногда соединение листов производится внахлестку или встык с перекрытием накладками. Это вызывает необходимость сваривать листы, не лежащие в одной плоскости, что осуществляется при помощи так называемых валиковых (или угловых) швов лобовых или торцевых (перпендикулярных к направлению действующей силы) и боковых или фланговых (параллельных ей).
Валиковый шов в сечении имеет довольно неопределенную форму (Рис.104). В теоретических расчетах на прочность сечение шва принимается в виде равнобедренного треугольника (очерченного пунктиром) с расчетной высотой ).
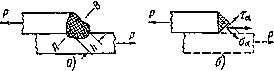
А) технология. б) расчетная схема
Рис.4.
Сварное соединение внахлестку:
Соединения торцевыми(лобовыми) швами показаны на рис.5. Разрушение таких швов происходит по наиболее слабому сечению AB , как это установлено опытами.
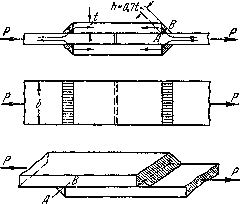
Рис.5. Сварное соединение торцевыми швами.
Как это видно из рис. 4 б , полное напряжение, возникающее в сечении АВ , может быть разложено на нормальную и касательную составляющие. Поскольку сопротивление стали сдвигу ниже, чем при растяжении, расчет лобовых швов производится условно на срез в предположении равномерного распределения касательных напряжений по площади сечения АВ . Имея в виду, что на восприятие силы Р в этих соединениях (Рис.5) работают два лобовых шва, верхний и нижний, получим:
Так как площадь сечения шва , а расчетная длина , то условие прочности примет вид:
В действительности, материал шва испытывает сложное напряженное состояние, причем напряжения по сечению АВ распределяются неравномерно. Исследования, произведенные методами теории упругости и подтвержденные экспериментально, показали, что в углах шва имеет место высокая концентрация напряжений.
Если учесть, что, вследствие укорочения швов при остывании, в зоне сварки возникают дополнительные напряжения и в основном металле, ведущие к переходу его в хрупкое состояние, то следует иметь в виду, что концентрация напряжений может явиться причиной появления трещин в основном металле соединения.
Соединение фланговыми (или боковыми) швами показано на Рис.6 а. Разрушение шва, показанное на Рис.6 б , происходит на значительном его протяжении путем срезывания наплавленного металла в направлении, параллельном шву по наиболее слабой плоскости АВ .
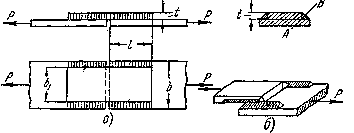
Рис.6. Соединение фланговыми швами- а) и его разрушение б)
Условие прочности для двух симметрично расположенных швов имеет вид:
Если стык перекрыт двухсторонними накладками, число швов удвоится и условие прочности примет вид:
Отсюда обычно определяют необходимую расчетную длину фланговых швов. Проектная же длина каждого шва принимается равной .
Как показали опыты, разрушение фланговых швов происходит по типу разрушений пластичных материалов со значительными остаточными деформациями. Это делает работу фланговых швов более благоприятной, чем работу лобовых швов. Однако следует иметь в виду, что у концов фланговых швов также имеет место высокая концентрация напряжений.
При проектировании часто стремятся обеспечить большую надежность соединения, применяя вместо сварки встык, или в дополнение к ней, перекрытие стыка накладками, которые привариваются фланговыми или торцевыми швами, а иногда и теми и другими вместе. Как уже указывалось, при переменных и ударных нагрузках такое «усиление» стыка может принести больше вреда, чем пользы.
Что касается расчета такого комбинированного стыка, то при одновременном применении лобовых и фланговых швов считают, что сопротивление соединения равно сумме сопротивлений всех швов, т. е. , где сопротивление торцевого шва при расчетной длине равно , а сопротивление двух фланговых швов
, причем , где b
ширина накладки. В результате подстановки получаем:
Зная длину торцевого шва, определяют длину фланговых швов .При двухсторонних накладках число швов удваивается, т. е. правую часть полученного соотношения следует удвоить.
Так как торцевые швы более жестки, то при совместной работе с фланговыми они перегружаются, что ведет к неравномерной работе соединения. Если учесть, что в таком соединении и термические напряжения достигают больших значений, то устройства такого стыка следует избегать.
Иногда при соединении внахлестку, в дополнение к фланговым швам, применяют прорезные швы, осуществляемые путем наплавки металла в узкую прорезь, сделанную в одном из соединяемых элементов параллельно действующему на соединение усилию.
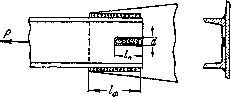
Рис.7. Комбинация фланговых и прорезных швов
При длине прорезного шва и ширине прорези d сопротивление такого шва срезу равно:
где усилие, приходящееся на прорезной шов.
В комбинированном соединении с фланговыми швами для записи расчетного условия принимают, что или
Задавшись размерами одного из швов (обычно флангового), находят необходимую длину другого. При этом ширина прорези d принимается равной двойной толщине прорезанного металла, длина не более двадцати толщин.
Недостатками соединения с прорезными швами являются: 1) ослабление сечения прорезями вследствие неизбежного непровара и 2) высокая концентрация напряжений в основном металле в зоне сварки, ведущая к появлению трещин около углов прорезного шва; поэтому такое соединение может применяться лишь в крайних случаях, при условии хорошо продуманной технологии сварочных работ.
В заключение заметим, что в том случае, когда приходится прибегать к соединению внахлестку, лучше всего ограничиться одними фланговыми швами, избегая комбинированных соединений.
Соединения встыкобычно выполняются лобовыми швами. При качественной сварке соединения разрушаются не по шву, а в зоне температурного влияния. Поэтому рассчитываются на прочность по сечению соединяемых деталей без учёта утолщения швов. Наиболее частые случаи – работа на растяжение и на изгиб.
Эти виды швов в различных сочетаниях применяются в разных соединениях.
Расчёт на прочность сварных швов
По ориентации относительно приложенных сил различают:
è лобовые швы – перпендикулярные силам;
è фланговые швы – параллельны силам;
è косые швы – под углом к силам.
Напряжения растяжения: s раст = Q / S = Q / bd ≤ [ s раст ] шва .
Напряжения изгиба: s изг = M изг / W = 6 M изг / bd 2 ≤[ s изг ] шва .
Допускаемые напряжения шва [ s раст ] шва и [ s изг ] шва принимаются в размере 90% от соответствующих допускаемых напряжений материала свариваемых деталей.
Лобовые швы в инженерной практике рассчитывают только по касательным напряжениям. За расчётное сечение принимают биссектрису m -m , где обычно наблюдается разрушение. Расчёт только по касательным напряжениям не зависит от угла приложения нагрузки.
При этом τ = Q / (0,707 k l ) ≤[ τ" ] шва .
Фланговые швы характерны неравномерным распределением напряжений, поэтому их рассчитывают по средним касательным напряжениям. При действии растягивающей силы касательные напряжения равны:
τ = Q / (2*0,707 d l ) ≤[ τ" ] шва .
При действии момента: τ = M / (0,707 k d l ) ≤[ τ" ] шва .
Если швы несимметричны, то нагрузка на фланговые швы распределяется по закону рычага Q 1,2
=
Q l 1,2 /
(l 1
+
l 2
)
, где l 1
и l 2
– длины швов.
При этом швы рассчитывают по соответствующим нагрузкам, а длины швов назначают пропорционально этим нагрузкам. Касательные напряжения в швах τ 1,2
= Q 1,2 / (1,414 d l 1,2)
≤ [τ"] шва
.
Косые швы рассчитываются аналогичным образом. Нагрузка Q раскладывается на проекции в продольном и нормальном направлениях к шву, а далее выполняются расчёты лобового и флангового швов.
Комбинированные
лобовые и фланговые швы рассчитывают на основе принципа распределения нагрузки пропорционально несущей способности отдельных швов. При действии силы Q
касательные напряжения равны:
τ Q = Q / [0,707 k (2 l ф + l л )] ≤[ τ" ] шва .
Если действует момент M , то
τ M = M / [0,707 k l л (l ф + l л /6 )] ≤[ τ" ] шва .
При совместном действии силы и момента касательные напряжения складываются τ = τ М + τ Q ≤[ τ" ] шва .
Тавровые и угловые швы
соединяют элементы в перпендикулярных плоскостях. Выполняются либо стыковым швом с разделкой кромок (а), либо угловым без разделки кромок (б). При нагружении изгибающим моментом и силой прочность соединения оценивают:
для стыкового шва (а) по нормальным напряжениям
s = 6M/ (bd 2 )+ Q / (ld ) ≤[ s раст ] шва ,
для углового шва (б) по касательным напряжениям
τ = 6M/ (1,414 l 2 k )+ Q / (1,414 l k ) ≤[ τ" ] шва .
В любом случае для расчёта самых сложных сварных швов сначала необходимо привести силу и момент к шву и распределить их пропорционально несущей способности (длине) всех простых участков. Таким образом, любой сложный шов сводится к сумме простейших расчётных схем.